ISL6721 Intersil Corporation, ISL6721 Datasheet - Page 11
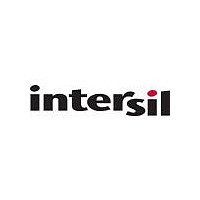
ISL6721
Manufacturer Part Number
ISL6721
Description
Flexible Single Ended Current Mode PWM Controller
Manufacturer
Intersil Corporation
Datasheet
1.ISL6721.pdf
(20 pages)
Available stocks
Company
Part Number
Manufacturer
Quantity
Price
Part Number:
ISL6721AAVZ
Manufacturer:
INTERSIL
Quantity:
20 000
Company:
Part Number:
ISL6721ABZ
Manufacturer:
Intersil
Quantity:
135
Company:
Part Number:
ISL6721ABZ
Manufacturer:
Intersil
Quantity:
500
Part Number:
ISL6721ABZ
Manufacturer:
INTERSIL
Quantity:
20 000
Part Number:
ISL6721ABZ-T
Manufacturer:
INTERSIL
Quantity:
20 000
Part Number:
ISL6721AV
Manufacturer:
INTERSIL
Quantity:
20 000
Company:
Part Number:
ISL6721AVZ
Manufacturer:
Intersil
Quantity:
500
Part Number:
ISL6721AVZ
Manufacturer:
INTERSIL
Quantity:
20 000
condition clears and the soft start voltage is below the reset
threshold, a soft start cycle begins.
Ground Plane Requirements
Careful layout is essential for satisfactory operation of the
device. A good ground plane must be employed. A unique
section of the ground plane must be designated for high di/dt
currents associated with the output stage. Power ground
(PGND) can be separated from the logic ground (LGND) and
connected at a single point. V
to PGND with good high frequency capacitors. The return
connection for input power and the bulk input capacitor
should be connected to the PGND ground plane.
Reference Design
The Typical Application Schematic features the ISL6721 in a
conventional dual output 10W discontinuous mode flyback
DC-DC converter. The ISL6721EVAL1 demonstration unit
implements this design and is available for evaluation.
The input voltage range is from 36 to 75V DC, and the two
outputs are 3.3V @ 2.5A and 1.8V @ 1.0A. Cross regulation
is achieved using the weighted sum of the two outputs.
Circuit Element Descriptions
The converter design may be broken down into the following
functional blocks:
Input Storage and Filtering Capacitance: C1, C2, C3
Isolation Transformer: T1
Primary voltage Clamp: CR6, R24, C18
Start Bias Regulator: R1, R2, R6, Q3, VR1
Operating Bias and Regulator: R25, Q2, D1, C5, CR2, D2
Main MOSFET Power Switch: Q1
Current Sense Network: R4, R3, R23, C4
Feedback Network:, R13, R15, R16, R17, R18, R19, R20,
R26, R27, C13, C14, U2, U3
Control Circuit:C7, C8, C9, C10, C11, C12, R5, R6, R8, R9,
R10, R11, R12, R14, R22
Output Rectification and Filtering: CR4, CR5, C15, C16,
C19, C20, C21, C22
Secondary Snubber: R21, C17
Design Criteria
The following design requirements were selected:
Switching Frequency, Fsw: 200kHz
Vin: 36 - 75V
Vout(1): 3.3V @ 2.5A
Vout(2): 1.8V @ 1.0A
Vout(bias): 12V @ 50mA
11
C
should be bypassed directly
ISL6721
Pout: 10W
Efficiency: 70%
Maximum Duty Cycle, Dmax: 0.45
Transformer Design
The design of a flyback transformer is a non-trivial affair. It is
an iterative process which requires a great deal of
experience to achieve the desired result. It is a process of
many compromises, and even experienced designers will
produce different designs when presented with identical
requirements. The iterative design process is not presented
here for clarity.
The abbreviated design process follows:
• Select a core geometry suitable for the application.
• Select suitable core material(s).
• Select maximum flux density desired for operation.
• Select core size. Core size will be dictated by the
• Determine maximum desired flux density. Depending on
• Determine the number of primary turns.
• Determine the turns ratio.
• Select the wire gauge for each winding.
• Determine winding order and insulation requirements.
• Verify the design.
Input Power:
Pout/Efficiency = 14.3W (use 15W)
Max On Time: Ton(max) = Dmax/Fsw = 2.25µS
Average Input Current: Iavg(in) = Pin/Vin(min) = 0.42A
Constraints of height, footprint, mounting preference, and
operating environment will affect the choice.
capability of the core structure to store the required
energy, the number of turns that have to be wound, and
the wire gauge needed. Often the window area (the space
used for the windings) and power loss determine the final
core size. For flyback transformers, the ability to store
energy is the critical factor in determining the core size.
The cross sectional area of the core and the length of the
air gap in the magnetic path determine the energy storage
capability.
the frequency of operation, the core material selected, and
the operating environment, the allowed flux density must
be determined. The decision of what flux density to allow
is often difficult to determine initially. Usually the highest
flux density that produces an acceptable design is used,
but often the winding geometry dictates a larger core than
is required based on flux density and energy storage
calculations.