R88A-CNG01R Omron, R88A-CNG01R Datasheet - Page 411
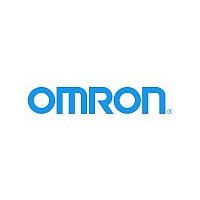
R88A-CNG01R
Manufacturer Part Number
R88A-CNG01R
Description
Encoder Connector ABS Motor
Manufacturer
Omron
Datasheet
1.R88A-CNG01R.pdf
(508 pages)
Specifications of R88A-CNG01R
Lead Free Status / Rohs Status
Lead free / RoHS Compliant
- Current page: 411 of 508
- Download datasheet (22Mb)
Gain Adjustment Methods
Note 1. Take sufficient care for safety.
Note 2. If oscillation occurs (e.g., abnormal sound or vibration), immediately turn OFF the power supply or let the
Automatic
Manual
adjust-
adjust-
ment
ment
servo OFF status occur.
Realtime autotuning
Adaptive filter
Normal Mode Autotuning
Automatic gain adjustment reset
Manual tuning (basic)
Manual tuning (application)
Fit gain function
Basic procedure
Gain switching
Machine resonance suppression
Automatic gain setting
Instantaneous speed observer
Damping control
Function
Realtime autotuning estimates the load inertia of the me-
chanical system in realtime and automatically sets the
optimal gain according to the estimated load inertia.
The fit gain function automatically searches for the appropri-
ate rigidity setting by repeating input of an operation with a
specified pattern to automatically make the rigidity setting for
realtime autotuning when position control is performed.
The adaptive filter reduces resonance point vibration by
estimating the resonance frequency from the vibration com-
ponent that appears in the Servomotor speed during actual
operation and automatically sets the coefficient of the notch
filter, which removes the resonance component from the
torque command.
Normal mode autotuning automatically sets the appropriate
gain by operating the Servomotor with the command pattern
automatically generated by the Servo Drive and estimating
the load inertia from the torque required at that time.
This function disables the default settings for realtime auto-
tuning and the adaptive filter.
Manual tuning is performed if autotuning cannot be executed
due to restrictions on the control mode or load conditions or
if ensuring the maximum responsiveness to match each load
is required.
Position control mode adjustment
Speed control mode adjustment
Torque control mode adjustment
Gain switching can be used with internal data or external sig-
nals to perform such actions as reducing vibration at stop-
ping, shortening stabilization time, and improving command
follow-up.
It is sometimes not possible to set the gain high because of
vibration or sound due to resonance caused by shaft contor-
tion when the machine rigidity is low. In these cases, two
types of filters can be used to suppress resonance.
This function initializes control parameters and gain switch-
ing parameters to settings that match the normal mode auto-
tuning rigidity parameters before manual tuning is
performed.
The following application functions can be used to further
improve performance if the specifications cannot be satisfied
using basic adjustment.
The instantaneous speed observer both increases respon-
siveness and reduces vibration at stopping by estimating the
Servomotor speed using a load model and improving the
speed detection accuracy.
Damping control reduces vibration by removing the vibration
frequency component from the command when the end of
mechanisms or devices vibrates.
Explanation
7-1 Gain Adjustment
Refer-
page
ence
7-11
7-14
7-19
7-22
7-24
7-25
7-26
7-30
7-32
7-33
7-35
7-4
7-7
7-2
7
Related parts for R88A-CNG01R
Image
Part Number
Description
Manufacturer
Datasheet
Request
R

Part Number:
Description:
G6S-2GLow Signal Relay
Manufacturer:
Omron Corporation
Datasheet:

Part Number:
Description:
Compact, Low-cost, SSR Switching 5 to 20 A
Manufacturer:
Omron Corporation
Datasheet:

Part Number:
Description:
Manufacturer:
Omron Corporation
Datasheet:

Part Number:
Description:
Manufacturer:
Omron Corporation
Datasheet:

Part Number:
Description:
Manufacturer:
Omron Corporation
Datasheet:

Part Number:
Description:
Manufacturer:
Omron Corporation
Datasheet:

Part Number:
Description:
Manufacturer:
Omron Corporation
Datasheet:

Part Number:
Description:
Manufacturer:
Omron Corporation
Datasheet: