ADP1621ARMZ-R7 Analog Devices Inc, ADP1621ARMZ-R7 Datasheet - Page 14
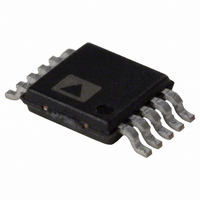
ADP1621ARMZ-R7
Manufacturer Part Number
ADP1621ARMZ-R7
Description
IC CTRLR DC/DC PWM STEPUP 10MSOP
Manufacturer
Analog Devices Inc
Type
Step-Up (Boost)r
Datasheet
1.ADP1621ARMZ-R7.pdf
(32 pages)
Specifications of ADP1621ARMZ-R7
Internal Switch(s)
No
Synchronous Rectifier
Yes
Number Of Outputs
1
Current - Output
1A
Frequency - Switching
100kHz ~ 1.5MHz
Voltage - Input
2.9 ~ 5.5 V
Operating Temperature
-40°C ~ 125°C
Mounting Type
Surface Mount
Package / Case
10-MSOP, Micro10™, 10-uMAX, 10-uSOP
Primary Input Voltage
5.5V
No. Of Outputs
1
Output Current
1A
No. Of Pins
10
Operating Temperature Range
-40°C To +125°C
Msl
MSL 1 - Unlimited
Frequency Max
1.5MHz
Termination Type
SMD
Lead Free Status / RoHS Status
Lead free / RoHS Compliant
For Use With
ADP1621-EVALZ - BOARD EVALUATION FOR ADP1621
Voltage - Output
-
Power - Output
-
Lead Free Status / RoHS Status
Lead free / RoHS Compliant, Lead free / RoHS Compliant
Other names
ADP1621ARMZ-R7
ADP1621ARMZ-R7TR
ADP1621ARMZ-R7TR
ADP1621
APPLICATION INFORMATION: BOOST CONVERTER
In this section, an analysis of a boost converter is presented,
along with guidelines for component selection. A typical boost-
converter application circuit is shown in Figure 1.
DUTY CYCLE
To determine the worst-case inductor current ripple, output voltage
ripple, and slope-compensation factor, it is first necessary to
determine the system duty cycle. The duty cycle in continuous
conduction mode (CCM) is calculated by the equation
where V
voltage, and V
typical Schottky diode has a forward-voltage drop of 0.5 V.
The GATE minimum on and off times determine the minimum
and maximum duty cycles, respectively. The minimum on and
off times are typically 180 ns and 190 ns, respectively. The
minimum and maximum duty cycles are given by
where D
cycle, t
time, t
Note that when the converter tries to operate at a duty cycle
lower than D
the output voltage regulation (see the Light Load Operation
section).
SETTING THE OUTPUT VOLTAGE
The output voltage is set through a voltage divider from the
output voltage to the FB input. The feedback resistor ratio sets
the output voltage of the system. The regulation voltage at FB is
1.215 V. The output voltage is given by (see Figure 1)
The input bias current into FB is 25 nA typical, 70 nA
maximum. For a 0.1% degradation in regulation voltage and
with 70 nA bias current, R2 must be less than 18 kΩ, which
results in 68 μA of divider current. Choose the value of R1 to set
the output voltage. Using higher values for R2 results in reduced
output voltage accuracy due to the input bias current at the FB
pin, whereas lower values cause increased quiescent current
consumption.
INDUCTOR CURRENT RIPPLE
Choose a peak-to-peak inductor ripple current between 20%
and 40% of the average inductor current. A good starting point
V
D
D
D
SW
ON,MIN
OUT
MIN
MAX
=
MIN
OUT
is the switching period, and f
V
=
=
is the minimum duty cycle, D
OUT
=
is the desired output voltage, V
is the minimum on time, t
V
. 1
MIN
t
1
ON
OUT
D
−
215
t
+
is the forward-voltage drop of the diode. A
SW
, pulse-skipping modulation occurs to maintain
,
t
V
MIN
OFF
+
D
t
V
SW
V
,
−
MIN
×
=
D
V
⎛ +
⎜
⎝
t
1
ON
IN
=
,
MIN
1
R2
R1
−
(
×
t
⎞
⎟
⎠
OFF
f
SW
,
MIN
SW
OFF,MIN
is the switching frequency.
×
MAX
f
SW
IN
is the maximum duty
is the minimum off
)
is the input
Rev. A | Page 14 of 32
(1)
(2)
(3)
(4)
for a design is to choose the peak-to-peak ripple current to be
30% of 1/(1 − D) times the maximum load current:
where ΔI
is the maximum load current required by the application.
INDUCTOR SELECTION
The inductor value choice is important because it dictates
the inductor current ripple and therefore the voltage ripple
at the output.
The average inductor current, I
and the peak-to-peak inductor ripple current is inversely
proportional to the inductor value:
where f
Assuming continuous conduction mode (CCM) operation, the
peak inductor current is given by
Smaller inductor values are typically smaller in size and usually
less expensive, but increase the ripple current. Larger ripple current
also increases the power loss in the inductor core. Too large an
inductor value results in added expense and may impede load
transient responses because it reduces the effect of slope
compensation.
Assuming the ripple current is 30% of 1/(1 − D) times the max-
imum load current, a reasonable choice for the inductor value is
From this starting point, modify the inductance to obtain the
right balance of size, cost, and output voltage ripple while
maintaining the inductor ripple current between 20% and 40%
of 1/(1 − D) times the maximum load current. Keep in mind
that the inductor saturation current must be greater than the
peak inductor current. Magnetically shielded inductors are
generally recommended, although they cost slightly more than
unshielded inductors.
Also, losses due to the inductor winding resistance reduce the
efficiency of the boost converter. This power loss is given by
where P
inductor, and R
Δ
L
Δ
I
I
P
L
L
L
I
I
=
,
SW
,
,
AVE
PK
W
L
L
L,W
L
0
=
=
is the switching frequency, and L is the inductor value.
is the peak-to-peak inductor ripple current, and I
3 .
=
=
V
is the power dissipation in the winding of the
0
=
V
⎛
⎜
⎝
×
f
3 .
I
IN
1
SW
IN
I
1
I
LOAD
1
f
−
×
LOAD
LOAD
×
SW
−
−
W
×
×
D
I
D
D
D
D
is the winding resistance.
LOAD
×
L
×
1
+
I
⎞
⎟
⎠
−
(
LOAD
2
1
Δ
,
×
D
−
MAX
2
I
R
L
D
,
MAX
W
=
)
I
1
LOAD
−
D
L,AVE
+
, is given by
2
V
×
IN
f
SW
×
D
×
L
LOAD,MAX
(10)
(5)
(6)
(7)
(8)
(9)