EP2AGX190FF35C6N Altera, EP2AGX190FF35C6N Datasheet - Page 352
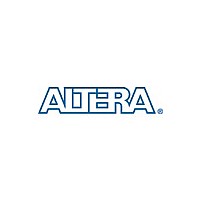
EP2AGX190FF35C6N
Manufacturer Part Number
EP2AGX190FF35C6N
Description
IC ARRIA II GX 190K 1152FBGA
Manufacturer
Altera
Series
Arria II GXr
Datasheets
1.EP2AGX45CU17C6N.pdf
(96 pages)
2.EP2AGX45CU17C6N.pdf
(14 pages)
3.EP2AGX45CU17C6N.pdf
(692 pages)
4.EP2AGX45CU17C6N.pdf
(10 pages)
5.EP2AGX45CU17C6N.pdf
(88 pages)
6.EP2AGX190FF35C6N.pdf
(306 pages)
Specifications of EP2AGX190FF35C6N
Number Of Logic Elements/cells
181165
Number Of Labs/clbs
7612
Total Ram Bits
9939
Number Of I /o
612
Voltage - Supply
0.87 V ~ 0.93 V
Mounting Type
Surface Mount
Operating Temperature
0°C ~ 85°C
Package / Case
1152-FBGA
Family Name
Arria® II GX
Number Of Logic Blocks/elements
190300
# I/os (max)
612
Frequency (max)
400MHz
Operating Supply Voltage (typ)
900mV
Logic Cells
190300
Ram Bits
10380902.4
Operating Supply Voltage (min)
0.87V
Operating Supply Voltage (max)
0.93V
Operating Temp Range
0C to 85C
Operating Temperature Classification
Commercial
Mounting
Surface Mount
Pin Count
1152
Package Type
FC-FBGA
Lead Free Status / RoHS Status
Lead free / RoHS Compliant
Number Of Gates
-
Lead Free Status / Rohs Status
Compliant
Available stocks
Company
Part Number
Manufacturer
Quantity
Price
- EP2AGX45CU17C6N PDF datasheet
- EP2AGX45CU17C6N PDF datasheet #2
- EP2AGX45CU17C6N PDF datasheet #3
- EP2AGX45CU17C6N PDF datasheet #4
- EP2AGX45CU17C6N PDF datasheet #5
- EP2AGX190FF35C6N PDF datasheet #6
- Current page: 352 of 692
- Download datasheet (22Mb)
10–2
Configuration Error Detection
User Mode Error Detection
Arria II Device Handbook Volume 1: Device Interfaces and Integration
In configuration mode, a frame-based CRC is stored in the configuration data and
contains the CRC value for each data frame.
During configuration, the Arria II device calculates the CRC value based on the frame
of data that is received and compares it against the frame CRC value in the data
stream. Configuration continues until either the device detects an error or
configuration is complete.
In Arria II devices, the CRC value is calculated during the configuration stage. A
parallel CRC engine generates 16 CRC check bits per frame and then stores them into
the configuration RAM. The configuration RAM chain used for storing CRC check
bits is 16 bits wide and its length is equal to the number of frames in the device.
Arria II devices have built-in error detection circuitry to detect data corruption by soft
errors in the configuration RAM cells. This feature allows all configuration RAM
contents to be read and verified to match a configuration-computed CRC value. Soft
errors are changes in a configuration RAM’s bit state due to an ionizing particle.
The error detection capability continuously calculates the CRC of the configured
configuration RAM bits and compares it with the pre-calculated CRC. If the CRCs
match, there is no error in the current configuration RAM bits. The process of error
detection continues until the device is reset by setting nCONFIG low.
To enable the error detection process when the device transitions into user mode, turn
on the Enable Error Detection CRC option on the Error Detection CRC page of the
Device and Pin Options dialog box in the Quartus II software.
A single 16-bit error detection CRC calculation is done on a per-frame basis. After the
error detection circuitry has finished the CRC calculation for a frame, the resulting
16-bit signature is hex 0000. If the error detection circuitry detects no configuration
RAM bit errors in a frame, the output signal CRC_ERROR is 0. If the circuitry detects a
configuration RAM bit error in a frame in the device, the resulting signature is
non-zero and the error detection circuitry starts searching for the error bit location.
The error detection circuitry in Arria II devices calculates CRC check bits for each
frame and pulls the CRC_ERROR pin high when it detects bit errors in the chip. Within a
frame, it can detect all single-bit, double-bit, and triple-bit errors. The probability of
more than three configuration RAM bits being flipped by a single event upset (SEU) is
very low. In general, the probability of detection for all error patterns is 99.998%.
The error detection circuitry reports the bit location and determines the type of error
for all single-bit errors and over 99.641% of double-adjacent errors. The probability of
other error patterns is very low and the reporting of bit location is not guaranteed.
You can also read the error bit location through the JTAG and the core interface.
Before the error detection circuitry detects the next error in another frame, you must
shift erroneous bits out from the error message register (EMR) with either the JTAG
instruction, SHIFT_EDERROR_REG, or the core interface. The CRC circuitry continues to
run, and if an error is detected, you must decide whether to complete the
reconfiguration or to ignore the CRC error.
Chapter 10: SEU Mitigation in Arria II Devices
December 2010 Altera Corporation
Configuration Error Detection
Related parts for EP2AGX190FF35C6N
Image
Part Number
Description
Manufacturer
Datasheet
Request
R

Part Number:
Description:
CYCLONE II STARTER KIT EP2C20N
Manufacturer:
Altera
Datasheet:

Part Number:
Description:
CPLD, EP610 Family, ECMOS Process, 300 Gates, 16 Macro Cells, 16 Reg., 16 User I/Os, 5V Supply, 35 Speed Grade, 24DIP
Manufacturer:
Altera Corporation
Datasheet:

Part Number:
Description:
CPLD, EP610 Family, ECMOS Process, 300 Gates, 16 Macro Cells, 16 Reg., 16 User I/Os, 5V Supply, 15 Speed Grade, 24DIP
Manufacturer:
Altera Corporation
Datasheet:

Part Number:
Description:
Manufacturer:
Altera Corporation
Datasheet:

Part Number:
Description:
CPLD, EP610 Family, ECMOS Process, 300 Gates, 16 Macro Cells, 16 Reg., 16 User I/Os, 5V Supply, 30 Speed Grade, 24DIP
Manufacturer:
Altera Corporation
Datasheet:

Part Number:
Description:
High-performance, low-power erasable programmable logic devices with 8 macrocells, 10ns
Manufacturer:
Altera Corporation
Datasheet:

Part Number:
Description:
High-performance, low-power erasable programmable logic devices with 8 macrocells, 7ns
Manufacturer:
Altera Corporation
Datasheet:

Part Number:
Description:
Classic EPLD
Manufacturer:
Altera Corporation
Datasheet:

Part Number:
Description:
High-performance, low-power erasable programmable logic devices with 8 macrocells, 10ns
Manufacturer:
Altera Corporation
Datasheet:

Part Number:
Description:
Manufacturer:
Altera Corporation
Datasheet:

Part Number:
Description:
Manufacturer:
Altera Corporation
Datasheet:

Part Number:
Description:
Manufacturer:
Altera Corporation
Datasheet:

Part Number:
Description:
CPLD, EP610 Family, ECMOS Process, 300 Gates, 16 Macro Cells, 16 Reg., 16 User I/Os, 5V Supply, 25 Speed Grade, 24DIP
Manufacturer:
Altera Corporation
Datasheet: