hip6301vcbza-t Intersil Corporation, hip6301vcbza-t Datasheet - Page 11
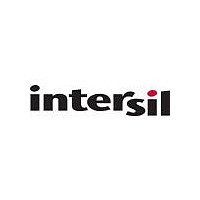
hip6301vcbza-t
Manufacturer Part Number
hip6301vcbza-t
Description
Microprocessor Core Voltage Regulator Multiphase Buck Pwm Controller
Manufacturer
Intersil Corporation
Datasheet
1.HIP6301VCBZA-T.pdf
(20 pages)
example, a 500kHz system detecting a change from 1.300V
to 1.800V requires between 84ms and 88ms to complete the
change.
If a new VID code is detected during a DAC change and the
DAC can continue toward the new VID code without
changing direction, processing continues without
interruption. If a new VID code is detected during a DAC
change and the DAC has to change direction in order to
proceed toward then new VID code, processing halts. A two-
cycle wait period is initiated and processing continues as
above. These decisions are made with reference to the
transitional DAC value rather than the original target value.
1.85V
1.85V
1.10V
1.10V
FIGURE 6. VCORE TRACKING THE REFERENCE VOLTAGE
FIGURE 7. VCORE TRACKING THE REFERENCE VOLTAGE
5V
5V
5V
5V
AFTER A 1.85V TO 1.10V CHANGE COMMAND
AFTER A 1.10V TO 1.85V CHANGE COMMAND
PGOOD
VID CHANGE
VREF
11
50µs/div
50µs/div
VCORE
VCORE
VREF
VID CHANGE
PGOOD
HIP6301V, HIP6302V
HIP6301V, HIP6302V
Fault Protection
The HIP6301V and HIP6302V protect the microprocessor
and the entire power system from damaging stress levels.
Within the controller, both overvoltage and overcurrent
circuits are incorporated to protect the load and regulator.
Overvoltage
The VSEN pin is connected to the microprocessor CORE
voltage. A CORE overvoltage condition is detected when the
VSEN pin goes more than 15% above the programmed VID
level.
The overvoltage condition is latched, disabling normal PWM
operation, and causing PGOOD to go low. The latch can
only be reset by lowering and returning V
POR and Soft-Start sequence.
During a latched overvoltage, the PWM outputs will be
driven either low or three state, depending upon the VSEN
input. PWM outputs are driven low when the VSEN pin
detects that the CORE voltage is 15% above the
programmed VID level. This condition drives the PWM
outputs low, causing in the lower or MOSFETs to conduct
and shunt the CORE voltage to ground to protect the load.
If after this event, the CORE voltage falls below the over-
voltage limit (plus some hysteresis), the PWM outputs will
three state. The HIP6601 family drivers pass the three state
information along, and shuts off both upper and lower
MOSFETs. This prevents “dumping” of the output capacitors
back through the lower MOSFETs, avoiding a possibly
destructive ringing of the capacitors and output inductors. If
the conditions that caused the overvoltage still persist, the
PWM outputs will be cycled between three state and V
clamped to ground, as a hysteretic shunt regulator.
Under-Voltage
The VSEN pin also detects when the CORE voltage falls
more than 10% below the VID programmed level. This
causes PGOOD to go low, but has no other effect on
operation and is not latched. There is also hysteresis in this
detection point.
Over-Current
In the event of an over-current condition, the over-current
protection circuit reduces the average current delivered to
less than 25% of the current limit. When an over-current
condition is detected, the controller forces all PWM outputs
into a three state mode. This condition results in the gate
driver removing drive to the output stages.The controller
goes into a wait delay timing cycle that is equal to the Soft-
Start ramp time. PGOOD also goes “low” during this time
due to VSEN going below its threshold voltage.To lower the
average output dissipation, the soft-start initial wait time is
increased from 32 to 2048 cycles, then the soft-start ramp is
initiated. At a PWM frequency of 200kHz, for instance, an
overcurrent detection would cause a dead time of 10.24ms,
then a ramp of 10.08ms.
CC
high to initiate a
December 27, 2004
FN9034.2
CORE