MAX1957EUB+ Maxim Integrated Products, MAX1957EUB+ Datasheet - Page 15
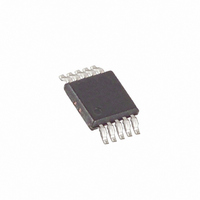
MAX1957EUB+
Manufacturer Part Number
MAX1957EUB+
Description
IC CNTRLR PWM BUCK 10-UMAX
Manufacturer
Maxim Integrated Products
Type
Step-Down (Buck)r
Datasheet
1.MAX1954EUB.pdf
(22 pages)
Specifications of MAX1957EUB+
Internal Switch(s)
No
Synchronous Rectifier
Yes
Number Of Outputs
1
Voltage - Output
0.4 ~ 4.73 V
Current - Output
3A
Frequency - Switching
300kHz
Voltage - Input
3 ~ 5.5 V
Operating Temperature
-40°C ~ 85°C
Mounting Type
Surface Mount
Package / Case
10-MSOP, Micro10™, 10-uMAX, 10-uSOP
Power - Output
444mW
Duty Cycle (max)
89 %
Output Voltage
0.4 V to 4.73 V
Output Current
3000 mA
Mounting Style
SMD/SMT
Switching Frequency
300 KHz
Maximum Operating Temperature
+ 85 C
Minimum Operating Temperature
- 40 C
Synchronous Pin
No
Topology
Boost, Buck
Lead Free Status / RoHS Status
Lead free / RoHS Compliant
Once these conditions are met, the step-down controller
enables soft-start and starts switching. The soft-start cir-
cuitry gradually ramps up to the feedback-regulation
voltage in order to control the rate-of-rise of the output
voltage and reduce input surge currents during startup.
The soft-start period is 1024 clock cycles (1024/f
MAX1954/MAX1957) or 4096 clock cycles (4096/f
MAX1953) and the internal soft-start DAC ramps the
voltage up in 64 steps. The output reaches regulation
when soft-start is completed, regardless of output
capacitance and load.
The MAX1953/MAX1954/MAX1957 feature a low-power
shutdown mode. Use an open-collector transistor to
pull COMP low to shut down the IC. During shutdown,
the output is high impedance. Shutdown reduces the
quiescent current (I
Thermal overload protection limits total power dissipation
in the MAX1953/MAX1954/MAX1957. When the junction
temperature exceeds T
sensor shuts down the device, allowing the IC to cool.
The thermal sensor turns the IC on again after the junc-
tion temperature cools by 15°C, resulting in a pulsed out-
put during continuous thermal overload conditions.
Figure 5. DH Boost Circuit
Low-Cost, High-Frequency, Current-Mode PWM
MAX1953
MAX1954
MAX1957
Thermal Overload Protection
______________________________________________________________________________________
Q
IN
) to approximately 220µA.
J
BST
= +160°C, an internal thermal
DH
DL
LX
Shutdown
S
S
,
,
To set the output voltage for the MAX1953/MAX1954,
connect FB to the center of an external resistor-divider
connected between the output to GND (Figures 1 and
2). Select R2 between 8k
late R1 by:
where V
close to the IC as possible.
For the MAX1957, connect FB directly to the output
through a decoupling resistor of 10k
3). The output voltage is then equal to the voltage at
REFIN. Again, this resistor should be placed as close to
the IC as possible.
There are several parameters that must be examined
when determining which inductor is to be used. Input
voltage, output voltage, load current, switching frequen-
cy, and LIR. LIR is the ratio of inductor current ripple to
DC load current. A higher LIR value allows for a smaller
inductor, but results in higher losses and higher output
ripple. A good compromise between size, efficiency,
and cost is an LIR of 30%. Once all of the parameters
are chosen, the inductor value is determined as follows:
where f
value close to the calculated value. The exact inductor
value is not critical and can be adjusted in order to
make trade-offs among size, cost, and efficiency. Lower
inductor values minimize size and cost, but they also
increase the output ripple and reduce the efficiency due
to higher peak currents. By contrast, higher inductor val-
ues increase efficiency, but eventually resistive losses
due to extra turns of wire exceed the benefit gained
from lower AC current levels.
For any area-restricted applications, find a low-core
loss inductor having the lowest possible DC resistance.
Ferrite cores are often the best choice, although pow-
dered iron is inexpensive and can work well at 300kHz.
S
FB
is the switching frequency. Choose a standard
L
= 0.8V. R1 and R2 should be placed as
V
Determining the Inductor Value
IN
Buck Controller
R
V
1
OUT
Setting the Output Voltage
f
S
R
2
Design Procedures
I
LOAD MAX
V
and 24k , and then calcu-
IN
V
V
OUT
FB
V
OUT
1
to 21k
LIR
(Figure
15