CV500BSC51 Omron, CV500BSC51 Datasheet
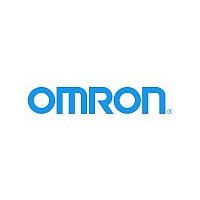
CV500BSC51
Specifications of CV500BSC51
Related parts for CV500BSC51
CV500BSC51 Summary of contents
Page 1
Cat. No. W410-E1-01 SYSMAC CS1W-GPI01 GP-IB Interface Unit OPERATION MANUAL ...
Page 2
Operation Manual Produced September 2002 ...
Page 3
iv ...
Page 4
... OMRON. No patent liability is assumed with respect to the use of the information contained herein. Moreover, because OMRON is con- stantly striving to improve its high-quality products, the information contained in this manual is subject to change without notice ...
Page 5
vi ...
Page 6
... Features . . . . . . . . . . . . . . . . . . . . . . . . . . . . . . . . . . . . . . . . . . . . . . . . . . . . . . . . . . . . . . . . . 1-2 Specifications and Device Configuration . . . . . . . . . . . . . . . . . . . . . . . . . . . . . . . . . . . . . . . 1-3 Description of the GP-IB System . . . . . . . . . . . . . . . . . . . . . . . . . . . . . . . . . . . . . . . . . . . . . 1-4 Comparison with other OMRON Units’ GP-IB Functions . . . . . . . . . . . . . . . . . . . . . . . . . . SECTION 2 Preparations . . . . . . . . . . . . . . . . . . . . . . . . . . . . . . . . . . . . . . SECTION 3 Installation and Wiring . . . . . . . . . . . . . . . . . . . . . . . . . . . . . 3-1 Component Names and Functions . . . . . . . . . . . . . . . . . . . . . . . . . . . . . . . . . . . . . . . . . . . . . ...
Page 7
SECTION 6 Programming Examples 6-1 Master Mode Program Examples . . . ...
Page 8
About this Manual: This manual describes the installation and operation of the GP-IB Interface Unit and includes the sec- tions described below. Please read this manual carefully along with any related manuals (see table below) and be sure you understand ...
Page 9
x ...
Page 10
This section provides general precautions for using the GP-IB Interface Unit, Programmable Controller, and related devices. The information contained in this section is important for the safe and reliable application of the GP-IB Interface Unit. You must read this section ...
Page 11
... It is extremely important that a PLC and all PLC Units be used for the speci- fied purpose and under the specified conditions, especially in applications that can directly or indirectly affect human life. You must consult with your OMRON representative before applying a PLC system to the above mentioned applica- tions ...
Page 12
Safety Precautions 3 Safety Precautions !WARNING !WARNING !WARNING !Caution Execute online edit only after confirming that no adverse effects will be !Caution Confirm safety at the destination node before transferring a program to Never attempt to disassemble any Units while ...
Page 13
Operating Environment Precautions 4 Operating Environment Precautions !Caution Take appropriate and sufficient countermeasures when installing systems in !Caution The operating environment of the PLC System can have a large effect on the xiv Do not operate the control system in ...
Page 14
Application Precautions 5 Application Precautions !WARNING !Caution Failure to abide by the following precautions could lead to faulty operation of Observe the following precautions when using the GP-IB Interface Unit or the PLC. Failure to abide by the following precautions ...
Page 15
Application Precautions xvi • Check the user program for proper execution before actually running it on the Unit. Not checking the program may result in an unexpected opera- tion. • Confirm that no adverse effect will occur in the system ...
Page 16
... EMC Directives EMC Directives OMRON devices that comply with EC Directives also conform to the related EMC standards so that they can be more easily built into other devices or the overall machine. The actual products have been checked for conformity to EMC standards (see the following note). Whether the products conform to the standards in the system used by the customer, however, must be checked by the customer ...
Page 17
EC Directives 6-4 EMC Countermeasures Recommended Ferrite Core Recommended Mounting Method xviii The CS1W-GPI01 GP-IB Interface Unit test conditions are as follows: • Ferrite cores were attached to the GP-IB cables. Ferrite Core (data line noise filter): 0443-164151 manufactured by ...
Page 18
... Description of the GP-IB System . . . . . . . . . . . . . . . . . . . . . . . . . . . . . . . . . . 1-3-1 GP-IB System Configuration . . . . . . . . . . . . . . . . . . . . . . . . . . . . . . 1-3-2 GP-IB Bus Line Specifications 1-3-3 GP-IB Device Functions 1-4 Comparison with other OMRON Units’ GP-IB Functions 1-4-1 Functional Comparison 1-4-2 Differences in the Units’ Interface Functions Features and System Configuration SECTION 1 2 ...
