RDK-252 Power Integrations, RDK-252 Datasheet - Page 26
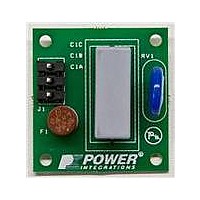
RDK-252
Manufacturer Part Number
RDK-252
Description
KIT REF DESIGN DG CAPZERO
Manufacturer
Power Integrations
Series
CAPZero™r
Type
Other Power Managementr
Specifications of RDK-252
Main Purpose
Automatic X Capacitor Discharge
Embedded
No
Utilized Ic / Part
CAP014DG, CAP002DG, CAP012DG
Primary Attributes
Low No-Load Input Power (
Secondary Attributes
Surge Testing to EN6100-4-5 Class 4
Input Voltage
85 V to 264 V
Board Size
38.1 mm x 25.4 mm
Product
Power Management Modules
Dimensions
38.1 mm x 25.4 mm
Lead Free Status / RoHS Status
Lead free / RoHS Compliant
For Use With/related Products
CAP014DG
Other names
596-1313
Available stocks
Company
Part Number
Manufacturer
Quantity
Price
Company:
Part Number:
RDK-252
Manufacturer:
Power Integrations
Quantity:
135
Rev. A 030910
JX MOSFET. This arrangement was selected over a standard
RCD clamp to improve light load efficiency and no-load input
power.
In a standard RCD clamp C4 would be discharged by a parallel
resistor rather than a resistor and series Zener. In an RCD clamp
the resistor value is selected to limit the peak drain voltage
under full load and overload conditions. However under light or
no-load conditions this resistor value now causes the capacitor
voltage to discharge significantly as both the leakage inductance
energy and switching frequency are lower. As the capacitor has
to be recharged to above the reflected output voltage each
switching cycle the lower capacitor voltage represents wasted
energy. It has the effect of making the clamp dissipation
appear as a significant load just as if it were connected to the
output of the power supply.
The RZCD arrangement solves this problem by preventing the
voltage across the capacitor discharging below a minimum
value (defined by the voltage rating of VR2) and therefore
minimizing clamp dissipation under light and no-load conditions.
Resistors R6 and R28 provide damping of high frequency
ringing to reduce EMI. Due to the resistance in series with VR2,
limiting the peak current, standard power Zeners vs. a TVS type
may be used for lower cost (although a TVS type was selected
due to availability of a SMD version). Diode D2 was selected to
have an 800 V vs. the typical 600 V rating due to its longer
reverse recovery time of 500 ns. This allows some recovery of
the clamp energy during the reverse recovery time of the diode
improving efficiency. Multiple resistors were used in parallel to
share dissipation as SMD components were used.
Feedback Configuration
•
•
•
Typically the feedback current into the CONTROL pin at high
line is ~3 mA. This current is both sourced from the bias
winding (voltage across C10) and directly from the output. Both
of these represent a load on the output of the power supply.
To minimize the dissipation from the bias winding under no-load
conditions the number of bias winding turns and value of C10
was adjusted to give a minimum voltage across C10 of ~9 V.
This is the minimum required to keep the optocoupler biased.
To minimize the dissipation of the secondary side feedback
circuit Q2 was added to form a Darlington connection with U3B.
This reduced the feedback current on the secondary to ~1 mA.
The increased loop gain (due to the h
compensated by increasing the value of R16 and the addition of
R25. A standard 2.5 V TL431 voltage reference was replaced
with the 1.24 V LMV431 to reduce the supply current requirement
from 1 mA to 100 µA.
A Darlington connection formed together with optocoupler
transistor to reduce secondary side feedback current and
therefore no-load input power.
Low voltage, low current voltage reference IC used on
secondary side to reduce secondary side feedback current
and therefore no-load input power.
Bias winding voltage tuned to ~9 V at no-load, high line to
reduce no-load input power.
26
Application Note
FE
of the transistor) was
Output Rectifier Choice
•
A dual 15 A, 100 V Schottky rectifier diode with a V
at 5 A was selected for D5. This is a higher current rating than
required to reduce resistive and forward voltage losses to improve
both full load and average efficiency. The use of a 100 V Schottky
was possible due to the high transformer primary to secondary
turns ratio (V
voltage rating of the TOPSwitch-JX internal MOSFET.
Increased Output Overvoltage Shutdown Sensitivity
•
During an open loop condition the output and therefore bias
winding voltage will rise. When this exceeds the voltage of VR1
plus a V
V pin. The addition of Q1 ensures that the current into the V pin
is sufficient to exceed the latching shutdown threshold even
when the output is fully loaded while the supply is operating at
low line as under this condition the output voltage overshoot is
relatively small
Output overload power limitation is provided via the current limit
programming feature of the X pin and R7, R8 and R9. Resistors
R8 and R9 reduce the device current limit as a function of
increasing line voltage to provide a roughly flat overload power
characteristic, below the 100 VA limited power source (LPS)
requirement. In order to still meet this under a single fault condition
(such as open circuit of R8) the rise in the bias voltage that occurs
during an overload condition is also used to trigger a latching
shutdown.
Very Low No-load, High Efficiency, 30 W, Universal Input,
Open Frame, Power Supply
The circuit shown in Figure 32 below shows an 85 VAC to
265 VAC input, 12 V, 2.5 A output power supply. The goals of
the design were highest full load efficiency, average efficiency
(average of 25%, 50%, 75% and 100% load points), very low
no-load consumption. Additional requirements included latching
output overvoltage shutdown and compliance to safety agency
limited power source (LPS) limits. Actual efficiency and no-load
performance is summarized in the table shown in the schematic
which easily exceed current energy efficiency requirements.
In order to meet these design goals the following key design
decisions were made.
PI Part Selection
•
The device selected for this design was based on the 85-265 VAC,
Open Frame, PCB heatsinking column of power table (Table 1).
One device size smaller was selected (TOP266V vs. TOP267V)
due to the ambient specification of 40 °C (vs. the 50°C assumed
in the power table) and the optimum PCB area and layout for
Higher current rating, low V
for output rectifier.
Transistor Q1 and VR1 added to improve the output over-
voltage shutdown sensitivity.
Ambient of 40 °C allowed one device size smaller than
indicated by the power table.
BE
voltage drop Q1 turns on and current is fed into the
OR
= 110 V) which was in turn possible due to the high
F
Schottky rectifier diode selected
www.powerint.com
F
of 0.455 V
AN-47