RDK-252 Power Integrations, RDK-252 Datasheet - Page 23
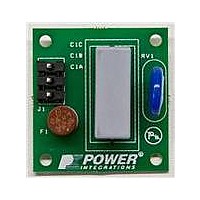
RDK-252
Manufacturer Part Number
RDK-252
Description
KIT REF DESIGN DG CAPZERO
Manufacturer
Power Integrations
Series
CAPZero™r
Type
Other Power Managementr
Specifications of RDK-252
Main Purpose
Automatic X Capacitor Discharge
Embedded
No
Utilized Ic / Part
CAP014DG, CAP002DG, CAP012DG
Primary Attributes
Low No-Load Input Power (
Secondary Attributes
Surge Testing to EN6100-4-5 Class 4
Input Voltage
85 V to 264 V
Board Size
38.1 mm x 25.4 mm
Product
Power Management Modules
Dimensions
38.1 mm x 25.4 mm
Lead Free Status / RoHS Status
Lead free / RoHS Compliant
For Use With/related Products
CAP014DG
Other names
596-1313
Available stocks
Company
Part Number
Manufacturer
Quantity
Price
Company:
Part Number:
RDK-252
Manufacturer:
Power Integrations
Quantity:
135
In some designs the Zener diode connected from the bias
winding may become a source of noise injected into the V pin.
This happens when the bias winding output ripple is high, or
the circuit board layout allows noise from adjacent circuits to be
coupled in the trace connecting the Zener diode to the V pin. In
such a situation, the solution shown in Figure 21 should be used.
Implementing Over-Power Protection (OPP)
Primary side sensed over-power protection can be implemented
via the V pin by sensing the voltage on the bias winding. Figure 22
shows this configuration. Zener diode VR
overvoltage protection and VR
overpower protection. This approach works well where the
desired OPP limit is >150% of the full load output power.
The OPP feature relies on the imperfect coupling between the
secondary and the bias winding. As the output load increases the
bias winding voltage rises due to the effect of leakage inductance.
If the bias voltage exceeds the voltage rating of VR
into the V pin causing the device to stop switching. The shutdown
can be made latching or non-latching through the value of R
5.1 kW results in non-latching while <22 W results in latching
shutdown. To prevent false triggering during transient loads and
startup R
constant of approximately 2 ms or longer than the duration of any
peak load conditions.
The voltage of VR
triggering of OVP during startup and load transients
Implementing an Accurate Over-Current protection (OCP)
The over-power protection (OPP) can also be used as a form of
(loose) over-current protection. However if an accurate over-
current protection (OCP) feature needs to be implemented, then
a separate optocoupler based circuit can be used to detect the
OCP threshold and turn off the switching device through the V pin.
Figure 30 shows an implementation of an accurate over-current
protection circuit. The load current is monitored by measuring
the voltage drop across a current sense resistor R
regulator IC U1 together with resistor divider network formed by
R2 and R3 is used to generate an accurate voltage reference of
0.03 V at the inverting input of op-amp U2. This low voltage
sense threshold allows for the use of small current sense resistors.
Resistor R6 and C1 provide frequency compensation. In this
example the value of R
threshold is set at 5 A. At this programmed current, the voltage
across R
the op-amp output to rise. This forward biases the diode in
optocoupler thereby triggering a shutdown through the V pin.
The value of R
5.1 kW results in non-latching while <22 W results in latching
shutdown. If the over-current limit specification is wide, then a
small signal diode may be used instead of U2 as a voltage
reference.
Designing High-Power Power Supplies
Using TOPSwitch-JX
At high power levels design of power supplies using a Flyback
topology requires additional considerations.
www.powerint.com
AN-47
P
SENSE
and C
exceeds the reference voltage (0.03 V) causing
OCP
P
OVP
provide a delay, with a recommended time
defines latching or non-latching shutdown,
should be higher than VR
SENSE
is chosen such that the over-current
OPP
together with R
OVP
provides the output
OPP
P
to prevent false
OPP
and C
SENSE
current flows
P
. Shunt
provides
OPP
,
1. Proximity losses in the transformer can be significant and
2. Slight increases in leakage inductance of the transformer
3. At high output currents the secondary ripple current increases
4. Minimize the length and loop area of PCB traces which
For high power designs using any TOPSwitch-JX and especially
for designs that use TOP269 – TOP271, it is recommended that
provision is made on the PCB board for a small RC (or RCD)
network positioned between the drain and source terminals
(Figure 29). This reduces switching noise from affecting power
supply operation and also helps in reducing radiated EMI. A
22 W to 150 W resistor and a 1 kV rated ceramic capacitor in the
range of 10 pF to 33 pF will be suitable for most applications.
The addition of the diode reduces power dissipation in the
snubber by up to a factor of 2.
Quick Design Checklist
As with any power supply, all TOPSwitch-JX designs should be
verified with actual hardware to ensure that component
specifications are not exceeded under worst-case conditions.
The following minimum set of tests is strongly recommended:
1. Maximum drain voltage – verify that peak V
2. Maximum drain current – at maximum ambient temperature,
makes design of flyback transformers at high power levels
very sensitive to the construction method with respect to
winding configuration and the choice of the number of strands
in multi wire configuration. The choice of wire size in a high
frequency transformer is dependent on switching frequency.
Skin depth is proportional to switching frequency and limits
the usable cross sectional area of each conductor. Multi-strand
(filar) windings and litz wires are commonly used to reduce
conduction losses in high frequency transformers. To further
reduce skin effects, the use of foil windings is recommended
especially for low voltage high current (>6 A) outputs.
and PCB traces can lead to a large increase in dissipation in
the snubber circuit. To reduce leakage inductance it is
important to use sandwich winding construction in the
transformer and minimize PCB trace lengths, especially the
loop formed by the secondary winding, output diode and
output capacitors. Design of the snubber circuit is critical in
achieving high efficiency; typically at high power levels a
correctly sized RCDZ clamp will ensure that the drain source
voltage does not exceed 680 V.
and may be above the rating of a single very low ESR output
capacitor. It is therefore common to use multiple capacitors
in parallel. In this case special attention must be paid to
equalize the trace length to all capacitors to give even
distribution of the ripple current. This ensures equal dissipation
and temperature rise, critical to ensure an acceptable
operating life. Even with multiple capacitors a second stage
LC filter is required to reduce switching frequency ripple.
carry large switching currents and voltages as these can be
a source of radiated EMI.
exceed 680 V at highest input voltage and maximum
overload output power. Maximum overload output power
occurs when the output is overloaded to a level just before
the power supply goes into auto-restart (loss of regulation).
maximum input voltage and maximum output load, verify
Application Note
DS
does not
Rev. A 030910
23