Page 19
Features 1-1 Features Conforms to the IEEE-488-1978 Standards Control GB-IP Communications from the Ladder Program Master and Slave Modes Master Mode Slave Mode 2 The CS1W-GPI01 GP-IB Interface Unit connects GP-IB devices to a CS- series PLC to provide communications ...
Page 20
Specifications and Device Configuration 1-2 Specifications and Device Configuration 1-2-1 General Specifications ory. If the Data Read Completed Flag has been turned ON, transfer the data from the connected device to the CS-series CPU Unit by executing IORD(222) to read ...
Page 21
Specifications and Device Configuration 1-2-2 Functional Specifications Item Name Model number Compatible PLCs Unit type Mounting location Max. number of GP-IB Interface Units Unit number setting range GP-IB Interface Unit settings when editing the I/O tables offline with the CX-Programmer ...
Page 22
Description of the GP-IB System 1-2-3 System Configuration Note There are three kinds of devices that can be connected in a GP-IB system: 1-2-4 GP-IB Cables 1-3 Description of the GP-IB System 1-3-1 GP-IB System Configuration The CS1W-GPI01 GP-IB Interface ...
Page 23
Description of the GP-IB System System Restrictions GP-IB System Functions Controller Talkers Listeners 1-3-2 GP-IB Bus Line Specifications 6 • There must be no more than 15 interfaces (devices) connected in one system. • The total length of communications cable ...
Page 24
Description of the GP-IB System Signal Line Configuration Lines Data lines DIO1 (Data Input/Output 1) DIO2 (Data Input/Output 2) DIO3 (Data Input/Output 3) DIO4 (Data Input/Output 4) DIO5 (Data Input/Output 5) DIO6 (Data Input/Output 6) DIO7 (Data Input/Output 7) DIO8 ...
Page 25
Description of the GP-IB System Interface Messages Note Transferring Commands and Data 8 Interface messages control the GP-IB devices’ interface functions and device functions. The following table lists the messages that can control the GP-IB Interface Unit. Interface message Device ...
Page 26
... Comparison with other OMRON Units’ GP-IB Functions 1,2,3... Note The GP-IB Interface Unit automatically controls the ATN line status to switch Service Request and Serial Poll 1-4 Comparison with other OMRON Units’ GP-IB Functions 1-4-1 Functional Comparison Model Compatible PLCs CS-series ...
Page 27
... Comparison with other OMRON Units’ GP-IB Functions 1-4-2 Differences in the Units’ Interface Functions Interface function SH SH1 AH AH1 T T8/ SR1 RL RL0 PP PP0 DC DC1 DT DT0 C C1, C2, C3, C4, and C28 10 CS1W-GPI01 C500-GPI01 T6 C0 Section 1-4 CV500-BSC51/61 T8/T6 RL1 PP1 C1, C2, C3, C4, and C26 ...
Page 28
This section explains the main steps required to prepare for operation. SECTION 2 Preparations 11 ...
Page 29
Preparations Step Operation 1 Mount Unit in the PLC. 2 Wire the cables. 3 Set the unit number. 4 Turn ON the PLC. 5 Create I/O tables. 6 Make required settings in allocated DM area words. 7 Turn the PLC ...
Page 30
This section explains the steps required for installation and wiring. 3-1 Component Names and Functions . . . . . . . . . . . . . . . . . . . . . . . . . ...
Page 31
Component Names and Functions 3-1 Component Names and Functions 3-1-1 Unit Appearance 3-1-2 Dimensions (Unit: mm) Dimensions without a Cable Connected 14 LED Indicators Indicate the Unit’s status. Unit Number Setting Switches These two rotary switches set the Unit’s unit ...
Page 32
Component Names and Functions Dimensions with Two Cables Connected 3-1-3 Indicators 55 (With two connectors) 31 (With one connector) GPI01 CS RUN ERC ERH TALK LSTN SRQ Indicator Color Name RUN Green Unit Operating ERC Red GPIB Communica- tions Error ...
Page 33
Mounting the Unit in the PLC 3-2 Mounting the Unit in the PLC Note Note If the GP-IB Interface Unit is mounted in a CS-series Expansion Backplane, 3-3 Wiring the Cables 3-3-1 Daisy-chain Configuration 16 The GP-IB Interface Unit must ...
