PDSP16256A Zarlink Semiconductor, PDSP16256A Datasheet - Page 16
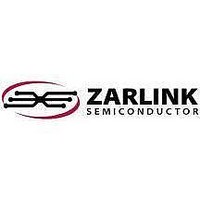
PDSP16256A
Manufacturer Part Number
PDSP16256A
Description
Programmable FIR Filter
Manufacturer
Zarlink Semiconductor
Datasheet
1.PDSP16256A.pdf
(25 pages)
Available stocks
Company
Part Number
Manufacturer
Quantity
Price
Company:
Part Number:
PDSP16256ABO
Manufacturer:
MT
Quantity:
28
16
Using a Remote Master
When a remote master is used to load
coefficients,
conventional peripheral interface is then provided. It
is not possible, however, to read coefficients already
stored. The master supplies an address and data
bus, and writes to the PDSP16256 occur under the
control of synchronous
Coefficient Control Register pin (CCS) must be driven
by a master address line higher in significance than
A7:0. Both the
the load operation to occur. When loading the control
register the
cycles, see Fig. 20. Since the internal write operation
is actually performed with the system clock, it is
necessary for the clock to be present during the
transfer.
The
loaded as a single 16 bit word or two 8-bit bytes. The
latter saves on connections to the remote master.
Address bits A7:0 are used in byte mode. 16-bit word
mode uses bits A6:0, A7 being redundant. When
writing in byte mode the least significant byte (A0 = 0)
must be written first followed by the most significant
byte (A0 = 1).
In byte mode the internal comparison between C15:12
and C11:8 is made, regardless of the state of
For this reason pins C15:8 should all be tied low when
a remote master is used with byte transfers. This
ensures that the internal comparison gives equality
and allows the load operation to occur.
PDSP16256/A
BYTE
input defines whether coefficients are
CS
EPROM
signal must be held low for a further 2
WEN
and
must be tied high and a
CS
CS
signals must be low for
and
WEN
inputs. The
EPROM
.
The address and coefficient buses plus
the
set up and hold times with respect to the system
clock, see Fig 20 and Switching Characteristics.
This synchronous interface is optimum for the
majority of high end applications, when individual
coefficients must be updated at sample clock rates.
However, if the coefficients are to be loaded under
software control from a general purpose
microprocessor, the processor’s
probably be asynchronous with the SCLK clock
used by the PDSP16256. In this case external
synchronising logic is needed, as shown in Fig.18.
Fig. 19 shows the recommended loading sequence
and filter operation initiation. The simplest technique
is to reset the device prior to loading a set of
coefficients. Coefficients may be loaded once BUSY
returns low or 22 cycles after
When loading a device from a remote master the
control register must be loaded first followed by the
filter coefficients. Fig. 19 shows the required loading
sequence, two examples are given one for byte
mode the other for word mode. A gap of at least one
cycle must be left after loading the control register
before loading the first coefficient.
Filter operations are started by presenting the first
data word at the same time as raising signal FEN;
FRUN should always be low.
WEN
and
CS
signals must all meet the specified
RES
WRITE STROBE
is taken high.
will