MAX11068EVKIT+ Maxim Integrated Products, MAX11068EVKIT+ Datasheet - Page 19
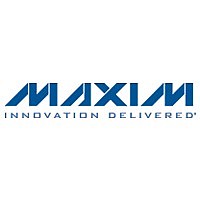
MAX11068EVKIT+
Manufacturer Part Number
MAX11068EVKIT+
Description
KIT SMART BATT MEASUREMENT 12CH
Manufacturer
Maxim Integrated Products
Specifications of MAX11068EVKIT+
Main Purpose
Power Management, Battery Monitor, Car
Utilized Ic / Part
MAX11068
Primary Attributes
Monitors Current, Voltage, Temperature
Secondary Attributes
1 ~ 12 Cell- Li-Ion, 1 ~ 12 Cell- NiMH
Lead Free Status / RoHS Status
Lead free / RoHS Compliant
Embedded
-
The BMS in an electric vehicle monitors cell voltage,
pack current, and temperature. The BMS is composed
of two components. The first is the master controller of
the system that handles all communication with the VCS.
It also handles state of charge, state of health, and fault-
management features of the battery pack. The second
component is the data-monitoring function, which gath-
ers information on the conditions of the battery cells,
takes voltage/current/temperature measurements, and
signals safety faults.
The slave monitor controller (SLC) is directly connected
to the series stack battery cells. The SLC measures cell
voltages and module temperature, as well as controls
the cell-charge equalization feature that keeps all cells
balanced to equal states of charge. The SLCs are also
designed to report alarm conditions such as cell over-
voltage or undervoltage, sense wire-open circuits, and
in the case of Li+ battery chemistries, overtemperature
situations. The SLCs are managed by the master control-
ler. The master controller orchestrates all data acquisi-
tion and cell-balancing tasks in the slaves. The master
also measures the pack current coincident to voltage
measurements so that state of health of the battery pack
can be determined. Measurement of the current through
the pack is made across a low-value shunt resistor or
hall sensor.
The MAX11068 contains 13 analog inputs that are used
for the differential measurement of as many as 12 bat-
tery cells. Each differential cell input can withstand up
to 9.0V and can be included in the measurement cycle
through the cell-channel scan-enable bits of the CELLEN
register (address 0x09). Cell inputs are measured differ-
entially and level shifted down to the internal ADC by a
high-voltage mux and ADC preamp. The common-mode
range of the cell inputs from C2 to C12 is 0.5V to V
2.9V. Common-mode range for C1 is limited to 7.0V and
for C0 it is limited to voltages within 50mV of AGND for
proper measurements. The absolute maximum differen-
tial input between two inputs must always be observed,
which is 9.0V.
The application circuit shows RC filtering for each cell
input. The values of the resistors are chosen in large
part depending on the cell-balancing functionality that is
desired. The capacitor value chosen complements the
12-Channel, High-Voltage Sensor, Smart
Battery-Management
Cell Inputs C0–C12
System (BMS)
HV
Data-Acquisition Interface
-
resistor values to provide lowpass filtering of the ADC
measurement. Capacitor values should be in the 100nF
to 1FF range.
The first cell position between C1 and C0 must be popu-
lated for all applications with a voltage of at least 500mV.
This ensures accurate measurements for all other cell
positions as defined by the ADC specifications. When
implementing a module configuration with fewer than 12
cells, the first cell position should always be used, and
then other cell positions may be used in any configura-
tion. Any unused cell positions should have their inputs
shorted together. Random connection of cells or the
high-voltage supplies during module configuration does
not cause adverse effects.
When a cell is enabled for acquisition by setting the
associated scan-enable bits in the CELLEN register
(address 0x09), the appropriate cell differential input is
scheduled for conversion. The auxiliary input channels
along with the self-diagnostic channel may be similarly
enabled using their enable bits in the ADCCFG register
(address 0x08).
Conversion begins with the setting of the SCAN bit in the
SCANCTRL register. The setting of the SCAN bit may
be accomplished using either the WRITEALL command
or the WRITEDEVICE command, depending on whether
all devices are expected to perform the conversion. If
the ADC is still busy from a previous acquisition scan,
the scan command is ignored. Each module in a sys-
tem begins the measurement scan cycle as soon as it
receives the scan signal. The measurement order of the
inputs during a cycle is as follows:
1) All enabled cell inputs phase 1, descending order
2) All enabled cell inputs phase 2, descending order
3) Self-diagnostic measurement phase 1, if enabled
4) Self-diagnostic measurement phase 2, if enabled
5) All enabled auxiliary inputs phase 1, ascending order
The complete acquisition of the cell voltages takes place
in two phases, which is shown in Figure 10. The first
phase is the raw cell-voltage acquisition. In this stage,
the ADC scans through all the enabled cell input chan-
nels, starting with the highest cell.
(12–1)
(12–1)
(AUXIN1, AUXIN2)
Measurement Scanning
19