Page 34
Wiring the Cables 3-3-2 Star Configuration Note Up to two GP-IB Cable Connectors can be connected at the GP-IB Interface 3-3-3 Recommended Cables 3-3-4 Connecting the Cables 1,2,3... Note Device Device Device It is also possible to combine daisy-chain and ...
Page 35
Setting the Unit Number 3-4 Setting the Unit Number Note 18 8. Ground the Power Supply Unit to a resistance of 100 Rack or Expansion Rack where the GP-IB Interface Unit is mounted. The GP-IB connector’s shell is internally connected ...
Page 36
This section explains the functions of the GP-IB Interface Unit’s buffer memory and the words allocated in the DM area and CIO area. 4-1 DM Area Allocations . . . . . . . . . . . . . ...
Page 37
DM Area Allocations 4-1 DM Area Allocations 4-1-1 Allocation of DM Area Words Allocation of DM Area Words to Special I/O Units 4-1-2 DM Area Allocation Details m = D20000 + (100 unit number) Word Bits ...
Page 38
DM Area Allocations Word Bits m Transmission delimiter specification EOI specification Transmission delimiter selection m Reception delimiter specification EOI specification Reception delimiter ...
Page 39
DM Area Allocations Data Storage Order (Bits m+1) Byte Order when Sending Byte Order when Receiving Enhanced BASIC Commands Setting (Bits m+1) Timeout Monitor Time (m+2) Transmission Delimiter Specification (m+3) 22 Specifies ...
Page 40
CIO Area Allocations Reception Delimiter Specification (m+4) Number of Bytes to Receive (m+5) Note The GP-IB Interface Unit will complete reception when any of the following SRQ External Interrupt Task Settings (m+6) Note 4-2 CIO Area Allocations 4-2-1 Allocation of ...
Page 41
CIO Area Allocations Allocation of CIO Area Words to Special I/O Units CIO Area Allocation Details (Output) 24 Unit number Allocated words #0 CIO 2000 to CIO 2009 #1 CIO 2010 to CIO 2019 #2 CIO 2020 to CIO 2029 ...
Page 42
CIO Area Allocations Note CIO Area Allocation Details (Input) 1. The Send Interface Message Request Bit, Send Data Request Bit, Read Data Request Bit, and SRQ Request Bit are effective when the bit goes from OFF to ON. 2. The ...
Page 43
CIO Area Allocations 26 Word Bits Name n Reserved --- 06 ID0/OD0 Com ID0 or OD0 command was not received. mand Received Flag 1: An ID0 or OD0 command was received. 07 Parameter Error 0: ...
Page 44
Buffer Memory 4-3 Buffer Memory 4-3-1 Buffer Memory Details Category Address Functions 0000 Interface message number related to interface mes- sages 0001 Number of peer devices 0002 to Peer device addresses 000F 0010 to Serial polling status 001D 001E to ...
Page 45
Using IORD(222) and IOWR(223) Note 4-4 Using IORD(222) and IOWR(223) 4-4-1 INTELLIGENT I/O READ: IORD(222) Note Bit used as the Read Continuation Bit. When more than 128 words 4-4-2 INTELLIGENT I/O WRITE: IOWR(223) Note Refer to ...
Page 46
Using IORD(222) and IOWR(223) 4-4-3 Reading more than 128 Words Read Continuation Flag Note Bit functions as the Read Continuation Bit. The Data Read Completed Flag in the allocated CIO area words will be turned OFF when ...
Page 47
Using IORD(222) and IOWR(223) Note 30 First IORD(222) Starting read address: 8154 Hex Number of words to receive: 128 IORD(222) Buffer memory Turned ON by Unit. Data Read Completed Flag The Read Continuation Bit is ON, so the Data Read ...
Page 48
This section explains the GP-IB Interface Unit’s communications functions. 5-1 Master Mode Functions . . . . . . . . . . . . . . . . . . . . . . . . . . . ...
Page 49
Master Mode Functions 5-1 Master Mode Functions 5-1-1 Sending Interface Messages 1,2,3... 5-1-2 Sending Data in Master Mode 1,2,3... 32 Send interface messages to control other devices in the GP-IB system. Use the following procedure to send interface messages. 1. ...
Page 50
Master Mode Functions 2. Write the following 4 settings into buffer memory from the ladder program the Data Send Completed Flag (bit 01 of n+5 in the allocated CIO area 4. When the data has been sent, the ...
