AT-FM-10K BANNER ENGINEERING, AT-FM-10K Datasheet - Page 9
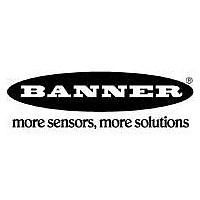
AT-FM-10K
Manufacturer Part Number
AT-FM-10K
Description
Control Module, Two Hand; Solid State (NPN, PNP), Relay (Auxiliary N.C.); 200 W
Manufacturer
BANNER ENGINEERING
Type
Safetyr
Specifications of AT-FM-10K
Brand/series
Duo-Touch
Contact Form
SPDT-NO/NC
Dimensions
22.5mmW×84mmH×118mmD
Enclosure Rating
IP20
Indicator
4 Green LED, 1 Red LED
Ip Rating
IP20
Material, Casing
Polycarbonate
Mounting
DIN Rail
Mounting Type
DIN Rail
Number Of Outputs
4
Output Type
Digital/Relay
Power Consumption
200 W
Primary Type
Controller
Standards
cULus, cCSAus, CE
Temperature, Operating
0 to +50 °C
Voltage, Supply
24 VDC
Coil Voltage Vac Nom
24V
Coil Voltage Vdc Nom
24V
Contact Current Max
6A
Contact Voltage Ac Nom
250V
Contact Voltage Dc Nom
24V
Contact Configuration
SPST-NO
No. Of Poles
1
Lead Free Status / Rohs Status
RoHS Exempt Product
For Use With
Two-Hand Control
Connection to the Guarded Machine
The wiring diagrams show a generic connection of the Safety Module’s redundant output contacts to machine primary control elements
MPCE1 and MPCE2. An MPCE is defined as an electrically-powered element, external to the Safety Module, which directly controls the
machine’s normal operating cycle so that it is the last (in time) to operate when the cycle is either initiated or arrested. Some older ma-
chines offer only one MPCE; for such machines, it may be necessary to add a second MPCE to establish the appropriate level of safety
integrity (e.g., control reliability).
The connection of the safety outputs must be in such a manner that the stop command issued by the Safety Module can not be overrid-
den by a device or circuit that is not at the same level of safety integrity. This means that the safety outputs are interfaced on the output
of the machine logic (e.g., PLC or PC). Then, normally, a feedback signal identifies to the machine logic the status of the Safety Module
and, if possible, the status of the MPCEs.
In summary, Control Reliability (OSHA 29CFR1910.217, ANSI B11, and ANSI/RIA R15.06) and Category 3 and 4 (ISO13849-1) require-
ments demand that a single failure does not lead to the loss of the safety function, or does not prevent a normal or immediate stop from
occurring. The failure or the fault must be detected at or before the next demand of safety (e.g., at the beginning or end of a cycle, or
when a safeguard is actuated). The safety-related function of the machine control then must issue an immediate stop command or pre-
vent the next machine cycle or hazardous situation until the failure or fault is corrected.
External Device Monitoring
To satisfy the requirements of Control Reliability (OSHA and ANSI) and Category 3 and 4 of ISO 13849-1 (EN 954-1), the machine
primary control elements (MPCEs) must each offer a normally closed, forced-guided (mechanically linked) monitor contact. Connect one
normally closed monitor contact from each master stop control element in series to Y1 and Y2 (see wiring diagrams).
In operation, if one of the switching contacts of either MPCE fails in the energized condition, the associated monitor contact will remain
open. Therefore, it will not be possible to reset the Safety Module. If no MPCE-monitor contacts are monitored, a jumper must be instal-
led between terminals Y1 and Y2 (dotted line), as shown in the hookup drawings. It is the user’s responsibility to ensure that any
single failure will not result in a hazardous condition and will prevent a successive machine cycle.
Overvoltage Category II and III Installations (EN 50178 and IEC 60664-1)
The Safety Module is rated for Overvoltage Category III when voltages of 1V to 150V ac/dc are applied to the output relay contacts. It is
rated for Overvoltage Category II when voltages of 151V to 250V ac/dc are applied to the output relay contacts and no additional precau-
tions are taken to attenuate possible overvoltage situations in the supply voltage. The Module can be used in an Overvoltage Category III
environment (with voltages of 151V to 250V ac/dc) if care is taken either to reduce the level of electrical disturbances seen by the Module
to Overvoltage Category II levels by installing surge suppressor devices (e.g., arc suppressors), or to install extra external insulation in
order to isolate both the Safety Module and the user from the higher voltage levels of a Category III environment.
For Overvoltage Category III installations with applied voltages from 151V to 250V ac/dc applied to the output contact(s): the
Safety Module may be used under the conditions of a higher overvoltage category where appropriate overvoltage reduction is provided.
Appropriate methods include:
AT-FM-10K Two-Hand Control Module
P/N 64137 F
• An overvoltage protective device
• A transformer with isolated windings
• A distribution system with multiple branch circuits (capable of diverting energy of surges)
• A capacitance capable of absorbing energy of surges
• A resistance or similar damping device capable of dissipating the energy of surges
WARNING: . . . Interfacing MSCs
NEVER wire an intermediate device(s) (e.g., PLC, PES, PC) between the Safety Module outputs and the Master Stop
Control Element it switches in such a manner that in the event of a failure there is a loss of the safety stop com-
mand, OR in such a manner that the safety function can be suspended, overridden, or defeated, unless accomplish-
ed with the same or greater degree of safety.
Whenever forced-guided, mechanically linked relays are added as intermediate switching devices, a normally closed forced-
guided monitor contact from each relay must be added to the series feedback loop between Safety Module terminals S31
and S32.
www.bannerengineering.com - tel: 763-544-3164
9