ncp5424adr2 ON Semiconductor, ncp5424adr2 Datasheet - Page 10
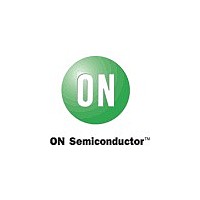
ncp5424adr2
Manufacturer Part Number
ncp5424adr2
Description
Dual Synchronous Buck Controller With Input Current Sharing
Manufacturer
ON Semiconductor
Datasheet
1.NCP5424ADR2.pdf
(18 pages)
Definition of the design specifications
of the following:
consider all of the above effects and provide an output
voltage that will meet the specified tolerance at the load.
component temperatures are kept within the manufacturer’s
specified ratings at full load and maximum ambient
temperature.
Selecting Feedback Divider Resistors
amplifier is referenced to 1.0 V and the output voltage is
determined by selecting resistor divider values. Resistor R1
is selected based on a design trade−off between efficiency
and output voltage accuracy. The output voltage error can be
estimated due to the bias current of the error amplifier
neglecting resistor tolerance:
Calculating Duty Cycle
losses) is given by the formula:
where:
The output voltage tolerance can be affected by any or all
Budgeting the tolerance is left to the designer who must
The designer must also ensure that the regulator
The feedback pins (V
resistor dividers to set the output voltages. The error
R2 can be sized after R1 has been determined:
The duty cycle of a buck converter (including parasitic
1. buck regulator output voltage setpoint accuracy;
2. output voltage change due to discharging or charging
3. output voltage change due to the ESR and ESL of the
4. output voltage ripple and noise.
Duty Cycle + D +
V
V
Figure 7. Selecting Feedback Divider Resistors
OUT
HFET
of the bulk decoupling capacitors during a load
current transient;
bulk and high frequency decoupling capacitors,
circuit traces, and vias;
= buck regulator output voltage;
Error% + 1
= high side FET voltage drop due to R
DESIGN GUIDELINES
R2 + R1
V
OUT
V IN ) V LFET * V HFET * V L
FB1(2)
R1
R2
10 *6
V OUT ) (V HFET ) V L )
V OUT
1
1
) are connected to external
V
* 1
FB
R1
100%
DS(ON)
http://onsemi.com
NCP5424
;
10
Selecting the Switching Frequency
component size and power losses. Operation at higher
switching frequencies allows the use of smaller inductor and
capacitor values. Nevertheless, it is common to select lower
frequency operation because a higher frequency results in
lower efficiency due to MOSFET gate charge losses.
Additionally, the use of smaller inductors at higher
frequencies results in higher ripple current, higher output
voltage ripple, and lower efficiency at light load currents.
linearly related to the switching period. If the designer
prefers not to use Figure 8 to select the necessary resistor, the
following equation quite accurately predicts the proper
resistance for room temperature conditions.
where:
Selection of the Output Inductor
current capability, and DC resistance. Increasing the
inductor value will decrease output voltage ripple, but
degrade transient response. There are many factors to
consider in selecting the inductor including cost, efficiency,
EMI and ease of manufacture. The inductor must be able to
handle the peak current at the switching frequency without
saturating, and the copper resistance in the winding should
be kept as low as possible to minimize resistive power loss.
cores that could be used for this application. Among them
are ferrites, molypermalloy cores (MPP), amorphous and
powdered iron cores. Powdered iron cores are very
Selecting the switching frequency is a trade−off between
The value of the oscillator resistor is designed to be
The inductor should be selected based on its inductance,
There are a variety of materials and types of magnetic
800
700
600
500
400
300
200
100
V
V
V
R
f
SW
10
OSC
L
IN
LFET
= output inductor voltage drop due to inductor wire
= buck regulator input voltage;
= switching frequency in kHz.
DC resistance;
= oscillator resistor in kW;
= low side FET voltage drop due to R
Figure 8. Switching Frequency
20
R OSC +
30
21700 * f SW
R
OSC (kW)
2.31f SW
40
50
DS(ON)
60
.