Page 51
Master Mode Functions 5-1-3 Receiving Data in Master Mode 1,2,3... 34 Controller (Master mode) GP-IB Interface CPU Unit Unit 1. Use IOWR(223) to write the transmission data and parameters. 2. Turn ON the Send Data Request Bit. 4. The Data ...
Page 52
Master Mode Functions Note 1. The individual reception parameters (reception delimiter specification, tim- 2. When the same settings are being used for all sending and receiving de- 3. The “number of bytes to receive” setting does not include the reception ...
Page 53
Slave Mode Functions 5-1-4 Receiving SRQ Messages in Master Mode Note 5-2 Slave Mode Functions 5-2-1 Sending Data in Slave Mode 1,2,3... SRQ message is received from another device while the GP-IB Interface Unit is operating in ...
Page 54
Slave Mode Functions 3. If the Data Send Completed Flag (bit 01 of n+5 in the allocated CIO area 4. When the data has been sent, the TALK Indicator will go OFF and the Data Use the INTELLIGENT I/O READ ...
Page 55
Slave Mode Functions 5-2-2 Receiving Data in Slave Mode 1,2,3... 38 Slave mode GP-IB CPU Unit Interface Unit 2. Talker Specification Received Flag goes ON. 3. Write transmission data with IOWR(223). 4. Turn ON the Send Data Request Bit. 6. ...
Page 56
Slave Mode Functions Note 1. The individual reception parameters (reception delimiter specification, tim- 2. When the same settings are being used for all sending and receiving de- 3. The “number of bytes to receive” setting does not include the reception ...
Page 57
Slave Mode Functions 5-2-3 Sending SRQ Messages in Slave Mode (Interrupt Request) Note When serial polling is performed because an SRQ message has been sent to 5-2-4 Executing Enhanced BASIC Commands Note 40 When the GP-IB Interface Unit is operating ...
Page 58
Slave Mode Functions Executable Enhanced BASIC Commands OS (Output Status) IN (Initialize) ID0 (Input Data: ASCII) ID1 (Input Data: Binary) OD0 (Output Data: ASCII) OD1 (Output Data: Binary) Command Name OS Output Status Sends the Unit’s internal status to the ...
Page 59
Slave Mode Functions 42 Section 5-2 ...
Page 60
This section provides programming examples that demonstrate how to control the GP-IB system and transfer data from the ladder program. 6-1 Master Mode Program Examples . . . . . . . . . . . . . . . ...
Page 61
Master Mode Program Examples 6-1 Master Mode Program Examples Note When the sample programs are used as-is, verify that the bits and words used 6-1-1 Device Trigger 44 The programming examples in this section use the following system configu- ration. ...
Page 62
Master Mode Program Examples Program Example The GET message is sent when W000.00 is turned ON. A200.11 First Cycle Flag A200.11 First Cycle Flag W000.00 W100.00 W100.01 W100.01 W100.01 IOWR(223) Equal Flag (CF006) W100.00 W100.00 2005.00 2000.00 2005.00 2007.07 Section ...
Page 63
Master Mode Program Examples 6-1-2 Set Remote Status Program Example 46 This program sets a device to remote status. The REN message can be used to set a single device to remote status or set two or more devices simulta- ...
Page 64
Master Mode Program Examples 6-1-3 Device Clear Program Example This program initializes a device in the system. A DCL message is sent if there is no address specification. An SDC message is sent if there is an address specification. In ...
Page 65
Master Mode Program Examples 6-1-4 Set Local Status Program Example 48 This program sets a device to local status. The control line REN is set to high if there is no address specification. A GTL message is sent if there ...
Page 66
Master Mode Program Examples 6-1-5 Set Local Lockout Program Example This program sends an LLO message and prohibits operations from the desti- nation device’s front panel. The LLO message is sent when W000.00 is turned ON. A200.11 First Cycle Flag ...
Page 67
Master Mode Program Examples 6-1-6 Serial Poll Program Example 50 This program reads the status of a GP-IB device. The SRQ Received Flag (CIO 2007.12) is turned ON to perform serial polling. A200.11 First Cycle Flag A200.11 First Cycle Flag ...
