ADIS16334/PCBZ Analog Devices Inc, ADIS16334/PCBZ Datasheet - Page 15
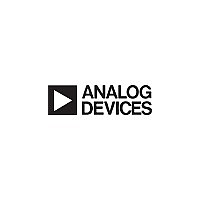
ADIS16334/PCBZ
Manufacturer Part Number
ADIS16334/PCBZ
Description
ADIS16334/PCB EVAL. BD. PB Free
Manufacturer
Analog Devices Inc
Series
iSensor™r
Datasheet
1.ADIS16334BMLZ.pdf
(20 pages)
Specifications of ADIS16334/PCBZ
Sensor Type
Gyroscope, 3 Axis
Sensing Range
±75 ~ 300°/s
Interface
Serial
Sensitivity
0.0125°/sec/LSB
Embedded
No
Utilized Ic / Part
ADIS16334
Lead Free Status / RoHS Status
Lead free / RoHS Compliant
Voltage - Supply
-
Lead Free Status / RoHS Status
Lead free / RoHS Compliant
OPTIMIZING ACCURACY
The mechanical structure and assembly process of the ADIS16334
provide excellent position and alignment stability for each sensor,
even after subjected to temperature cycles, shock, vibration, and
other environmental conditions. The factory calibration includes a
dynamic characterization of each sensor’ s behavior over temperature
and generates sensor-specific correction formulas. The bias
correction registers in Table 19 provide users with the ability to
address bias shifts that can result from mechanical stress. Figure 20
illustrates the summing function of each sensor’s offset correction
register.
Table 19. Registers for User Calibration
Register
XGYRO_OFF
YGYRO_OFF
ZGYRO_OFF
XACCL_OFF
YACCL_OFF
ZACCL_OFF
GLOB_CMD
There are two options for optimizing gyroscope bias accuracy
prior to system deployment: automatic bias correction (ABC)
and manual bias correction (MBC).
AUTOMATIC BIAS CORRECTION
The ABC function provides a simple measure-and-adjust function
for the three gyroscope sensors. Set GLOB_CMD[0] = 1 (DIN =
0xBE01) to start the ABC function, which automatically performs
the following steps to correct the bias on each gyroscope:
1.
2.
3.
4.
5.
6.
The accuracy of the bias correction depends on the internal
averaging time used for the data sample, which depends on the
decimation setting. For example, set SMPL_PRD[15:8] = 0x10
(DIN = 0xB710) to establish a decimation rate of 2
This establishes an averaging time of 80 seconds at a sample
rate of 819.2 SPS, which results in an Allan Variance of 0.006°/sec
in Figure 7.
X-AXIS
MEMS
GYRO
Sets the output range to ±75°/sec
Waits for the next output register update
Reads the output register of the gyroscope
Multiplies the measurement by −1 to change its polarity
Writes the final value into the offset register
Performs a manual flash back-up function to store the
correction factor in nonvolatile flash memory
Figure 20. User Calibration, XGYRO_OFF Example
Address
0x1A
0x1C
0x1E
0x20
0x22
0x24
0x3E
ADC
CALIBRATION
FILTERING
FACTORY
Gyroscope bias, x-axis
Gyroscope bias, y-axis
Gyroscope bias, z-axis
Accelerometer bias, x-axis
Accelerometer bias, y-axis
Accelerometer bias, z-axis
Automatic calibration
Description
AND
XGYRO_OFF
16
, or 65536.
XGYRO_OUT
Rev. 0 | Page 15 of 20
MANUAL BIAS CORRECTION
The MBC function requires the user to collect the desired number
of samples, calculate the averages to develop bias estimates for
each gyroscope channel, and then write them into the bias offset
registers, located in Table 20 for the gyroscopes. For example,
set XGYRO_OFF = 0x1FF6 (DIN = 0x9B1F, 0x9AF6) to adjust
the XGYRO_OUT offset by −0.125°/sec (−10 LSBs). Table 21
provides a manual adjustment function for the accelerometer
channels as well.
Table 20. XGYRO_OFF, YGYRO_OFF, and ZGYRO_OFF
Bit Descriptions
Bits
[15:13]
[12:0]
Table 21. XACCL_OFF, YACCL_OFF, and ZACCL_OFF
Bit Descriptions
Bits
[15:12]
[11:0]
RESTORING FACTORY CALIBRATION
Set GLOB_CMD[1] = 1 (DIN = 0xBE02) to execute the factory
calibration restore function. This is a single-command function,
which resets each user calibration register to 0x0000 and all sensor
data to 0. Then, it automatically updates the flash memory within
50 ms. See Table 23 for more information on GLOB_CMD.
POINT-OF-PERCUSSION/LINEAR-g COMPENSATION
Set MSC_CTRL[6] = 1 (DIN = 0xB446) to enable this feature
and maintain the factory-default settings for DIO1. This feature
performs a point-of-percussion translation to the point identified
in Figure 6. See Table 25 for more information on MSC_CTRL.
Set MSC_CTRL[7] = 1 to enable internal compensation for
linear-g on the gyroscope bias.
Description (Default = 0x0000)
Not used
Data bits. Twos complement, 0.0125°/sec per LSB.
Typical adjustment range = ±50°/sec.
Description (Default = 0x0000)
Not used
Data bits. Twos complement, 1mg/LSB. Typical
adjustment range = ±2 g.
PIN 20
Figure 21. Point of Percussion Reference
PIN 2
ORIGIN ALIGNMENT
REFERENCE POINT
SEE MSC_CTRL[6].
ADIS16334