EVAL-ADXL343Z-M Analog Devices, EVAL-ADXL343Z-M Datasheet - Page 26
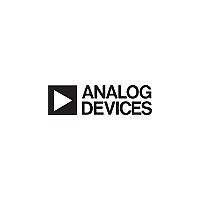
EVAL-ADXL343Z-M
Manufacturer Part Number
EVAL-ADXL343Z-M
Description
Acceleration Sensor Development Tools EB
Manufacturer
Analog Devices
Datasheet
1.EVAL-ADXL343Z.pdf
(36 pages)
Specifications of EVAL-ADXL343Z-M
Rohs
yes
Tool Is For Evaluation Of
ADXL343
Acceleration
2 g, 4 g, 8 g, 16 g
Sensing Axis
Triple Axis
Interface Type
I2C, SPI
Operating Voltage
2 V to 3.6 V
Maximum Operating Temperature
+ 85 C
Minimum Operating Temperature
- 40 C
Operating Current
140 uA
Output Type
Digital
Product
Evaluation Systems
Sensitivity
256 LSB/g, 128 LSB/g, 64 LSB/g, 32 LSG/g
Factory Pack Quantity
1
ADXL343
APPLICATIONS INFORMATION
POWER SUPPLY DECOUPLING
A 1 µF tantalum capacitor (C
(C
recommended to adequately decouple the accelerometer from
noise on the power supply. If additional decoupling is necessary,
a resistor or ferrite bead, no larger than 100 Ω, in series with V
may be helpful. Additionally, increasing the bypass capacitance
on V
ceramic capacitor may also improve noise.
Care should be taken to ensure that the connection from the
ADXL343
because noise transmitted through ground has an effect similar
to noise transmitted through V
V
on the V
the supplies, as previously mentioned, may be necessary.
MECHANICAL CONSIDERATIONS FOR MOUNTING
The
close to a hard mounting point of the PCB to the case. Mounting
the
Figure 35, may result in large, apparent measurement errors
due to undampened PCB vibration. Locating the accelerometer
near a hard mounting point ensures that any PCB vibration at
the accelerometer is above the accelerometer’s mechanical sensor
resonant frequency and, therefore, effectively invisible to the
accelerometer. Multiple mounting points close to the sensor
and/or a thicker PCB also help to reduce the effect of system
resonance on the performance of the sensor.
INTERRUPT
DD I/O
I/O
CONTROL
ADXL343
ADXL343
) at V
S
to a 10 µF tantalum capacitor in parallel with a 0.1 µF
be separate supplies to minimize digital clocking noise
S
supply. If this is not possible, additional filtering of
DD I/O
ground to the power supply ground has low impedance
Figure 35. Incorrectly Placed Accelerometers
at an unsupported PCB location, as shown in
should be mounted on the PCB in a location
placed close to the
C
MOUNTING POINTS
S
Figure 34. Application Diagram
ACCELEROMETERS
INT1
INT2
V
V
S
S
SDO/ALT ADDRESS
ADXL343
PCB
GND
S
) at V
SDA/SDI/SDIO
S
SCL/SCLK
V
. It is recommended that V
V
DD I/O
DD I/O
S
ADXL343
and a 0.1 µF ceramic capacitor
CS
C
IO
supply pins is
3- OR 4-WIRE
SPI OR I
INTERFACE
2
C
S
and
Rev. 0 | Page 26 of 36
S
TAP DETECTION
The tap interrupt function is capable of detecting either single
or double taps. The following parameters are shown in Figure 36
for a valid single and valid double tap event:
•
•
•
•
If only the single tap function is in use, the single tap interrupt
is triggered when the acceleration goes below the threshold, as
long as DUR has not been exceeded. If both single and double
tap functions are in use, the single tap interrupt is triggered
when the double tap event has been either validated or
invalidated.
Figure 36. Tap Interrupt Function with Valid Single and Double Taps
The tap detection threshold is defined by the THRESH_TAP
register (Address 0x1D).
The maximum tap duration time is defined by the DUR
register (Address 0x21).
The tap latency time is defined by the latent register
(Address 0x22) and is the waiting period from the end
of the first tap until the start of the time window, when a
second tap can be detected, which is determined by the
value in the window register (Address 0x23).
The interval after the latency time (set by the latent register) is
defined by the window register. Although a second tap must
begin after the latency time has expired, it need not finish
before the end of the time defined by the window register.
LATENCY
(LATENT)
TIME
FIRST TAP
TIME LIMIT FOR
SINGLE TAP
INTERRUPT
TAPS (DUR)
SECOND TAP (WINDOW)
TIME WINDOW FOR
SECOND TAP
DOUBLE TAP
INTERRUPT
Data Sheet
THRESHOLD
(THRESH_TAP)