ISL6721ABZ Intersil, ISL6721ABZ Datasheet - Page 13
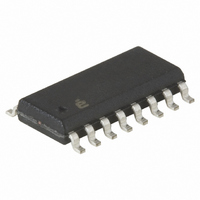
ISL6721ABZ
Manufacturer Part Number
ISL6721ABZ
Description
IC CTRLR PWM SGL ENDED 16-SOIC
Manufacturer
Intersil
Datasheet
1.ISL6721ABZ.pdf
(22 pages)
Specifications of ISL6721ABZ
Pwm Type
Current Mode
Number Of Outputs
1
Frequency - Max
1MHz
Duty Cycle
100%
Voltage - Supply
9 V ~ 18 V
Buck
Yes
Boost
Yes
Flyback
Yes
Inverting
No
Doubler
No
Divider
No
Cuk
No
Isolated
Yes
Operating Temperature
-40°C ~ 105°C
Package / Case
16-SOIC (3.9mm Width)
Frequency-max
1MHz
Peak Reflow Compatible (260 C)
Yes
Rohs Compliant
Yes
Lead Free Status / RoHS Status
Lead free / RoHS Compliant
Available stocks
Company
Part Number
Manufacturer
Quantity
Price
Company:
Part Number:
ISL6721ABZ
Manufacturer:
Intersil
Quantity:
135
Company:
Part Number:
ISL6721ABZ
Manufacturer:
Intersil
Quantity:
500
Part Number:
ISL6721ABZ
Manufacturer:
INTERSIL
Quantity:
20 000
Part Number:
ISL6721ABZ-T
Manufacturer:
INTERSIL
Quantity:
20 000
Maximum Primary Inductance:
Choose desired primary inductance to be 40µH.
The core structure must be able to deliver a certain amount
of energy to the secondary on each switching cycle in order
to maintain the specified output power.
where Δw is the amount of energy required to be transferred
each cycle and Vd is the drop across the output rectifier.
The capacity of a gapped ferrite core structure to store
energy is dependent on the volume of the airgap and can be
expressed in Equation 12:
where Aeff is the effective cross sectional area of the core in
m
permeability of free space (4π • 10
in flux density in Tesla.
A core structure having less airgap volume than calculated will
be incapable of providing the full output power over some
portion of its operating range. On the other hand, if the length
of the airgap becomes large, magnetic field fringing around
the gap occurs. This has the effect of increasing the airgap
volume. Some fringing is usually acceptable, but excessive
fringing can cause increased losses in the windings around
the gap resulting in excessive heating. Once a suitable core
and gap combination are found, the iterative design cycle
begins. A design is developed and checked for ease of
assembly and thermal performance. If the core does not allow
adequate space for the windings, then a core with a larger
window area is required. If the transformer runs hot, it may be
necessary to lower the flux density (more primary turns, lower
operating frequency), select a less lossy core material,
change the geometry of the windings (winding order), use
heavier gauge wire or multi-filar windings, and/or change the
type of wire used (Litz wire, for example).
For simplicity, only the final design is further described.
An EPCOS EFD 20/10/7 core using N87 material gapped to
an A
required air gap volume to store the energy required, but
was needed for the window area it provides.
The flux density ΔB is only 0.069T or 690 gauss, a relatively
low value.
Lp max
Δw
Vg
2
Aeff = 31 • 10
lg = 1.56 • 10
(
, lg is the length of the airgap in meters, µ
=
=
L
P
Aeff lg
value of 25nH/N
OUT
)
=
•
V
-------------------------------------------------------- -
•
IN MIN
----------------------------------- -
〈
f
V
=
(
sw
-3
-6
OUT
2 μ
-----------------------------
•
•
I
V
)
PPK
m
ΔB
m
•
+
OUT
o
t
Vd
2
ON MAX
2
•
2
Δw
was chosen. It has more than the
〉
(
13
)
joules
=
m
3
43.3
-7
), and ΔB is the change
μH
o
is the
(EQ. 12)
(EQ. 10)
(EQ. 11)
ISL6721
Since:
L
the number of primary turns, N
result is N
calculated as follows:
N
where tr is the time required to reset the core. Since
discontinuous MMF mode operation is desired, the core
must completely reset during the off time. To maintain
discontinuous mode operation, the maximum time allowed to
reset the core is t
minimum time is application dependent and at the designers
discretion knowing that the secondary winding RMS current
and ripple current stress in the output capacitors increases
with decreasing reset time. The calculation for maximum N
for the 3.3 V output using t = t
turns.
The determination of the number of secondary turns is also
dependent on the number of outputs and the required turns
ratios required to generate them. If Schottky output rectifiers
are used and we assume a forward voltage drop of 0.45V,
the required turns ratio for the two output voltages, 3.3V and
1.8V, is 5:3.
With a turns ratio of 5:3 for the secondary windings, we will
use N
using these values for the number of secondary turns yields
a duration of Tr = 2.33µs or about 47% of the switching
period, an acceptable result.
The bias winding turns may be calculated similarly, only a
diode forward drop of 0.7V is used. The rounded off result is
17 turns for a 12V bias.
The next step is to determine the wire gauge. The RMS
current in the primary winding may be calculated using
Equation 15:
The peak and RMS current values in the remaining windings
may be calculated using Equations 16 and 17:
I
I
The RMS current for the primary winding is 0.72A, for the
3.3V output, 4.23A, for the 1.8V output, 1.69A, and for the
bias winding, 85mA.
I
SPK
RMS
p
P RMS
s
(
≤
=
------------------------------------------------------- -
N
Ig
μ
----------------------------------------
=
s1
=
p
o
•
)
•
2 I
------------------------------------ -
•
2 I
= 5 turns and N
〈
Ippk μ
=
•
N
•
Vout
p
p
I
lg
OUT
OUT
= 40 turns. The secondary turns may be
PPK
2
Tr
•
•
+
Aeff
•
•
•
Vd
o
sw
t
•
sw
〉 tr
t
-------------------------- -
-------------- -
3 Tr
Aeff
ON MAX
t
•
- t
3 t
sw
•
•
ON(MAX)
(
s2
μH
sw
A
= 3 turns. Checking the reset time
)
sw
A
p
, may be calculated. The
where t
- t
A
ON (MAX)
sw
= 1/f
= 2.75µs is 5.52
sw
. The
March 5, 2008
(EQ. 15)
(EQ. 14)
(EQ. 16)
(EQ. 17)
(EQ. 13)
FN9110.6
s