HIP4082EVAL Intersil, HIP4082EVAL Datasheet - Page 4
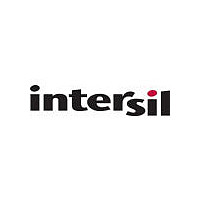
HIP4082EVAL
Manufacturer Part Number
HIP4082EVAL
Description
EVAL BOARD FET DRIVER HIP4082
Manufacturer
Intersil
Type
FET Driverr
Datasheet
1.HIP4082EVAL.pdf
(13 pages)
Specifications of HIP4082EVAL
Contents
Fully Assembled Evaluation Board
For Use With/related Products
HIP4082
Lead Free Status / RoHS Status
Contains lead / RoHS non-compliant
with the additional trace impedances in the bootstrap
charging loop will not allow 24A to flow. Often the customer’s
power supply used for biasing the driver and control logic is
incapable of supplying this magnitude of current. For this
reason, much larger bypass capacitors are recommended
for the V
capacitors. A good rule of thumb is ten times greater. In the
example above, if the bootstrap circuit impedance is
estimated to be about 5Ω, then the peak current will be only
2.4A. The time required to charge up the bootstrap capacitor
(an exponential charge characteristic is assumed) to just
under 11V will be approximately 12µs. (24 times the charge
time allotted by default within the IC!) To avoid problems
when driving large MOSFETs or when paralleling MOSFETs
it is necessary to consider the low voltage bias supply’s
output impedance, the bias supply’s bypass capacitor
(located at the HIP4082 IC), the size of the bootstrap
capacitor (it should also be about 10 times the equivalent
input capacitance of the connected MOSFETs), and the
forward resistance characteristic of the chosen bootstrap
diode.
Transformer Specification
Current Product-to-Market needs often require having a
magnetics supplier design the magnetics devices in your
design. We followed this approach with respect to the eval-
board’s transformer and choke. The electronics designer
provides a detailed specification to the transformer supplier.
The specification should include the minimum frequency of
operation, the maximum applied voltage and waveform, the
continuous and overload current profiles, and operating
ambient temperature. Required transformer regulation must
also be specified. The transformer designer needs to know
this in order to size the transformer wire and leakage
inductance. The power handling capability and operating
frequency influences choice of core size and geometry and
ultimately the cost and size of the transformer. (Refer to the
Bill of Material included in the Appendix for information
regarding the transformer.)
It is important that the transformer designer have knowledge
of the transformer excitation waveform. The reason that this
is important is that the current waveshape dictates the form
factor or the value of RMS (root-mean-square) current that
will result for a given required average current. The size of
the filter capacitor, the equivalent series impedance of the
secondary, and the output voltage waveshape will determine
the current waveform and form factor. The RMS current
determines the power losses in the transformer and
temperature rise. To minimize ringing on the inverter bridge
of the primary inverter it will help to minimize the leakage
inductance of the transformer. For the DC-to-AC inverter
eval-board, power ferrite material, E core style PQ3230, was
used for the core.
CC
supply than are used for the bootstrap
4
Application Note 9611
In order to minimize transformer size and maximize winding
fill, the primary was formed of 3 separate windings which were
paralleled to supply the approximately 30A
rated output power. Each primary winding’s DC resistance is
less than 10mΩ. There are two equal, but separate,
secondary power output windings. When series-connected,
these secondary power output windings provide 230V
power. The US configured eval-boards are provided with
paralleled output windings for 115V
connection via soldered jumper wires allows for 230V
operation, but this shouldn’t be attempted without changing
the power MOSFETs and the voltage ratings of several
capacitors. A 500V MOSFET with an r
the Intersil IRF830R would be a suitable device for 230V
operation. Besides having to double the capacitor voltage
ratings of C
have to be dropped by a factor of 4. This maintains the power
dissipation in resistors, R
the 115V
A third secondary winding provides low voltage control
power to all of the secondary-side inverter logic and gate
drivers. This voltage is nominally 20.5V (peak of the square-
wave) when there is a nominal 13.6V
battery input terminals of the eval-board. This winding must
output at least 14V at the minimum battery voltage in order
to keep the series regulator out of saturation. This winding
carries less than 100mA, so winding gauge will be
determined more for strength than for current carrying
capacity.
Secondary Inverter Design
The secondary-side inverter and control is designed to
provide a near constant 115V
voltage waveform. The inverter can supply approximately
120W to loads such as small fans, lights, radios and other
small electric appliances that might be handy to have with
you on a camping trip, for example.
In addition, a simple current trip circuit and an overtemp
limiter was incorporated in order to provide features similar
to a commercially available DC-to-AC inverter of similar
rating and purpose.
The secondary-side inverter includes the following functions:
• A high voltage input rectifier and filter
• A high voltage DC-to-AC inverter and control circuits,
• A neon lamp to warn of the presence of high voltage and
Input Filter and Rectifiers
There are two full wave rectifiers. One rectifies the 162V
secondary voltage to provide the DC high voltage bus for the
providing over-current, thermal protection, and output
voltage regulation to compensate for widely varying
battery voltages and output current;
ELECTRICAL SHOCK HAZARD. Details of these circuits
follow.
AC
23
design.
, C
27
and C
34
13
, the capacity of C
and R
AC
to 120V
38
AC
to remain as they are for
DS(ON)
DC
operation. Series
AC
applied to the
RMS
, 55Hz output
of 1.5Ω such as
23
required at
and C
AC
AC
27
AC
load
will