Z8FMC160100KIT Zilog, Z8FMC160100KIT Datasheet - Page 3
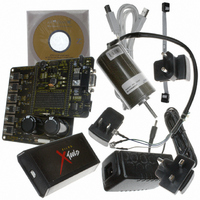
Z8FMC160100KIT
Manufacturer Part Number
Z8FMC160100KIT
Description
KIT DEV FOR Z8 ENCORE Z8FMC16100
Manufacturer
Zilog
Series
Z8 Encore! MC™r
Datasheets
1.Z8FMC160100KIT.pdf
(7 pages)
2.Z8FMC160100KIT.pdf
(383 pages)
3.Z8FMC160100KIT.pdf
(20 pages)
Specifications of Z8FMC160100KIT
Main Purpose
Power Management, Motor Control
Embedded
Yes, MCU, 8-Bit
Utilized Ic / Part
Z8FMC16100
Primary Attributes
3-Ph DC Motors
Secondary Attributes
Graphic User Interface
Processor To Be Evaluated
Z8FMC16100
Data Bus Width
8 bit
Interface Type
USB
For Use With
269-4664 - KIT ACC OPTO-ISO USB SMART CABLE269-4661 - KIT ACC ETHERNET SMART CABLE269-4539 - KIT ACCESSORY USB SMART CABLE
Lead Free Status / RoHS Status
Contains lead / RoHS non-compliant
Other names
269-3639
•
Furthermore, two voltage application techniques can be applied, based on the configuration of the supply-to-
motor windings:
•
•
In this application, sensorless control with a trapezoidal waveform is implemented. This implementation is
very common in small BLDC motors used in many White Goods and other consumer-based products.
The block diagram of the BLDC motor control system is shown in
Z8FMC16100. In a 3-Phase commutation arrangement, at any given instance, only two phases are energized.
The back EMF voltage is in turn generated in the unenergized phase winding, and the zero crossing of this
induced voltage is detected for synchronization of the subsequent closed-loop control events. As discussed
later, the innovative Time Stamp feature of the Z8FMC16100 MCU provides for robust, efficient
implementation of this critical sensing function without the requirement for an additional comparator.
AN022602-0810
additional hardware for sensor interface.
Sensorless commutation–In the sensorless commutation technique, the back-EMF induced in the idle
phase is used to determine the moment of commutation. When the induced idle-phase back-EMF equals
one-half of the DC bus voltage, commutation is complete.
The advantage of sensorless commutation is that it makes the hardware design simpler. No sensors or
associated interface circuitry are required. The disadvantages are that it requires a relatively complex
control algorithm, and, when the magnitude of induced back-EMF is low, it does not support low motor
speeds.
Sinusoidal–Sinusoidal voltage is applied to the three-phase winding. Sinusoidal voltage provides a smooth
motor rotation and fewer ripples.
Trapezoidal–Here DC is applied to two phases at a time, and the third phase is left idle. Trapezoidal
voltage is simpler to implement and less complex.
Sensorless Brushless DC Motor Control with Z8 Encore! MC
Figure 1
on page 4 and is based on
TM
Microcontrollers