Page 68
Master Mode Program Examples Continued 2007.12 W100.00 W100.01 W100.01 W100.01 IOWR(223) #0000 D00010 D17000 Equal Flag (CF006) W100.00 W100.00 2005.00 2000.00 2000.00 2005.00 IORD(222) #0010 D17002 Equal Flag W300 (CF006) RSET 2000.00 2007.07 W200.00 END(001) Section 6-1 IOWR(223) writes the ...
Page 69
Master Mode Program Examples 6-1-7 Interface Clear Program Example 52 This program initializes the interface functions. Sets control line IFC to “L” for approximately 100 s. The IFC message is sent when W000.00 is turned ON. A200.11 First Cycle Flag ...
Page 70
Master Mode Program Examples 6-1-8 Sending Data Program Example This program sends data to a device. Data is transmitted when W000.00 is turned ON. In this example, 50 words of transmission data are stored in the DM area starting at ...
Page 71
Master Mode Program Examples 54 Continued W000.00 W100.00 W100.01 W100.01 W000.00 W100.02 W100.03 W100.03 W100.01 IOWR(223) #0022 D00010 D17000 Equal Flag (CF006) W100.00 W100.03 IOWR(223) #0031 D00012 D17002 Equal Flag (CF006) W100.02 W100.00 W100.02 2005.01 SET 2000.01 2000.01 2005.01 RSET ...
Page 72
Master Mode Program Examples 6-1-9 Receiving Data Program Example This program receives data from a device. Data is transferred when W000.00 is turned ON and the received data is stored in the DM area starting at D02000. The reception delimiter ...
Page 73
Slave Mode Program Examples Note The sample program above always reads 10 words (20 bytes) of data. The 6-2 Slave Mode Program Examples Note When the sample programs are used as-is, verify that the bits and words used 56 Continued ...
Page 74
Slave Mode Program Examples 6-2-1 Sending Data Program Example This program sends data to another device. If the GP-IB Interface Unit is operating as a Slave, it sends data when a send request has been received from the system Controller, ...
Page 75
Slave Mode Program Examples 6-2-2 Receiving Data Program Example 58 Continued W100.00 2005.01 2000.01 2005.01 2007.07 2007.08 2007.09 This program receives data from another device. If the GP-IB Interface Unit is operating as a Slave, it receives data automati- cally. ...
Page 76
Enhanced BASIC Command Program Example Note The sample program above always reads 10 words (20 bytes) of data. The 6-2-3 Service Request Program Example 6-3 Enhanced BASIC Command Program Example OS (Output Status) BASIC Programming Example IN (Initialize) BASIC Programming ...
Page 77
Enhanced BASIC Command Program Example ID0 (Input Data: ASCII) BASIC Programming Example ID1 (Input Data: Binary) BASIC Programming Example OD0 (Output Data: ASCII) BASIC Programming Example OD1 (Output Data: Binary) BASIC Programming Example 60 When an ID0 command is received ...
Page 78
This section provides tables to help troubleshoot and correct errors that may occur when operating the GP-IB Interface Unit. 7-1 Using LED Indicators for Error Processing . . . . . . . . . . . . . . ...
Page 79
Using LED Indicators for Error Processing 7-1 Using LED Indicators for Error Processing Indicator status Error Flag in Status Byte RUN ERC ERH (See note 1.) Not lit Not lit Not lit --- Not lit Not lit Lit --- Not ...
Page 80
Using the Status Byte for Error Processing shows the errors indicated in the status area as well as the steps most likely to correct the errors. Error Flags in n CIO 2000 + (10 Error Flag Probable cause ...
Page 81
Using the Status Byte for Error Processing Error Flag Probable cause Timeout error A non-existent device address was specified in buffer memory for the “transmitting device address” (Bit 9 of n+7 or “receiving device address.” ON) The timeout monitor time ...
Page 82
Other Communications Problems 7-3 Other Communications Problems Problem The byte order is reversed in --- the received data. Only part of the expected data The GP-IB Interface Unit is the receiving can be received. device and allocated CIO word n+6 ...
Page 83
Other Communications Problems Problem The GP-IB Interface Unit is --- operating in Master mode (as the Controller) and it is set to trigger an interrupt program, but the interrupt program in the PLC does not start when an SRQ message ...
Page 84
System Configuration GP-IB device address 1 This program reads the DC voltage data measured by an Advantest Digital Multimeter. The data received from the Multimeter is stored in DM addresses D00000 to D00006. The GP-IB Interface Unit operates as the ...
