NIS3001 ON Semiconductor, NIS3001 Datasheet - Page 15
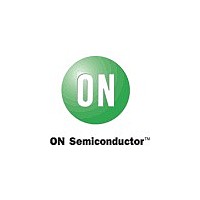
NIS3001
Manufacturer Part Number
NIS3001
Description
Integrated Driver And Mosfet Power Chip For Synchronous Buck Controllers
Manufacturer
ON Semiconductor
Datasheet
1.NIS3001.pdf
(18 pages)
as shown in Figure 20. Dividing the larger die pads into
smaller screen openings reduces the risk of solder voiding
and allows the solder joints for the smaller terminal pads to
be at the same height as the larger ones.
Package Placement onto the PCB
tend to center itself and correct for slight placement errors
during the reflow process due to the surface tension of the
solder.
Solder Reflow
the solder paste, a standard surface mount reflow process
can be used to mount the part. Figure 21 is an example of
a standard reflow profile. The exact profile will be
determined, and is available, by the manufacture of the
paste since the chemistry and viscosity of the flux matrix
will vary. These variations will require small changes in
the profile in order to achieve an optimized process.
0.05 mm or better is recommended. The package will
Figure 20. Solder stencil design illustrating smaller
Pick and place equipment with the standard tolerance of
stencil openings over the larger exposed die pads.
Once the package is placed on the PC board along with
12X
2X
0.789
1.000
0.356
12X
1.856
4X
0.700
33X
0.928
8X
0.811
8X
Die Attach
Pads
1.621
1.015
6X
4X
http://onsemi.com
NIS3001
15
not more than 2 C/sec during the initial stages of the reflow
profile. The soak zone then occurs when the part is
approximately 150 C and should last for 30 to 120 seconds.
Typically, extending the time in the soak zone will reduce
the risk of voiding within the solder. The temperature is
then raised and will be above the liquidus of the solder for
30 to 100 seconds depending on the mass of the board. The
peak temperature of the profile should be between 205 and
225 C for eutectic Sn/Pb solder.
completed by using the recommended procedures set forth
by the flux manufacturer.
Final Solder Inspection
performed with the use of an X−ray inspection system.
With this tool, one can locate defects such as shorts
between pads, open contacts, voids within the solder as
well as any extraneous solder.
should be rotated on its side to inspect the sides of the solder
joints with an X−ray inspection system. The solder joints
should have enough solder volume with the proper
stand−off height so that an “Hour Glass” shaped connection
is not formed as shown below in Figure 22. “Hour Glass”
solder joints are a reliability concern and must be avoided.
250
200
183
150
100
Figure 21. Typical reflow profile for eutectic tin/lead
In general, the temperature of the part should be raised
If required, removal of the residual solder flux can be
The inspection of the solder joints is commonly
In addition to searching for defects, the mounted device
50
Preferred
Solder Joint
0
0
Less than
2 C/sec
Figure 22. Side view of NIS3001 illustrating
preferred and undesirable solder joints.
100
Î Î Î Î Î
Î Î
Î Î Î Î
(30 to 120 sec)
200
Î Î Î Î
Î Î
PCB
solder.
Soak
Zone
Time (sec)
300
Peak of 225 C
Î Î Î
Î Î Î
Î Î Î
Liquidus
Above
Time
Î Î Î Î
Î Î Î Î
Î Î Î Î
Undesirable
“Hour Glass”
Solder Joint
400
500