HCPL-M454#500 Avago Technologies US Inc., HCPL-M454#500 Datasheet - Page 11
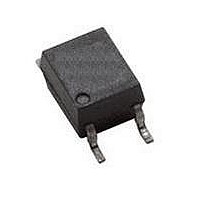
HCPL-M454#500
Manufacturer Part Number
HCPL-M454#500
Description
OPTOCOUPLER 1MBS TTL/IPM SO-5
Manufacturer
Avago Technologies US Inc.
Datasheet
1.HCPL-M454500.pdf
(12 pages)
Specifications of HCPL-M454#500
Input Type
DC
Package / Case
5-SOP
Number Of Channels
1
Voltage - Isolation
3750Vrms
Current Transfer Ratio (min)
25% @ 16mA
Current Transfer Ratio (max)
60% @ 16mA
Voltage - Output
20V
Current - Output / Channel
8mA
Current - Dc Forward (if)
25mA
Output Type
Transistor with Vcc
Mounting Type
Surface Mount
Isolation Voltage
3750 Vrms
Output Device
Phototransistor
Configuration
1 Channel
Current Transfer Ratio
65 %
Maximum Baud Rate
1 MBps
Maximum Forward Diode Voltage
1.7 V
Maximum Reverse Diode Voltage
5 V
Maximum Input Diode Current
25 mA
Maximum Power Dissipation
100 mW
Maximum Operating Temperature
+ 70 C
Minimum Operating Temperature
0 C
Lead Free Status / RoHS Status
Contains lead / RoHS non-compliant
Vce Saturation (max)
-
Lead Free Status / RoHS Status
Lead free / RoHS Compliant, Contains lead / RoHS non-compliant
Available stocks
Company
Part Number
Manufacturer
Quantity
Price
Power Inverter Dead Time and Propagation Delay Specifica-
tions
The HCPL-M454 includes a specification intended to help
designers minimize “dead time” in their power inverter
designs. The new “propagation delay difference” specifi-
cation (t
much optocoupler switching delay is needed to prevent
“shoot-through” current, but also for determining the
best achievable wort-case dead time for a given design.
When inverter power transistors switch (Q1 and Q2 in
Figure 15), it is essential that they never conduct at the
same time. Extremely large currents will flow if there is
any overlap in their conduction during switching transi-
tions, potentially damaging the transistor and even the
surrounding circuitry. This “shoot-through” current is
eliminated by delaying the turn-on of one transistor (Q2)
long enough to ensure that the opposing transistor (Q1)
has completely turned off. This delay introduces a small
amount of “dead time” at the output of the inverter dur-
ing which both transistors are off during switching tran-
sitions. Minimizing this dead time is an important design
goal for an inverter designer.
The amount of turn-on delay needed depends on the
propagation delay characteristics of the optocoupler,
as well as the characteristics of the transistor base/gate
drive circuit. Considering only the delay characteristics
of the optocoupler (the characteristics of the base/gate
drive circuit can be analyzed in the same way), it is im-
portant to know the minimum and maximum turn-on
(t
tions, preferably over the desired operating temperature
range. The importance of these specifications is illustrat-
ed in Figure 16. The waveforms labeled “LED1”, “LED2”,
“OUT1”, and “OUT2” are the input and output voltages
of the optocoupler circuits driving Q1 and Q2 respec-
tively. Most inverters are designed such that the power
transistor turns on when the optocoupler LED turns on;
this ensures that both power transistors will be off in the
event of a power loss in the control circuit. Inverters can
also be designed such that the power transistor turns off
when the optocoupler LED turns on; this type of design,
however, requires additional fail-safe circuitry to turn off
the power transistor if an over-current condition is de-
tected. The timing illustrated in Figure 16 assumes that
the power transistor turns on when the optocoupler LED
turns on.
The LED signal to turn on Q2 should be delayed enough
so that an optocoupler with the very fastest turn-on
propagation delay (t
PHL
) and turn-off (t
PLH
- t
PHL
) is useful for determining not only how
PHLmin
PLH
) propagation delay specifica-
) will never turn on before
an optocoupler with the very slowest turn-off propaga-
tion delay (t
of the optocoupler should be delayed by an amount no
less than (t
maximum data sheet value for the propagation delay dif-
ference specification, (t
fies a maximum (t
temperature range of 0-70°C.
Although (t
delay is needed to prevent shoot-through current, it is
insufficient to tell the designer how much dead time a
design will have. Assuming that the optocoupler turn-
on delay is exactly equal to (t
dead time is zero (i.e., there is zero time between the
turn-off of the very slowest optocoupler and the turn-on
of the very fastest optocoupler).
Calculating the maximum dead time is slightly more
complicated. Assuming that the LED turn-on delay is still
exactly equal to (t
that the maximum dead time is the sum of the maximum
difference in turn-on delay plus the maximum difference
in turn-off delay,
[(t
This expression can be rearranged to obtain
[(t
and further rearranged to obtain
[(t
which is the maximum minus the minimum data sheet
values of (t
mum and minimum values depends directly on the to-
tal spread of propagation delays and sets the limit on
how good the worst-case dead time can be for a given
design. Therefore, optocouplers with tight propagation
delay specifications (and not just shorter delays or lower
pulse-width distortion) can achieve short dead times in
power inverters. The HCPL-M454 specifies a minimum
(t
range of 0-70°C, resulting in a maximum dead time of 2.0
µs when the LED turn-on delay is equal to (t
or 1.3 µs.
It is important to maintain accurate LED turn-on delays
because delays shorter than (t
shoot-through currents, while longer delays will increase
the worst-case dead time.
PLH
PLHmax
PLHmax
PLH
- t
-t
PHL
PHL
-t
-t
)
PLHmin
PHLmin
max
) of -0.7 µs over an operating temeprature
PLHmax
PLH
PLH
PLHmax
- (t
- t
- t
) + (t
) - (t
PLH
PHL
- t
PLH
PHL
) turns off. To ensure this, the turn-on
PLH
PHLmin
PHLmin
-t
). The difference between the maxi-
PHLmax
- t
)
PHL
- t
max
PHL
PLH
PHL
)
min
), which also happens to be the
-t
)
tells the designer how much
max
-t
- t
) of 1.3 µs over an operating
PHLmax
],
PHLmin
PHL
PLH
, it can be seen in Figure 16
PLH
). The HCPL-M454 speci-
- t
)],
)],
PHL
- t
)
PHL
max
)
, the minimum
max
PLH
may allow
- t
PHL
)
max
,