AFS600-FGG256 Actel, AFS600-FGG256 Datasheet - Page 160
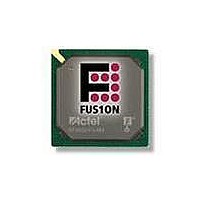
AFS600-FGG256
Manufacturer Part Number
AFS600-FGG256
Description
FPGA - Field Programmable Gate Array 600K System Gates
Manufacturer
Actel
Datasheet
1.AFS600-PQG208.pdf
(330 pages)
Specifications of AFS600-FGG256
Processor Series
AFS600
Core
IP Core
Maximum Operating Frequency
1098.9 MHz
Number Of Programmable I/os
119
Data Ram Size
110592
Supply Voltage (max)
1.575 V
Maximum Operating Temperature
+ 70 C
Minimum Operating Temperature
0 C
Development Tools By Supplier
AFS-Eval-Kit, AFS-BRD600, FlashPro 3, FlashPro Lite, Silicon-Explorer II, Silicon-Sculptor 3, SI-EX-TCA
Mounting Style
SMD/SMT
Supply Voltage (min)
1.425 V
Number Of Gates
600 K
Package / Case
FPBGA-256
Lead Free Status / RoHS Status
Lead free / RoHS Compliant
Available stocks
Company
Part Number
Manufacturer
Quantity
Price
Company:
Part Number:
AFS600-FGG256
Manufacturer:
Actel
Quantity:
135
Part Number:
AFS600-FGG256
Manufacturer:
ACTEL/爱特
Quantity:
20 000
Company:
Part Number:
AFS600-FGG256I
Manufacturer:
Microsemi SoC
Quantity:
10 000
Company:
Part Number:
AFS600-FGG256K
Manufacturer:
Microsemi SoC
Quantity:
10 000
- Current page: 160 of 330
- Download datasheet (13Mb)
Device Architecture
2- 14 4
For Fusion devices requiring Level 3 and/or Level 4 compliance, the board drivers connected to Fusion
I/Os need to have 10 kΩ (or lower) output drive resistance at hot insertion, and 1 kΩ (or lower) output
drive resistance at hot removal. This is the resistance of the transmitter sending a signal to the Fusion
I/O, and no additional resistance is needed on the board. If that cannot be assured, three levels of
staging can be used to meet Level 3 and/or Level 4 compliance. Cards with two levels of staging should
have the following sequence:
Cold-Sparing Support
Cold-sparing means that a subsystem with no power applied (usually a circuit board) is electrically
connected to the system that is in operation. This means that all input buffers of the subsystem must
present very high input impedance with no power applied so as not to disturb the operating portion of the
system.
Pro I/O banks and standard I/O banks fully support cold-sparing.
For Pro I/O banks, standards such as PCI that require I/O clamp diodes, can also achieve cold-sparing
compliance, since clamp diodes get disconnected internally when the supplies are at 0 V.
For Advanced I/O banks, since the I/O clamp diode is always active, cold-sparing can be accomplished
either by employing a bus switch to isolate the device I/Os from the rest of the system or by driving each
advanced I/O pin to 0 V.
If Standard I/O banks are used in applications requiring cold-sparing, a discharge path from the power
supply to ground should be provided. This can be done with a discharge resistor or a switched resistor.
This is necessary because the standard I/O buffers do not have built-in I/O clamp diodes.
If a resistor is chosen, the resistor value must be calculated based on decoupling capacitance on a given
power supply on the board (this decoupling capacitor is in parallel with the resistor). The RC time
constant should ensure full discharge of supplies before cold-sparing functionality is required. The
resistor is necessary to ensure that the power pins are discharged to ground every time there is an
interruption of power to the device.
I/O cold-sparing may add additional current if the pin is configured with either a pull-up or pull down
resistor and driven in the opposite direction. A small static current is induced on each IO pin when the pin
is driven to a voltage opposite to the weak pull resistor. The current is equal to the voltage drop across
the input pin divided by the pull resistor. Please refer to
page
standard.
For example, assuming an LVTTL 3.3 V input pin is configured with a weak Pull-up resistor, a current will
flow through the pull-up resistor if the input pin is driven low. For an LVTTL 3.3 V, pull-up resistor is ~45
kΩ and the resulting current is equal to 3.3 V / 45 kΩ = 73 µA for the I/O pin. This is true also when a
weak pull-down is chosen and the input pin is driven high. Avoiding this current can be done by driving
the input low when a weak pull-down resistor is used, and driving it high when a weak pull-up resistor is
used.
In Active and Static modes, this current draw can occur in the following cases:
1. Grounds
2. Powers, I/Os, other pins
•
•
•
•
•
•
•
•
2-171, and
Input buffers with pull-up, driven low
Input buffers with pull-down, driven high
Bidirectional buffers with pull-up, driven low
Bidirectional buffers with pull-down, driven high
Output buffers with pull-up, driven low
Output buffers with pull-down, driven high
Tristate buffers with pull-up, driven low
Tristate buffers with pull-down, driven high
Table 2-94 on page 2-173
for the specific pull resistor value for the corresponding I/O
R e visio n 1
Table 2-92 on page
2-171,
Table 2-93 on
Related parts for AFS600-FGG256
Image
Part Number
Description
Manufacturer
Datasheet
Request
R

Part Number:
Description:
AFS600-1FGG256I
Manufacturer:
Actel
Datasheet:

Part Number:
Description:
AFS600-2FGG256I
Manufacturer:
Actel
Datasheet: