ADC08D1500DEV/NOPB National Semiconductor, ADC08D1500DEV/NOPB Datasheet - Page 35
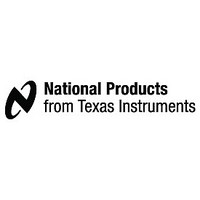
ADC08D1500DEV/NOPB
Manufacturer Part Number
ADC08D1500DEV/NOPB
Description
BOARD DEV FOR ADC08D1500
Manufacturer
National Semiconductor
Series
PowerWise®r
Specifications of ADC08D1500DEV/NOPB
Mfg Application Notes
Clocking High-Speed A/D Converters AppNote
Number Of Adc's
2
Number Of Bits
8
Sampling Rate (per Second)
1.5G
Data Interface
Serial
Inputs Per Adc
1 Differential
Input Range
870 mVpp
Power (typ) @ Conditions
1.8W @ 1.5GSPS
Voltage Supply Source
Single Supply
Operating Temperature
-40°C ~ 85°C
Utilized Ic / Part
ADC08D1500
Lead Free Status / RoHS Status
Lead free / RoHS Compliant
Other names
ADC08D1500DEV
Available stocks
Company
Part Number
Manufacturer
Quantity
Price
Company:
Part Number:
ADC08D1500DEV/NOPB
Manufacturer:
ELNA
Quantity:
30 000
If the power is applied to the device without an input clock
signal present, the current drawn by the device might be be-
low 200 mA. This is because the ADC08D1500 gets reset
through clocked logic and its initial state is unknown. If the
reset logic comes up in the "on" state, it will cause most of the
analog circuitry to be powered down, resulting in less than
100 mA of current draw. This current is greater than the power
down current because not all of the ADC is powered down.
The device current will be normal after the input clock is es-
tablished.
2.6.2 Thermal Management
The ADC08D1500 is capable of impressive speeds and per-
formance at very low power levels for its speed. However, the
power consumption is still high enough to require attention to
thermal management. For reliability reasons, the die temper-
ature should be kept to a maximum of 130°C. That is, T
(ambient temperature) plus ADC power consumption times
θ
ceed 130°C. This is not a problem if the ambient temperature
is kept to a maximum of +85°C as specified in the Operating
Ratings section.
As a convenience to the user, the ADC08D1500 incorporates
a thermal diode to aid in temperature measurement. Howev-
er, this diode has not been characterized and National Semi-
conductor has no information to provide regarding its
characteristics. Hence, no information is available as to the
temperature accuracy attainable when using this diode.
Please note that the following are general recommendations
for mounting exposed pad devices onto a PCB. This should
be considered the starting point in PCB and assembly pro-
cess development. It is recommended that the process be
developed based upon past experience in package mounting.
The package of the ADC08D1500 has an exposed pad on its
back that provides the primary heat removal path as well as
excellent electrical grounding to the printed circuit board. The
land pattern design for lead attachment to the PCB should be
the same as for a conventional LQFP, but the exposed pad
must be attached to the board to remove the maximum
amount of heat from the package, as well as to ensure best
product parametric performance.
To maximize the removal of heat from the package, a thermal
land pattern must be incorporated on the PC board within the
footprint of the package. The exposed pad of the device must
be soldered down to ensure adequate heat conduction out of
the package. The land pattern for this exposed pad should be
at least as large as the 5 x 5 mm of the exposed pad of the
package and be located such that the exposed pad of the
device is entirely over that thermal land pattern. This thermal
land pattern should be electrically connected to ground. A
clearance of at least 0.5 mm should separate this land pattern
from the mounting pads for the package pins.
JA
(junction to ambient thermal resistance) should not ex-
A
35
Since a large aperture opening may result in poor release, the
aperture opening should be subdivided into an array of small-
er openings, similar to the land pattern of Figure 16.
To minimize junction temperature, it is recommended that a
simple heat sink be built into the PCB. This is done by includ-
ing a copper area of about 2 square inches (6.5 square cm)
on the opposite side of the PCB. This copper area may be
plated or solder coated to prevent corrosion, but should not
have a conformal coating, which could provide some thermal
insulation. Thermal vias should be used to connect these top
and bottom copper areas. These thermal vias act as "heat
pipes" to carry the thermal energy from the device side of the
board to the opposite side of the board where it can be more
effectively dissipated. The use of 9 to 16 thermal vias is rec-
ommended.
The thermal vias should be placed on a 1.2 mm grid spacing
and have a diameter of 0.30 to 0.33 mm. These vias should
be barrel plated to avoid solder wicking into the vias during
the soldering process as this wicking could cause voids in the
solder between the package exposed pad and the thermal
land on the PCB. Such voids could increase the thermal re-
sistance between the device and the thermal land on the
board, which would cause the device to run hotter.
If it is desired to monitor die temperature, a temperature sen-
sor may be mounted on the heat sink area of the board near
the thermal vias. .Allow for a thermal gradient between the
temperature sensor and the ADC08D1500 die of θ
typical power consumption = 2.8 x 1.8 = 5°C. Allowing for 6°
C, including some margin for temperature drop from the pad
to the temperature sensor, then, would mean that maintaining
a maximum pad temperature reading of 124°C will ensure that
the die temperature does not exceed 130°C, assuming that
the exposed pad of the ADC08D1500 is properly soldered
down and the thermal vias are adequate. (The inaccuracy of
the temperature sensor is additional to the above calculation).
2.7 LAYOUT AND GROUNDING
Proper grounding and proper routing of all signals are essen-
tial to ensure accurate conversion. A single ground plane
should be used, instead of splitting the ground plane into ana-
log and digital areas.
Since digital switching transients are composed largely of
high frequency components, the skin effect tells us that total
ground plane copper weight will have little effect upon the
logic-generated noise. Total surface area is more important
than is total ground plane volume. Coupling between the typ-
ically noisy digital circuitry and the sensitive analog circuitry
can lead to poor performance that may seem impossible to
FIGURE 16. Recommended Package Land Pattern
www.national.com
J-PAD
20152121
times