MCP6271R Microchip Technology Inc., MCP6271R Datasheet - Page 14
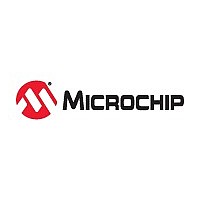
MCP6271R
Manufacturer Part Number
MCP6271R
Description
170 ?a, 2 Mhz Rail-to-rail Op Amp
Manufacturer
Microchip Technology Inc.
Datasheet
1.MCP6271R.pdf
(40 pages)
Available stocks
Company
Part Number
Manufacturer
Quantity
Price
Company:
Part Number:
MCP6271RT-E/OT
Manufacturer:
MCHP
Quantity:
6 004
Part Number:
MCP6271RT-E/OT
Manufacturer:
MICROCHIP/微芯
Quantity:
20 000
In an effort to further reduce size, cost and complexity of linear
solutions, many of the external components can be integrated
into the charge management controller. Advanced packaging
and reduced flexibility come along with higher integration. These
packages require advanced equipment for manufacturing,
and, in many instances, preclude rework. Typically, integration
encompasses charge current sensing, the pass transistor
and reverse discharge protection. In addition, these charge
management controllers typically employ some type of thermal
regulation. Thermal regulation optimizes the charge cycle time
while maintaining device reliability by limiting the charge current
based on the device die temperature. Thermal regulation greatly
reduces the thermal design effort.
Figure 4 depicts a fully integrated, linear solution utilizing
Microchip’s MCP73861. The MCP73861 incorporates all the
features of the MCP73843 along with charge current sensing,
the pass transistor, reverse discharge protection and cell
temperature monitoring.
Figure 4: Typical, Fully Integrated, Linear Solution.
Charge Cycle Waveforms
Figure 5 depicts complete charge cycles utilizing the MCP73843
with constant current charge rates of 1C ad 0.5C. Charging at a
rate of 0.5C instead of 1C, it takes about 1 hour longer for the
end of charge to be reached. The MCP73843 scales the charge
termination current proportionately with the fast charge current.
The result is an increase of 36% in charge time with the benefit
of a 2% gain in capacity and reduced power dissipation. The
change in termination current from 0.07C to 0.035C results in
an increase in final capacity from ~98% to ~100%. The system
designer has to make a trade-off between charge time, power
dissipation and available capacity.
12
Figure 3: Typical Linear Solution.
Analog and Interface Guide – Volume 2
4.3 μF
5V
5V
Charging Lithium Batteries
MA2Q705
10 μF
R
PROG
2, 3
14
16
15
1
5
100 kΩ
V
V
EN
STAT1
STAT2
PROG
DD
SET
MCP73861
R
2
3
4
SENSE
THERM
THREF
TIMER
V
STAT1
EN
V
V
SENSE
DD
BAT3
V
BAT
1
MCP73843
SS
10, 11
12
6
7
8
4, 9, 13
TIMER
8
DRV
V
6.19 kΩ
V
BAT
SS
7.32 kΩ
0.1 μF
7
6
5
10 μF
4.7 μF
0.1 μF
+
–
Single
Lithium-Ion
Cell
+
–
Single
Lithium-Ion
Cell
Figure 5: MCP73843 Charge Cycle Waveforms.
Switch Mode Charging Solutions
Switch mode charging solutions are generally employed in
applications that have a wide ranging input or a high input to
output voltage differential. In these applications, switch mode
solutions have the advantage of improved efficiency. The
disadvantage is system complexity, size and cost.
Take, for example, an application required to charge a
2200 mAh, single Li-Ion cell from a car adapter at a constant
current charge rate of 0.5C or 1C. It would be extremely difficult
to utilize a linear solution in this application due to the thermal
issues involved. A linear solution employing thermal regulation
could be utilized, but the charge cycle times at the reduced
charge currents may be prohibitive.
The first step to designing a successful switch mode charging
solution is to choose a topology: buck, boost, buck-boost, flyback,
Single-Ended Primary Inductive Converter (SEPIC) or other.
Knowing the input and output requirements, and experience,
quickly narrows the choices down to two for this application:
buck or SEPIC. A buck converter has the advantage of requiring
a single inductor. Disadvantages of this topology include an
additional diode required for reverse discharge protection, high-
side gate drive and current sense and pulsed input current (EMI
concern).
The SEPIC topology has advantages that include lowside
gate drive and current sense, continuous input current and
dc isolation from input to output. The main disadvantage of
the SEPIC topology is the use of two inductors and an energy
transfer capacitor.
Figure 6 depicts a schematic for a switch mode charger.
Microchip’s high speed Pulse Width Modulator (PWM), MCP1630,
has been utilized in a pseudo smart battery charger application.
The MCP1630 is a high-speed, microcontroller adaptable, pulse
width modulator. When used in conjunction with a microcontroller,
the MCP1630 will control the power system duty cycle to
provide output voltage or current regulation. The microcontroller,
PIC16F684, can be used to regulate output voltage or current,
switching frequency and maximum duty cycle. The MCP1630
generates duty cycle, and provides fast over current protection
based off various external inputs. External signals include the
input oscillator, the reference voltage, the feedback voltage and
the current sense. The output signal is a square-wave pulse. The
power train used for the charger is SEPIC.
The microcontroller provides an enormous amount of design
flexibility. In addition, the microcontroller can communicate with
a battery monitor (Microchip’s PS700) inside the battery pack to
significantly reduce charge cycle times.
4.50
4.00
3.50
3.00
2.50
2.00
1.50
1.00
0.50
0.00
MCP73843 Charge Cycles, 1000 mAh Battery
0.0
50.0
V
I
BAT
BAT
Time (Minutes)
V
@ 1C
@ 1C
BAT
@ 0.5C
100.0
I
BAT
@ 0.5C
150.0
200.0
1.20
1.00
0.80
0.60
0.40
0.20
0.00