AT-GM-11KM BANNER ENGINEERING, AT-GM-11KM Datasheet - Page 5
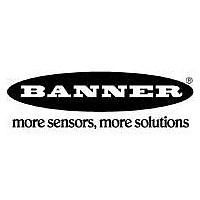
AT-GM-11KM
Manufacturer Part Number
AT-GM-11KM
Description
AT-GM-11KM TWO-HAND CTL W/MUTI
Manufacturer
BANNER ENGINEERING
Datasheet
1.AT-GM-11KM.pdf
(16 pages)
DUO-TOUCH
Figure 3. Hook-up of two pairs of mute
Figure 4. Solid-state output hook-up
If two pairs of mute sensors are required, parallel
the output (hard) contacts of M1 and M3, and M2
and M4, as shown above.
Two independent position switches
(at M1-M2) must be properly adjusted or
positioned so they close only after the
hazard no longer exists and open when the
cycle is complete or the hazard is again
present. If improperly adjusted or
positioned, injury or death could result.
The user has the responsibility to satisfy all
local, state, and national laws, rules codes,
and regulations relating to the use of safety
equipment in any application. It is extremely
important to be sure that all appropriate
agency requirements have been met and that
all installation and maintenance instructions
contained in the appropriate manuals are
followed.
If solid-state output mute devices are required,
use only devices with a discrete output, as
shown above. Two-wire sensors should not be
used due to the possibility of excessive leakage
current causing a false ON condition.
!
Banner Engineering Corp.
devices
24V dc
www.bannerengineering.com • Tel: 763.544.3164
0V dc
WARNING ...
Avoid Hazardous
Installations
+
+
–
–
M1
M2
®
M3
M1
M4
M2
SG –
NPN
PNP
•
M11
M12
M21
M22
Minneapolis MN, U.S.A.
B2
Models AT-GM-11KM and AT-HM-11KM Two-Hand Control Modules
Muting Device Requirements
The muting devices (typically sensors or switches) must, at a minimum, comply with
the following requirements:
• A minimum of two independent hard-wired muting devices must be used. If the
• The muting devices either must both have normally open contacts, or one device
• The activation of the inputs to the muting module must be from separate sources.
• The devices must be installed so they can not be easily defeated or bypassed.
• The devices must be mounted so their physical position and alignment cannot
• It must not be possible for environmental conditions (such as extreme airborne
• The muting sensors or switches must not be set to use any delay or other timing
Examples of Muting Sensors and Switches
Photoelectric Sensors (Opposed Mode):
Opposed-mode sensors, which initiate the muted condition when the beam path is
blocked, should be configured for Dark Operate and have open (non-conducting) output
contacts in a power OFF condition.
Photoelectric Sensors (Polarized Retroreflective Mode):
The user must ensure that false “proxing” (activation due to shiny or reflective surfaces)
is not possible. Banner “LP” sensors with linear polarization can greatly reduce or
eliminate this effect.
Configure sensors for Light Operate (LO or N.O.) if initiating a mute when the
retroreflective target or tape is detected (e.g., home position). Configure sensors for Dark
Operate (DO or N.C.) when a blocked beam path initiates the muted condition (e.g.,
entry/exit). Both situations must have open (non-conducting) output contacts in a power
OFF condition.
Positive-Opening Safety Switches:
Two or four independent switches, each with a minimum of one closed safety contact to
initiate the mute cycle are typically used. An application using a single switch with a
single actuator and two closed contacts could result in an unsafe situation.
Inductive Proximity Sensors:
Typically used to initiate a muted cycle when a metal surface is detected. Due to the
possibility of excessive leakage current causing false ON conditions, two-wire sensors
are not to be used. Only three- or four-wire sensors that have discrete PNP, NPN, or
hard-contact outputs separate from the input power can be used.
sources disagree or conflict, the mute must end or must not occur. No one source
can initiate or continue a muted condition.
have a PNP output and one device have an NPN output. These contacts must
“close” when the switch is actuated (to initiate a mute cycle), and “open” when the
switch is not actuated (to end a mute cycle) and in a power off condition.
These sources must be mounted separately in order to prevent misadjustment or a
single common mode failure resulting in an unintended muting condition. For
example, this condition could cause physical damage to the mounting surface,
causing both muting devices to be knocked out of alignment, resulting in false
“muting” signals. Only one of these sources may pass through, or be affected by, a
programmable logic controller or similar device.
change.
contamination) to initiate a mute condition.
functions (unless accomplished in such a manner that does not lessen the level of
safety integrity of the system and does not create a hazard by extending the mute
cycle).
P/N 109782
5