FX1S-30MR-ES/UL MITSUBISHI, FX1S-30MR-ES/UL Datasheet - Page 224
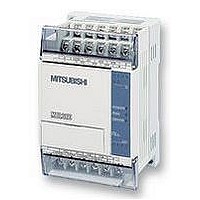
FX1S-30MR-ES/UL
Manufacturer Part Number
FX1S-30MR-ES/UL
Description
PLC, 16 IN, 14 RELAY OUT, 110V/2
Manufacturer
MITSUBISHI
Datasheet
1.FX1S-30MR-ESUL.pdf
(380 pages)
Specifications of FX1S-30MR-ES/UL
No. Of Analogue Inputs
16
No. Of Analogue Outputs
14
Ip/nema Rating
IP10
Approval Bodies
CE, CUL, UL
External Depth
49mm
External Length / Height
90mm
External Width
60mm
Mounting Type
Panel
- Current page: 224 of 380
- Download datasheet (7Mb)
5.9.8
FX Series Programmable Controlers
PID (FNC 88)
correction factor which also takes into account previous iterations and trends of the calculated
error. The PID process calculates a correction factor which is applied to the current output
value and stored as a corrected output value in destination device (D). The setup parameters
for the PID control loop are stored in 25 consecutive data registers S
Points to note:
a) Every PID application is different. There will be a certain amount of “trial and error”
b) On FX
c) The FX1S does not have analog capabilities, it is therefore neccessary to use RS232
d) As 25 data register are required for the setup parameters for the PID loop, the head address
e) There are control limits in the PLC intended to help the PID controlled machines operate in
f) The PID instruction has a special set of error codes associated with it. Errors are identified
g) A full PID iteration does not have to be performed. By manipulation of the setup parameters
PID
FNC 88
(PID
control loop)
register each
Mnemonic
necessary to set the variables at optimal levels.
initial values for the PID process. Refer to page 10-28 for more details.
communications to achieve basic PID operation.
of this data stack cannot be greater than D975. The contents of this data stack are
explained later in this section. Multiple PID instructions can be programmed, however each
PID loop must not have conflicting data registers.
a safe manner. If it becomes necessary to reset the Set Point Value (S
it is recommended to turn the PID command Off and restore the command after entering the
new Set Point Value. This will prevent the safety control limits from stopping the operation of
the PID instruction prematurely.
in the normal manner. The error codes associated with the PID loop will be flagged by
M8067 with the appropriate error code being stored in D8067. These error devices are not
exclusive to the PID instruction so care should be taken to investigate errors properly.
Please see chapter 6, ‘Diagnostic Devices’ for more information.
P (proportional), I (Integral) or D (derivative) loops may be accessed individually or in a user
defined/selected group. This is detailed later in this section.
2N,
FX
Receives a data
input and
calculates a
corrective action
to a specified
level based on
PID control
2NC
Function
& FX
1N
MPUs a Pre-tuning feature is available that can quickly provide
D
Note: S
use a single
data register
S
1
1
and S
S
2
Operation:
This instruction takes a current value (S
compares it to a predefined set value (S
difference or error between the two values is then
processed through a PID loop to produce a
2
D
Note: S
uses 25
consecutive
data registers
Operands
S
3
3
D
Note: D
uses a single
data register
D
3
+0 through S
Applied Instructions 5
1
) during operation,
PID:
9 steps
Program steps
5-102
3
+24.
1
). The
2
) and
Related parts for FX1S-30MR-ES/UL
Image
Part Number
Description
Manufacturer
Datasheet
Request
R

Part Number:
Description:
MITSUBISHI IGBT MODULES
Manufacturer:
MITSUBISHI
Datasheet:

Part Number:
Description:
MITSUBISHI INTELLIGENT POWER MODULES
Manufacturer:
MITSUBISHI
Datasheet:

Part Number:
Description:
TRANSFER-MOLD TYPE INSULATED TYPE
Manufacturer:
MITSUBISHI
Datasheet:

Part Number:
Description:
Manufacturer:
MITSUBISHI
Datasheet:

Part Number:
Description:
30A intelligent power module for flat-base type
Manufacturer:
MITSUBISHI
Datasheet:

Part Number:
Description:
15A - transistor module for medium power switching use, insulated type
Manufacturer:
MITSUBISHI
Datasheet:

Part Number:
Description:
5A power module for transfer-mold type insulated type
Manufacturer:
MITSUBISHI
Datasheet:

Part Number:
Description:
30A intelligent power module for flat-base type
Manufacturer:
MITSUBISHI
Datasheet:

Part Number:
Description:
TRANSFER-MOLD TYPE INSULATED TYPE
Manufacturer:
MITSUBISHI
Datasheet:

Part Number:
Description:
TRANSFER-MOLD TYPE INSULATED TYPE
Manufacturer:
MITSUBISHI
Datasheet:

Part Number:
Description:
20A - transistor module for medium power switching use, insulated type
Manufacturer:
MITSUBISHI
Datasheet:

Part Number:
Description:
20A - transistor module for medium power switching use, insulated type
Manufacturer:
MITSUBISHI
Datasheet: