C200HW-PD025 Omron, C200HW-PD025 Datasheet - Page 10
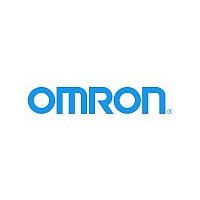
C200HW-PD025
Manufacturer Part Number
C200HW-PD025
Description
Power Supply
Manufacturer
Omron
Datasheet
1.CVM1-MP702-V1.pdf
(70 pages)
Specifications of C200HW-PD025
Lead Free Status / Rohs Status
Lead free / RoHS Compliant
Machine performance improved with high-speed,
high-precision, flexible motion control.
F-18
● MECHATROLINK-II-compatible
Single Cable Connection and
Flexible Routing!
With MECHATROLINK-II*, the Servo Drive
can be easily connected with a single cable
(2-core shielded twisted pair cable). The
wire savings over the total length of 50 m (or
30 m for 16 axes) enables Racks to be more
freely located.
Time Saved in Startup and
Maintenance
Servo Drive parameters can be set from the
PLC.
Settings and adjustments can be made from
one location, without connecting the Support
Software to individual Servo Drives. In
addition, Servo Drive alarm status, speed,
and torque monitoring can be centralized at
the PLC.
● Position Control Units
Two Types of Outputs and
Control of 1, 2, or 4 Axes
Select from 1-axis, 2-axis, and 4-axis
models with either open-collector output or
line-driver output to suit a number of
different applications.
A Variety of Positioning Functions
There are 2 operating modes: direct operation
(position, speed, acceleration, and
deceleration data specified from the ladder
program), which is effective for setting target
positions, speeds, and acceleration rates
immediately or during operation, and memory
operation, where fixed patterns are stored
beforehand in the Unit and used for operation.
There are also a variety of positioning
functions, such as interrupt feeding, which is
effective for feeder control, and forced interrupt,
which is useful in emergencies.
● MECHATROLINK-II-compatible
Easy System Construction
Up to 30 physical axes and two virtual axes,
making a total of 32, can be controlled, and the
servo interface is handled by high-speed servo
communications (MECHATROLINK-II*). This
makes it possible to control multiple axes with
less wiring.
Position Control Units
Motion Control Units
Easy Data Control
High-speed servo communications lets you
read programs and parameter settings from
CX-Programmer on a PC. You can also
read and track the operating status of
parameter settings inside the Servo Driver.
Easy Motion Control
Motion control, including positioning,
synchronizing (electronic gears, electronic
cams, tracking), speed, and torque control,
can all be handled by the CS1.
Eight motion tasks can be used for
simultaneous motion program execution.
SMART STEP
2 Servo
Drive with
Pulse-string
Input
Servomotor
Pulses
OMNUC G-series/
G5-series
MECHATROLINK-II
Servo Drive with
Built-in
Communications
MECHATROLINK-II
Position Control Unit
Position
Control Unit
Com-
muni-
cations
Servomotor
Communications
Servomotor
MECHATROLINK-II
Motion Control Unit
Motion Control Units
● Motion Control Units
Easy Programming with
G Language and Multitasking
The Motion Control Units use G language to
ensure easy programming. The Units have
a large programming capacity of up to 100
programs and 2,000 program blocks, and
allow independent operation of 4 tasks.
High-speed Interlocks
Interrupt programs can be executed from
the motion control program using D codes
(interrupt codes). Easy, fast interlocks
ensure greater production efficiency.
Synchronous control (electronic gears,
electronic cams) is also possible.
OMNUC W-series
MECHATROLINK-II
Servo Drive with
Built-in
Communications
Analog
Customizable Counter Units
Servomotor
OMNUC G-series/
G5-series
General-purpose
Servo Drive
Encoder
Pulse/analog output
● Customizable Counter Units
A Whole New Concept,
Customizable Counter Units
A high-speed PLC with 20 I/O points, a
2-axis high-speed counter, and 2 pulse or
analog outputs have all been combined into 1
Unit. The Customizable Counter Units allow
easy execution of complicated applications.
CX-Programmer
High-speed
overhead
0.1 ms
PLC
Servomotor
Servo Driver
CX-Motion
CX-Position
CX-Motion-NCF
CX-Motion-MCH
Customizable
Counter Unit
CX-One
Analog output
20 I/O points
Pulse output
Analog input
Counter
PLC
Easy Control for Bending and
Pressing
It is possible to switch between speed
control and torque control from the ladder
program, enabling bending operation for
metals and pressing operation for bonding.
Motion Applications with
High-speed Response
A wide range of interrupt functions and
superior response performance enable
motion applications requiring high-speed
response using pulse I/O.
Note: MECHATROLINK-II is aregistered trademark of the
MECHATROLINK Members Association.
Torque
CS1W-HCA22
Speed
Torque Sensor
Position
Torque Speed
Servomotor
Analog input
Servo Driver
F-19