ADIS16407BMLZ Analog Devices Inc, ADIS16407BMLZ Datasheet - Page 21
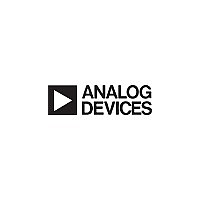
ADIS16407BMLZ
Manufacturer Part Number
ADIS16407BMLZ
Description
10 DoF IMU (with Pressure Sensor)
Manufacturer
Analog Devices Inc
Series
iSensor™r
Specifications of ADIS16407BMLZ
Output Type
Digital
Sensor Type
Gyroscope, 3 Axis
No. Of Axes
3
Ic Interface Type
Serial
Sensor Case Style
ML-24-2
No. Of Pins
24
Supply Voltage Range
4.75V To 5.25V
Operating Temperature Range
-40°C To +105°C
Lead Free Status / Rohs Status
Lead free / RoHS Compliant
Hard Iron Factors
When the hard iron error estimation is complete, take the
following steps:
1.
2.
3.
Soft Iron Effects
The XMAGN_SIC (Table 58), YMAGN_SIC (Table 59), and
ZMAGN_SIC (Table 60) registers provide an adjustment
variable for the magnetometer sensitivity adjustment in each
magnetometer response to simplify the process of performing a
system level soft iron correction.
Table 58. XMAGN_SIC (Base Address = 0x30), Read/Write
Bits
[15:12]
[11:0]
Table 59. YMAGN_SIC (Base Address = 0x32), Read/Write
Bits
[15:12]
[11:0]
Table 60. ZMAGN_SIC (Base Address = 0x34), Read/Write
Bits
[15:12]
[11:0]
Multiply the estimate by −1 to change its polarity.
Convert it into digital format for the hard iron correction
registers (Table 55).
Write the correction factors to the correction registers. For
example, lower the x-axis bias by 10 LSB (5 mgauss) by
setting XMAGN_HIC = 0x1FF6 (DIN = 0xAB1F, 0xAAF6).
Description (Default = 0x0800)
Not used
X-axis soft iron correction factor, binary format,
Scale factor = 100%/2048LSB, 0x000 = 0
Example: 0x800 = 100% (factory scale unchanged)
Maximum = 0xFFF = 200% − 100%/2048
Description (Default = 0x0800)
Not used
Y-axis soft iron correction factor, binary format,
Scale factor = 100%/2048LSB, 0x000 = 0
Example: 0x800 = 100% (factory scale unchanged)
Maximum = 0xFFF = 200% − 100%/2048
Description (Default = 0x0800)
Not used
Z-axis soft iron correction factor, binary format,
Scale factor = 100%/2048LSB, 0x000 = 0
Example: 0x800 = 100% (factory scale unchanged)
Maximum = 0xFFF = 200% − 100%/2048
Rev. B | Page 21 of 24
Soft Iron Factors
When the soft iron error estimation is complete, convert the
sensitivity into the digital format for the soft iron correction
registers (Table 58) and write the correction factors to the
correction registers. A simple method for converting the
correction factor is to divide it by 2 and multiply it by 4095. For
example, increasing the default soft iron factor to approximately
1.15 uses a binary code for 2355, or 0x933. Increase the soft iron
correction factor for the y-axis to approximately 1.15 by setting
YMAGN_SIC = 0x0933 (DIN = 0xB309, 0xB233).
FLASH UPDATES
When using the user calibration registers to optimize system
level accuracy, keep in mind that the register values are volatile
until their contents are saved in the nonvolatile flash memory.
After writing all of the correction factors into the user correction
registers, set GLOB_CMD[3] = 1 (DIN = 0xC204) to save these
settings in nonvolatile flash memory. Be sure to consider the
endurance rating of the flash memory when determining how
often to update the user correction factors in the flash memory.
RESTORING FACTORY CALIBRATION
Set GLOB_CMD[1] = 1 (DIN = 0xC202) to execute the factory
calibration restore function. This is a single command function,
which resets the gyroscope and accelerometer offset registers to
0x0000 and all sensor data to 0. Then, it automatically updates the
flash memory within 75 ms and restarts sampling and processing
data. See Table 32 for more information on GLOB_CMD.
ADIS16407