Page 85
Sample Program Program Command Control A200.11 MOV(021) First Cycle Flag #0001 W511 W511.00 W100.00 W511.01 W200.00 W511.02 W300.00 W511.03 W400.00 Interface Clear A200.11 MOV(021) First Cycle Flag #0007 W110 A200.11 MOV(021) First Cycle #0000 Flag W010 MOV(021) #0001 W011 W100.00 ...
Page 86
Sample Program Continued W100.00 W101.01 Equal Flag (CF006) W100.00 W101.00 2005.00 W100.00 2000.00 2005.00 W100.00 2007.07 2007.08 2007.09 Set Remote Status A200.11 First Cycle Flag Continued IOWR(223) #0000 IOWR(223) writes the interface message number (0007 Hex) beginning at buffer memory ...
Page 87
Sample Program Continued A200.11 First Cycle Flag W200.00 W201.00 W201.01 W200.00 W201.01 Equal Flag (CF006) W200.00 W201.00 2005.00 W200.00 2000.00 2005.00 W200.00 2007.07 2007.08 2007.09 Continued 70 MOV(021) #0000 W020 Sets the parameters for IOWR(223). Unit number of destination device: ...
Page 88
Sample Program Continued Device Clear A200.11 First Cycle Flag A200.11 First Cycle Flag W300.00 W301.00 W301.01 W300.00 W301.01 Equal Flag (CF006) W300.00 W301.00 2005.00 Continued MOV(021) #0003 W310 Stores the data that will be written in buffer memory. MOV(021) Interface ...
Page 89
Sample Program Continued W300.00 2000.00 2005.00 W300.00 2007.07 2007.08 2007.09 Receiving Data from the Digital Multimeter A200.11 First Cycle Flag A200.11 First Cycle Flag Continued 72 RSET Turns OFF the Send Interface Message Request Bit if the message was sent ...
Page 90
Sample Program Continued W400.00 W401.00 W401.01 W400.00 W401.01 Equal Flag (CF006) W400.00 W401.00 2005.02 W400.00 2000.02 2005.02 Equal Flag (CF006) W400.00 2007.07 2007.08 2007.09 W401.01 IOWR(223) IOWR(223) writes the transmitting device address, number of receiving #0143 device addresses, and receiving ...
Page 91
Sample Program 74 Appendix A ...
Page 92
GP-IB Cables (Recommended Cables) Appendix B List of Accessories Name Model GP-IB Harness 408JE-10P5 408JE-101 408JE-102 408JE-104 Length Manufacturer 0.5 m DDK Electronics, Inc ...
Page 93
List of Accessories 76 Appendix B ...
Page 94
A address , device address 7 , primary address 7 Advantest Digital Multimeter , sample program 67 B BASIC commands , executing 40 , program example 59 , setting in DM Area 22 , buffer memory 27 , reading data ...
Page 95
F , features 1 flags , CIO Area flags 25 , error flags general specifications 3 GET message , program example 44 , GP-IB Error Flag GP-IB Harness GP-IB Interface Unit , installation 16 ...
Page 96
Slave mode 2 , mounting the Unit 16 N number of bytes to receive , setting in DM area 23 , Number of data bytes received 25 number of peer devices , setting in buffer memory 27 O OD0 ...
Page 97
DM Area 21 specifications , functional 4 , general specifications 3 SRQ external interrupt , settings in DM area 23 SRQ indicator , function 15 SRQ messages , receiving ...
Page 98
A manual revision code appears as a suffix to the catalog number on the front cover of the manual. The following table outlines the changes made to the manual during each revision. Page numbers refer to the previous version. Revision ...
Page 99
Revision History ...
Page 100
... Cancellation; Etc. Orders are not subject to rescheduling or cancellation unless Buyer indemnifies Omron against all related costs or expenses. 10. Force Majeure. Omron shall not be liable for any delay or failure in delivery resulting from causes beyond its control, including earthquakes, fires, floods, strikes or other labor disputes, shortage of labor or materials, accidents to machinery, acts of sabotage, riots, delay in or lack of transportation or the requirements of any government authority ...
Page 101
... For US technical support or other inquiries: 800.556.6766 OMRON CANADA, INC. 885 Milner Avenue 1 5 Toronto, Ontario 416.286.6465 OMRON ON-LINE Global - http://www.omron.com USA - http://www.omron.com/oei Canada - http://www.omron.ca W410-E1-01 6/06 ©2006 OMRON ELECTRONICS LLC 8 Printed in the U.S.A. Specifications subject to change without notice. ...