F39-EU1E Omron, F39-EU1E Datasheet - Page 741
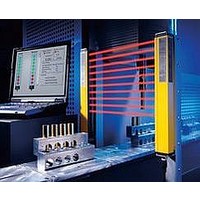
F39-EU1E
Manufacturer Part Number
F39-EU1E
Description
F3S-B OPTIONAL PROGRAMMING KIT
Manufacturer
Omron
Datasheet
1.F39-EU1E.pdf
(865 pages)
Specifications of F39-EU1E
Leaded Process Compatible
No
Peak Reflow Compatible (260 C)
No
Light Curtain Type
Safety
Lead Free Status / RoHS Status
Contains lead / RoHS non-compliant
Lead Free Status / RoHS Status
Contains lead / RoHS non-compliant
- Current page: 741 of 865
- Download datasheet (35Mb)
Courtesy of Steven Engineering, Inc.-230 Ryan Way, South San Francisco, CA 94080-6370-Main Office: (650) 588-9200-Outside Local Area: (800) 258-9200-www.stevenengineering.com
Safety Precautions
Regulations and Standards
Installation Conditions
Refer to “Precautions for All Safety Sensors” for installation
conditions.
Safety Distance
<Reference>
Method for calculating safety distance as provided by
International Standard ISO 13855-2002 (European
Standard EN 999-1999) (for intrusion perpendicular to the
detection zone)
Substitute K = 2,000 mm/s and C = 8 (d – 14 mm) in equation (1)
and calculate as shown below.
Use S = 100 mm if the result of equation (2) is less than 100 mm.
Recalculate using the following equation with K = 1,600 mm/s if the
result is over 500 mm.
Use S = 500 mm if the result from equation (3) is less than
*1. The machine response time is the maximum time from the moment
*2. The light curtain response time is the time required for output to
Always maintain a safe distance (S) between the F3SL
and a hazardous part of a machine.
Failure to do so causes the machine to fail to stop before
an operator reaches the dangerous area and may result
in serious injury.
“Type Certification” specified in the Chapter 44. 2 of the Industrial
Safety and Health Law in Japan does not apply to independent
F3SL Sensors. This law applies to systems incorporating the
Sensor. When using the F3SL Sensor in Japan as a “safety device
for presses or shearing machines,” as specified in the Chapter 42
of the same law, apply for certification for the overall system.
The F3SL is classified under electro-sensitive protective
equipment (ESPE) in the European Union (EU) Machinery
Directive Annex IV, B, Safety Components, Item 1.
The following certification have been obtained for the F3SL from
EU Certification Bodies: EC type certification (type 4 ESPE) under
the Machinery Directive from TÜV Rheinland.
S = 2,000 mm/s × (Tm + Ts) + 8 (d – 14 mm) ........................... (2)
Where: S = Safety distance (mm)
Example:
S = 1,600 mm/s × (Tm + Ts) + 8 (d – 14 mm) ........................... (3)
the machine receives a stop signal to the moment the hazardous
part of the machine stops.
change from ON to OFF.
Tm = 0.05 s, Ts = 0.020 s, d = 30 mm:
S = 2,000 mm/s × (0.05 s + 0.020 s) + 8 (30 mm – 14 mm) =
268 mm
500 mm.
Tm = Machine response time (s) *1
Ts = Safety light curtain response time (s) *2
d = Detection capability of the safety light curtain (mm)
http://www.ia.omron.com/
!WARNING
Distances from Reflective Surfaces
Side view
Install the F3SL with minimum Distance D shown above from
reflective surfaces (highly reflective surfaces) such as metal walls,
floors, ceilings, and work pieces.
Do not used the product in atmospheres or environments that exceed
product ratings
Refer to “Precautions for All Safety Sensors” for information on
preventing mutual interference.
Distance between emitter and
Be sure to install the F3SL to minimize the effects of
reflection from nearby surfaces.
Failure to do so may cause detection to fail and may
result in serious injury.
0.2 to 3 m
3 to 20 m
receiver (Operating range L)
Emitter
(c)Copyright OMRON Corporation 2008 All Rights Reserved.
Reflecting ceiling
Detection zone
Reflecting floor
Precautions for Correct Use
L
D
D
Receiver
Top view
Emitter
0.16 m
L × tan 3° = L × 0.052 (m)
Minimum installation distance
Reflecting surface
3°
3°
L
D
D
F3SL
Receiver
6
Related parts for F39-EU1E
Image
Part Number
Description
Manufacturer
Datasheet
Request
R

Part Number:
Description:
Pair Of Flat Mounting Brackets (transmitter & Receiver)
Manufacturer:
Omron

Part Number:
Description:
Pair Of Protective Shrouds (transmitter & Receiver)
Manufacturer:
Omron

Part Number:
Description:
G6S-2GLow Signal Relay
Manufacturer:
Omron Corporation
Datasheet:

Part Number:
Description:
Compact, Low-cost, SSR Switching 5 to 20 A
Manufacturer:
Omron Corporation
Datasheet:

Part Number:
Description:
Manufacturer:
Omron Corporation
Datasheet: