NCV3020BDR2G ON Semiconductor, NCV3020BDR2G Datasheet - Page 16
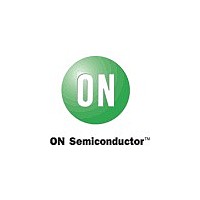
NCV3020BDR2G
Manufacturer Part Number
NCV3020BDR2G
Description
IC PWM CTLR SYNC 8SOIC
Manufacturer
ON Semiconductor
Series
-r
Datasheet
1.NCP3020BDR2G.pdf
(23 pages)
Specifications of NCV3020BDR2G
Pwm Type
Voltage Mode
Number Of Outputs
1
Frequency - Max
670kHz
Duty Cycle
80%
Voltage - Supply
4.7 V ~ 28 V
Buck
Yes
Boost
No
Flyback
No
Inverting
No
Doubler
No
Divider
No
Cuk
No
Isolated
No
Operating Temperature
-40°C ~ 125°C
Package / Case
8-SOIC (0.154", 3.90mm Width)
Lead Free Status / Rohs Status
Lead free / RoHS Compliant
Available stocks
Company
Part Number
Manufacturer
Quantity
Price
Part Number:
NCV3020BDR2G
Manufacturer:
ON/安森美
Quantity:
20 000
Inductor Selection
input and output requirements. Some example conditions
are listed below to assist in the process.
are LC filtered to produce a lower dc output voltage (V
The output voltage can be changed by modifying the on time
relative to the switching period (T) or switching frequency.
The ratio of high side switch on time to the switching period
is called duty cycle (D). Duty cycle can also be calculated
using V
and the High side switch voltage drop V
Table 1. DESIGN PARAMETERS
Input Voltage
Nominal Input Voltage
Output Voltage
Input ripple voltage
Output ripple voltage
Output current rating
Operating frequency
When selecting the inductor, it is important to know the
A buck converter produces input voltage (V
OUT
Design Parameter
, V
IN
, the low side switch voltage drop V
D +
T
(VOUT
T
ON
(VIN
F +
(* D +
18
16
14
12
10
RIPPLE
RIPPLE
(V
8
6
4
2
0
4.5
(I
(Fsw)
1
T
(V
(V
OUT
OUT
IN
IN
Voltage Ripple
Maximum Allowable Voltage
Maximum Boost Voltage
)
)
)
)
)
)
6.5
T
Figure 31. Boost Voltage at 80% Duty Cycle
OFF
T
HSD
Example Value
8.5
9 V to 18 V
.
IN
300 kHz
300 mV
50 mV
3.3 V
12 V
10 A
) pulses that
10.5
(eq. 3)
(eq. 4)
http://onsemi.com
12.5
OUT
LSD
).
Input Voltage (V)
14.5
,
Boost Voltage
16
16.5
simplifies the equations used for inductor selection. The
formula for this is given in Equation 6.
percentage of ripple current in the inductor lies between
10% and 40%. When using ceramic output capacitors the
ripple current can be greater thus a user might select a higher
ripple current, but when using electrolytic capacitors a lower
ripple current will result in lower output ripple. Now,
acceptable values of inductance for a design can be
calculated using Equation 7.
is shown in Figure 32.
The ratio of ripple current to maximum output current
The designer should employ a rule of thumb where the
The relationship between ra and L for this design example
18.5
D +
L +
+
20.5
³ 27.5% +
10 A @ 24% @ 300 kHz
I
V
OUT
IN
22.5
V
* V
@ ra @ F
V
OUT
OUT
ra +
24.5
3.3 V
HSD
) V
3.3 V
12 V
SW
26.5
) V
I
OUT
LSD
DI
@ ( 1 * D ) ³ 3.3 mH
LSD
[ D +
@ ( 1 * 27.5% )
V
V
OUT
IN
(eq. 5)
(eq. 6)
(eq. 7)