AD7890ARZ-10 Analog Devices Inc, AD7890ARZ-10 Datasheet - Page 15
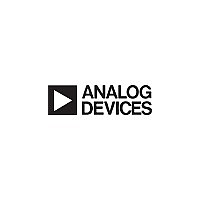
AD7890ARZ-10
Manufacturer Part Number
AD7890ARZ-10
Description
IC DAS 12BIT 8CH 24-SOIC
Manufacturer
Analog Devices Inc
Type
Data Acquisition System (DAS)r
Specifications of AD7890ARZ-10
Resolution (bits)
12 b
Data Interface
Serial
Sampling Rate (per Second)
117k
Voltage Supply Source
Single Supply
Voltage - Supply
±10V
Operating Temperature
-40°C ~ 85°C
Mounting Type
Surface Mount
Package / Case
24-SOIC (7.5mm Width)
Input Channel Type
Single Ended
Supply Voltage Range - Analogue
4.75V To 5.25V
Supply Current
10mA
Digital Ic Case Style
MSOP
No. Of Pins
24
Sampling Rate
117kSPS
Rohs Compliant
Yes
Lead Free Status / RoHS Status
Lead free / RoHS Compliant
Available stocks
Company
Part Number
Manufacturer
Quantity
Price
Company:
Part Number:
AD7890ARZ-10
Manufacturer:
FLATRON
Quantity:
301
Company:
Part Number:
AD7890ARZ-10
Manufacturer:
Analog Devices Inc
Quantity:
1 866
Part Number:
AD7890ARZ-10
Manufacturer:
ADI/亚德诺
Quantity:
20 000
SIMPLIFYING THE INTERFACE
To minimize the number of interconnect lines to the AD7890,
the user can connect the RFS and TFS lines of the AD7890
together and read and write from the part simultaneously. In
this case, new control register data should be provided on the
DATA IN line selecting the input channel and possibly providing
a conversion start command while the part provides the result
from the conversion just completed on the DATA OUT line.
In the self-clocking mode, this means that the part provides all
the signals for the serial interface. It does require that the micro-
processor has the data to be written to the Control Register
available in its output register when the part brings the TFS line
low. In the external clocking mode, it means that the user only
has to supply a single frame synchronization signal to control
both the read and write operations.
Care must be taken with this scheme that the read operation is
completed before the next conversion starts if the user wants to
obtain optimum performance from the part. In the case of the
software conversion start, the conversion command is written to
the Control Register on the sixth serial clock edge. However, the
read operation continues for another 10 serial clock cycles. To
avoid reading during the sampling instant or during conversion,
the user should ensure that the internal pulsewidth is sufficiently
long (by choosing C
before the next conversion sequence begins. Failure to do this
will result in significantly degraded performance from the part,
both in terms of signal-to-noise ratio and dc parameters. In the
case of a hardware conversion start, the user should ensure that
the delay between the sixth falling edge of the serial clock in the
write operation and the next rising edge of CONVST is greater
than the internal pulsewidth.
MICROPROCESSOR/MICROCONTROLLER INTERFACE
The AD7890’s flexible serial interface allows for easy connec-
tion to the serial ports of DSP processors and microcontrollers.
Figures 12 through 15 show the AD7890 interfaced to a num-
ber of different microcontrollers and DSP processors. In some
of the interfaces shown, the AD7890 is configured as the master
in the system, providing the serial clock and frame sync for the
read operation while in others it acts as a slave with these signals
provided by the microprocessor.
DATA IN (I)
SCLK (I)
TFS (I)
EXT
) so that the read operation is completed
t
20
A2
NOTE:
(I) SIGNIFIES AN INPUT; (O) SIGNIFIES AN OUTPUT.
t
21
A1
t
22
A0
CONV
STBY
AD7890–8051 Interface
Figure 12 shows an interface between the AD7890 and the
8xC51 microcontroller. The AD7890 is configured for its exter-
nal clocking mode while the 8xC51 is configured for its Mode 0
serial interface mode. The diagram shown in Figure 12 makes
no provisions for monitoring when conversion is complete on
the AD7890 (assuming hardware conversion start is used). To
monitor the conversion time on the AD7890 a scheme such as
outlined previously with CONVST can be used. This can be
implemented in two ways. One is to connect the CONVST line
to another parallel port bit which is configured as an input. This
port bit can then be polled to determine when conversion is
complete. An alternative is to use an interrupt driven system in
which case the CONVST line should be connected to the INT1
input of the 8XC51.
Since the 8xC51 contains only one serial data line, the DATA
OUT and DATA IN lines of the AD7890 must be connected
together. This means that the 8xC51 cannot communicate with
the output register and Control Register of the AD7890 at the
same time. The 8xC51 outputs the LSB first in a write opera-
tion so care should be taken in arranging the data which is to be
transmitted to the AD7890. Similarly, the AD7890 outputs the
MSB first during a read operation while the 8xC51 expects the
LSB first. Therefore, the data that is to be read into the serial
port needs to be rearranged before the correct data word from
the AD7890 is available in the microcontroller.
The serial clock rate from the 8xC51 is limited to significantly
less than the allowable input serial clock frequency with which
the AD7890 can operate. As a result, the time to read data from
the part will actually be longer than the conversion time of the
part. This means that the AD7890 cannot run at its maximum
throughput rate when used with the 8xC51.
DON’T
CARE
8xC51
P1.0
P1.1
P3.0
P3.1
DON’T
CARE
t
23
V
DD
DON’T
CARE
SMODE
RFS
TFS
DATA OUT
DATA IN
SCLK
AD7890
AD7890