EVAL-ADXL312Z Analog Devices, EVAL-ADXL312Z Datasheet - Page 26
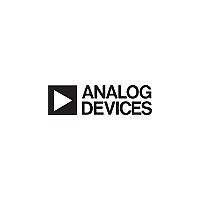
EVAL-ADXL312Z
Manufacturer Part Number
EVAL-ADXL312Z
Description
Daughter Cards & OEM Boards EB Digital Output Three-Axis Accel
Manufacturer
Analog Devices
Series
ADXL312r
Datasheet
1.EVAL-ADXL312Z.pdf
(32 pages)
Specifications of EVAL-ADXL312Z
Rohs
yes
Product
Evaluation Boards
Description/function
3 axis accelerometer evaluation board
Interface Type
I2C, SPI
Maximum Operating Temperature
+ 105 C
Minimum Operating Temperature
- 40 C
Operating Supply Voltage
2 V to 3.6 V
Factory Pack Quantity
1
For Use With
ADXL312
ADXL312
USING SELF-TEST
The self-test change is defined as the difference between the
acceleration output of an axis with self-test enabled and the
acceleration output of the same axis with self-test disabled (see
Endnote 4 of Table 1). This definition assumes that the sensor
does not move between these two measurements because, if the
sensor moves, a non-self-test related shift corrupts the test.
Proper configuration of the ADXL312 is also necessary for an
accurate self-test measurement. The part should be set with a
data rate greater than or equal to 100 Hz. This is done by
ensuring that a value greater than or equal to 0x0A is written
into the rate bits (Bit D3 through Bit D0) in the BW_RATE
register (Address 0x2C). The part also must be placed into
normal power operation by ensuring the LOW_POWER bit in
the BW_RATE register is cleared (LOW_POWER bit = 0) for
accurate self-test measurements. It is recommended that the
part be set to full-resolution, 12 g mode to ensure that there is
sufficient dynamic range for the entire self-test shift. This is done
by setting Bit D3 of the DATA_FORMAT register (Address 0x31)
and writing a value of 0x03 to the range bits (Bit D1 and Bit D0) of
the DATA_FORMAT register (Address 0x31). This results in a high
dynamic range for measurement and a 2.9 mg/LSB scale factor.
After the part is configured for accurate self-test measurement,
several samples of x-, y-, and z-axis acceleration data should be
retrieved from the sensor and averaged together. The number of
samples averaged is a choice of the system designer, but a recom-
mended starting point is 0.1 sec worth of data, which corresponds
to 10 samples at 100 Hz data rate. The averaged values should
be stored and labeled appropriately as the self-test disabled data,
that is, X
Next, self-test should be enabled by setting Bit D7 of the
DATA_FORMAT register (Address 0x31). The output needs
some time (about four samples) to settle after enabling self-test.
After allowing the output to settle, several samples of the x-, y-,
and z-axis acceleration data should be taken again and averaged. It
ST_OFF
, Y
ST_OFF
, and Z
ST_OFF
.
Rev. 0 | Page 26 of 32
is recommended that the same number of samples be taken for
this average as was previously taken. These averaged values should
again be stored and labeled appropriately as the value with self-
test enabled, that is, X
be disabled by clearing Bit D7 of the DATA_FORMAT register
(Address 0x31).
With the stored values for self-test enabled and disabled, the
self-test change is as follows:
X
Y
Z
Because the measured output for each axis is expressed in LSBs,
X
converted to g’s of acceleration by multiplying each value by the
2.9 mg/LSB scale factor, if configured for full-resolution mode.
Additionally, Table 14 through Table 17 correspond to the self-
test range converted to LSBs and can be compared with the
measured self-test change when operating at a V
other voltages, the minimum and maximum self-test output
values should be adjusted based on (multiplied by) the scale
factors shown in Table 13. If the part was placed into ±1.5 g,
10-bit or full-resolution mode, the values listed in Table 14 should
be used. Although the fixed 10-bit mode or a range other than
12 g can be used, a different set of values, as indicated in Table 15
through Table 17, must be used. Using a range below 6 g may
result in insufficient dynamic range and should be considered
when selecting the range of operation for measuring self-test.
If the self-test change is within the valid range, the test is considered
successful. Generally, a part is considered to pass if the minimum
magnitude of change is achieved. However, a part that changes
by more than the maximum magnitude is not necessarily a failure.
ST
ST
ST
ST
, Y
= Z
= X
= Y
ST
ST_ON
ST_ON
ST_ON
, and Z
− Z
− Y
− X
ST
ST_OFF
ST_OFF
ST_OFF
are also expressed in LSBs. These values can be
ST_ON
, Y
ST_ON
, and Z
ST_ON
. Self-test can then
S
of 3.3 V. For