MAX8792ETD+T Maxim Integrated Products, MAX8792ETD+T Datasheet - Page 14
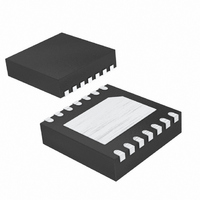
MAX8792ETD+T
Manufacturer Part Number
MAX8792ETD+T
Description
IC PWM CONTROLLER 14TDFN
Manufacturer
Maxim Integrated Products
Datasheet
1.MAX8792ETDT.pdf
(29 pages)
Specifications of MAX8792ETD+T
Applications
PWM Controller
Voltage - Input
2 ~ 26 V
Current - Supply
700µA
Operating Temperature
-40°C ~ 80°C
Mounting Type
Surface Mount
Package / Case
14-TDFN Exposed Pad
Lead Free Status / RoHS Status
Lead free / RoHS Compliant
Voltage - Supply
-
Lead Free Status / Rohs Status
Lead free / RoHS Compliant
input voltage and directly proportional to output volt-
age. Another one-shot sets a minimum off-time (200ns
typ). The on-time one-shot is triggered if the error com-
parator is low, the low-side switch current is below the
valley current-limit threshold, and the minimum off-time
one-shot has timed out.
The heart of the PWM core is the one-shot that sets the
high-side switch on-time. This fast, low-jitter, adjustable
one-shot includes circuitry that varies the on-time in
response to input and output voltage. The high-side
switch on-time is inversely proportional to the input volt-
age as sensed by the TON input, and proportional to
the feedback voltage as sensed by the FB input:
where T
(R
a nearly constant switching frequency despite the lack
of a fixed-frequency clock generator. Connect a resis-
tor (R
period T
where C
back (V
to switching periods of 167ns (600kHz) to 500ns
(200kHz), respectively. High-frequency (600kHz) opera-
tion optimizes the application for the smallest compo-
nent size, trading off efficiency due to higher switching
losses. This may be acceptable in ultra-portable devices
where the load currents are lower and the controller is
powered from a lower voltage supply. Low-frequency
(200kHz) operation offers the best overall efficiency at
the expense of component size and board space.
For continuous conduction operation, the actual switching
frequency can be estimated by:
where V
in the inductor discharge path, including synchronous
rectifier, inductor, and PC board (PCB) resistances;
V
path, including the high-side switch, inductor, and PCB
resistances; and t
MAX8792.
Single Quick-PWM Step-Down
Controller with Dynamic REFIN
14
DROP2
TON
______________________________________________________________________________________
TON
) between TON and V
OUT
TON
DROP1
SW
SW
is the sum of the resistances in the charging
) between TON and V
T
SW
On-Time (t
= 1 / f
(switching period) is set by the resistance
= V
= 16.26pF. When used with unity-gain feed-
=
is the sum of the parasitic voltage drops
FB
f
SW
C
SW
), a 96.75kΩ to 303.25kΩ corresponds
TON
ON
=
:
t
ON
ON IN
is the on-time calculated by the
(
R
V
TON
) = T
FB
(
V
+
IN
+
+
SW
V
. This algorithm results in
6 5 . Ω
DROP
V
DROP
IN
(V
k
FB
to set the switching
On-Time One-Shot
1
)
⎛
⎜
⎝
2
/ V
V
)
V
OUT
FB
IN
)
⎞
⎟
⎠
The MAX8792 is enabled when EN is driven high and
the 5V bias supply (V
powers up first. Once the reference exceeds its UVLO
threshold, the internal analog blocks are turned on and
masked by a 50µs one-shot delay in order to allow the
bias circuitry and analog blocks enough time to settle
to their proper states. With the control circuitry reliably
powered up, the PWM controller may begin switching.
Power-on reset (POR) occurs when V
approximately 3V, resetting the fault latch and prepar-
ing the controller for operation. The V
inhibits switching until V
troller powers up the reference once the system
enables the controller, V
driven high. With the reference in regulation, the con-
troller ramps the output voltage to the target REFIN volt-
age with a 1mV/µs slew rate:
The soft-start circuitry does not use a variable current
limit, so full output current is available immediately.
PGOOD becomes high impedance approximately
200µs after the target REFIN voltage has been reached.
The MAX8792 automatically uses pulse-skipping mode
during soft-start and uses forced-PWM mode during
soft-shutdown, regardless of the SKIP configuration.
For automatic startup, the battery voltage should be
present before V
the output into regulation without the battery voltage
present, the fault latch trips. The controller remains shut
down until the fault latch is cleared by toggling EN or
cycling the V
If the V
assumes that there is not enough supply voltage to
make valid decisions. To protect the output from over-
voltage faults, the controller shuts down immediately
and forces a high-impedance output (DL and DH
pulled low).
When the system pulls EN low, the MAX8792 enters
low-power shutdown mode. PGOOD is pulled low
immediately, and the output voltage ramps down with a
1mV/µs slew rate:
CC
voltage drops below 4.25V, the controller
Power-Up Sequence (POR, UVLO)
CC
t
t
START
SHDN
power supply below 0.5V.
CC
. If the controller attempts to bring
=
=
DD
1
1
CC
mV
mV
CC
V
V
) is present. The reference
FB
FB
rises above 4.25V. The con-
/
/
exceeds 4.25V, and EN is
μ
μ
s
s
=
=
1
1
V ms
V ms
V
V
FB
/
FB
/
CC
CC
UVLO circuitry
Shutdown
rises above