mc68hc908mr24 Freescale Semiconductor, Inc, mc68hc908mr24 Datasheet - Page 157
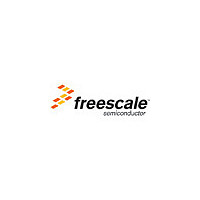
mc68hc908mr24
Manufacturer Part Number
mc68hc908mr24
Description
M68hc08 Microcontrollers
Manufacturer
Freescale Semiconductor, Inc
Datasheet
1.MC68HC908MR24.pdf
(406 pages)
- Current page: 157 of 406
- Download datasheet (3Mb)
MC68HC908MR24 — Rev. 4.1
Freescale Semiconductor
To allow for correction based on different current sensing methods or
correction controlled by software, the ISENS1 and ISENS0 bits in PWM
control register 1 are provided to choose the correction method. These
bits provide correction according to
If correction is to be done in software or is not necessary, setting
ISENS1:ISENS0 = 00 or = 01 causes the correction to be based on bits
IPOL1, IPOL2, and IPOL3 in PWM control register 2. If correction is not
required, the user can initialize the IPOLx bits and then only load one
PWM value register per PWM pair.
To allow the user to use a current sense scheme based upon sensed
phase voltage during dead time, setting ISENS1:ISENS0 = 10 causes
the polarity of the Ix pin to be latched when both the top and bottom
PWMs are off (for example, during the dead time). At the 0 percent and
100 percent duty cycle boundaries, there is no dead time so no new
current value is sensed.
To accommodate other current sensing schemes, setting
ISENS1:ISENS0 = 11 causes the polarity of the current sense pin to be
latched half-way into the PWM cycle in center-aligned mode and at the
end of the cycle in edge-aligned mode. Therefore, even at 0 percent and
100 percent duty cycle, the current is sensed.
Pulse-Width Modulator for Motor Control (PWMMC)
Current Correction Bits
ISENS1 and ISENS0
00
01
10
11
Table 9-5. Correction Methods
Bits IPOL1, IPOL2, and IPOL3 used for correction
Current sensing on pins IS1, IS2, and IS3 occurs
Current sensing on pins IS1, IS2, and IS3 occurs at
during the dead time.
the half cycle in center-aligned mode and at the
end of the cycle in edge-aligned mode.
Pulse-Width Modulator for Motor Control (PWMMC)
Table
Correction Method
9-5.
Advance Information
157
Related parts for mc68hc908mr24
Image
Part Number
Description
Manufacturer
Datasheet
Request
R

Part Number:
Description:
Manufacturer:
Freescale Semiconductor, Inc
Datasheet:

Part Number:
Description:
Manufacturer:
Freescale Semiconductor, Inc
Datasheet:

Part Number:
Description:
Manufacturer:
Freescale Semiconductor, Inc
Datasheet:

Part Number:
Description:
Manufacturer:
Freescale Semiconductor, Inc
Datasheet:

Part Number:
Description:
Manufacturer:
Freescale Semiconductor, Inc
Datasheet:

Part Number:
Description:
Manufacturer:
Freescale Semiconductor, Inc
Datasheet:

Part Number:
Description:
Manufacturer:
Freescale Semiconductor, Inc
Datasheet:

Part Number:
Description:
Manufacturer:
Freescale Semiconductor, Inc
Datasheet:

Part Number:
Description:
Manufacturer:
Freescale Semiconductor, Inc
Datasheet:

Part Number:
Description:
Manufacturer:
Freescale Semiconductor, Inc
Datasheet:

Part Number:
Description:
Manufacturer:
Freescale Semiconductor, Inc
Datasheet:

Part Number:
Description:
Manufacturer:
Freescale Semiconductor, Inc
Datasheet:

Part Number:
Description:
Manufacturer:
Freescale Semiconductor, Inc
Datasheet:

Part Number:
Description:
Manufacturer:
Freescale Semiconductor, Inc
Datasheet:

Part Number:
Description:
Manufacturer:
Freescale Semiconductor, Inc
Datasheet: