MAX11068EVKIT+ Maxim Integrated Products, MAX11068EVKIT+ Datasheet - Page 33
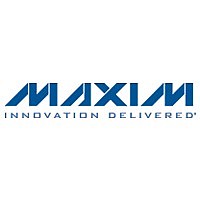
MAX11068EVKIT+
Manufacturer Part Number
MAX11068EVKIT+
Description
KIT SMART BATT MEASUREMENT 12CH
Manufacturer
Maxim Integrated Products
Specifications of MAX11068EVKIT+
Main Purpose
Power Management, Battery Monitor, Car
Utilized Ic / Part
MAX11068
Primary Attributes
Monitors Current, Voltage, Temperature
Secondary Attributes
1 ~ 12 Cell- Li-Ion, 1 ~ 12 Cell- NiMH
Lead Free Status / RoHS Status
Lead free / RoHS Compliant
Embedded
-
High-power batteries are often used in noisy environ-
ments subject to high dv/dt supply noise and EMI noise.
For example, the supply noise of a power inverter driving
a high-horsepower motor produces a large square wave
at the battery terminals, even though the battery is also a
high-power battery. Typically, the battery dominates the
task of absorbing this noise, since it is impractical to put
hundreds of farads at the inverter. Supply noise between
two modules occurs due to the very large current
transients that are often present in high-power battery
systems. Even very-low-impedance connections of only
a few milliohms between the various battery modules
and the load can produce substantial voltage noise that
would not allow an AC-coupled ground-referenced I
communication system to work reliably. Voltage noise is
also induced through the batteries’ impedance, which
cannot be easily reduced. A unique level-shifting SMBus
ladder communication architecture solves these prob-
lems by referencing the communication signals from
one module to the next from a common voltage that is
shared by both modules. The supply noise seen by the
communication interface is thus greatly reduced and is
then able to be rejected completely in most cases.
In a typical application of up to approximately 200A to
400A, the GND
of the battery stack without the communication path
experiencing adverse affects from bus-bar-induced
noise. In some high-current applications where the
load current is greater than 400A, or the module inter-
connect impedance is more than a couple milliohms,
further precautions may be necessary to ensure optimal
performance. In these cases, the extreme current levels
across even tiny interconnect impedances can result in
significant noise due to the GND
Applications with one or more of the following conditions
may benefit from connecting GND
U The bus bar impedance is greater than 1mI to 2mI.
U Battery pack current steps are greater than 400A in
U The RC time constant at cell 12 does not match the
In applications that meet these conditions, a Kelvin con-
nection should be made from GND
next-higher module. For applications that do not have
these conditions, the Kelvin-style connection is optional.
less than 100Fs.
time constant at DCIN.
U
supply may be connected to the top
12-Channel, High-Voltage Sensor, Smart
Noise Tolerance
U
reference connection.
U
with a Kelvin style:
U
to AGND of the
Data-Acquisition Interface
2
C
Figure 27. Module-to-Module DCIN Kelvin Connection
This connection can reject noise induced across the
bus bar to further improve noise immunity for the I
interface. Figure 27 demonstrates how to properly
Kelvin-connect modules for maximum noise immunity.
This method requires careful attention to the mechanical
design of the module, since an extra module terminal
connection is required. DCIN and C12 should not share
a common terminal of a module for Kelvin-connected
modules.
REFERENCE OF
NEXT MODULE
TO GROUND
PCK+
PCK+
C12
C11
C2
C1
C0
C12
C11
C2
C1
C0
MODULE
MODULE
GND
AGND
GND
AGND
N+1
U
U
N
DCIN
DCIN
2
33
C