DP83905AVQB National Semiconductor, DP83905AVQB Datasheet - Page 16
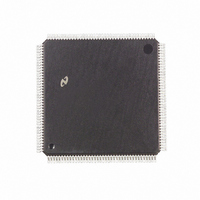
DP83905AVQB
Manufacturer Part Number
DP83905AVQB
Description
IC CONTROLR AT/LAN TP IN 160PQFP
Manufacturer
National Semiconductor
Series
AT/LANTIC™r
Datasheet
1.DP83905AVQB.pdf
(80 pages)
Specifications of DP83905AVQB
Controller Type
AT, LAN Twisted-Pair Interface Controller
Voltage - Supply
4.75 V ~ 5.25 V
Current - Supply
100mA
Operating Temperature
0°C ~ 70°C
Mounting Type
Surface Mount
Package / Case
160-BFQFP
Lead Free Status / RoHS Status
Contains lead / RoHS non-compliant
Interface
-
Other names
*DP83905AVQB
Available stocks
Company
Part Number
Manufacturer
Quantity
Price
Company:
Part Number:
DP83905AVQB
Manufacturer:
Texas Instruments
Quantity:
10 000
Part Number:
DP83905AVQB
Manufacturer:
NS/国半
Quantity:
20 000
4 0 Functional Description
at the desired base I O address If desired the configuration
software could change the EEPROM content to the new
values eliminating the need to reconfigure upon each power
up Alternately the software could leave the EEPROM alone
and execute the configuration using the printer port’s data
register upon each power up This configuration scheme will
only work once after each power-up Therefore the user
cannot enable the AT LANTIC Controller from reserved
mode change it back into reserved mode and enable it
again A power-on reset must occur between the first time it
is enabled from the reserved mode and the second
A second consideration is the location of the boot PROM in
the system memory map which also has the same conflict
and programming considerations as the I O address selec-
tion However the solution is different primarily because the
boot PROM must be configured before power up This is
because during normal usage of the boot PROM the PC’s
BIOS will look for the ROM immediately after reset not al-
lowing configuration software to first select the boot PROM
addressing prior to usage
To configure the boot PROM without jumpers the configura-
tion software must first power up the AT LANTIC Controller
configure the EEPROM to the desired location then hard-
ware reset the AT LANTIC Controller After the reset the
AT LANTIC Controller’s EEPROM will load in the desired
boot PROM configuration automatically during the reset
Now after reset when the PC scans for the boot PROM the
ROM will be correctly mapped in the memory space en-
abling the network boot operation to proceed
Ethernet Cable Configuration
AT LANTIC Controller offers the choice of all the possible
Ethernet cabling options that is Ethernet (10BASE5) Thin
Ethernet (10BASE2) and Twisted-pair Ethernet (10BASE-T)
The type of cabling used is controlled by Configuration Reg-
ister B AT LANTIC Controller also supplies a THIN output
signal which can be used to disable enable an external
DC –DC converter which is required for 10BASE2
4 5 LOW POWER OPERATION
The AT LANTIC Controller has a low power support mode
that can be used to disable the Ethernet port and conserve
power It should be noted that the device is not operational
in this mode and requires to be initialized after exiting this
mode
The power and ground pins to the AT LANTIC Controller
are split up into two groups interface and core By switching
the power off to the core logic while still powering the inter-
face logic the AT LANTIC Controller can be powered down
without crashing the ISA bus The LOWPWR pin should be
driven high to indicate that the device is about to go into low
power then the power to the V
off The same signal that is used to drive the LOWPWR pin
can be used to drive a p-channel load switch to disable
power to the core This switch must have a very low on
resistance to minimize the voltage difference between the
V
should also be powered from the V
CC
and the lFV
CC
All devices on the memory support bus
DD
pins should be switched
CC
supply
(Continued)
16
4 6 BOOT PROM OPERATION
The AT LANTIC Controller supports an optional boot
PROM the address and size of which can be set in Configu-
ration Register C This boot PROM can be any 8 bits wide
storage device implemented with a non-volatile technology
Write cycles to this device can be enabled and disabled by
programming Configuration Register B This can be used to
prevent unwanted write cycles to certain devices such as a
Flash EEPROM It should be noted that the address pins
for the boot PROM should be connected directly to the
ISA bus The AT LANTIC Controller supplies the chip se-
lect to the device and buffers the data onto and from the
ISA bus so the memory support data bus should be con-
nected to the boot PROM’s data pins
4 7 DP8390 CORE (NETWORK INTERFACE
CONTROLLER)
The DP8390 Core logic Figure 12 contains the Serializer
Deserializer which is controlled by the Protocol PLA DMA
Control FIFO Address Comparator Multicast Hashing Reg-
ister The DP8390 core implements all of the IEEE 802 3
Media access control functions for the AT LANTIC Control-
ler and interfaces to the internal ENDEC (on the left of the
block diagram) and also interfaces to the Bus Interface and
memory support bus via a number of address data and con-
trol signal (and the right side of the block diagram) The
following sections describe the functions of the DP8390
core
Receive Deserializer
The Receive Deserializer is activated when the input signal
Carrier Sense is asserted to allow incoming bits to be shift-
ed into the shift register by the receive clock The serial
receive data is also routed to the CRC generator checker
The Receive Deserializer includes a synch detector which
detects the SFD (Start of Frame Delimiter) to establish
where byte boundaries within the serial bit stream are locat-
ed After every eight receive clocks the byte wide data is
transferred to the 16-byte FlFO and the Receive Byte Count
is incremented The first six bytes after the SFD are
checked for valid comparison by the Address Recognition
Logic If the Address Recognition Logic does not recognize
the packet the FlFO is cleared
CRC Generator Checker
During transmission the CRC logic generates a local CRC
field for the transmitted bit sequence The CRC encodes all
fields after the synch byte The CRC is shifted out MSB first
following the last transmit byte During reception the CRC
logic generates a CRC field from the incoming packet This
local CRC is serially compared to the incoming CRC ap-
pended to the end of the packet by the transmitting node If
the local and received CRC match a specific pattern will be
generated and decoded to indicate no data errors Trans-
mission errors result in different patterns and are detected
resulting in rejection of a packet