LTC5100EUF Linear Technology, LTC5100EUF Datasheet - Page 26
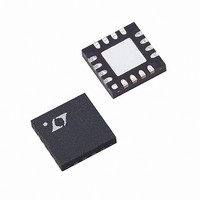
LTC5100EUF
Manufacturer Part Number
LTC5100EUF
Description
IC DRIVER VCSEL 3.2GBPS 16QFN
Manufacturer
Linear Technology
Type
Laser Diode Driverr
Datasheet
1.LTC5100EUF.pdf
(52 pages)
Specifications of LTC5100EUF
Data Rate
3.2Gbps
Number Of Channels
1
Voltage - Supply
3.135 V ~ 3.465 V
Current - Supply
54mA
Current - Modulation
12mA
Operating Temperature
-40°C ~ 85°C
Package / Case
16-QFN
Mounting Type
Surface Mount
Lead Free Status / RoHS Status
Contains lead / RoHS non-compliant
Available stocks
Company
Part Number
Manufacturer
Quantity
Price
Company:
Part Number:
LTC5100EUF
Manufacturer:
LT
Quantity:
10 000
Part Number:
LTC5100EUF
Manufacturer:
LINEAR/凌特
Quantity:
20 000
Company:
Part Number:
LTC5100EUF#PBF
Manufacturer:
LT
Quantity:
5 000
Part Number:
LTC5100EUF#PBF
Manufacturer:
LINEAR/凌特
Quantity:
20 000
OPERATIO
LTC5100
current can be temperature compensated with first and
second order temperature coefficients.
Servo Control
The laser bias current is controlled by a digital servo loop
(shown in the upper half of Figure 4) and can be under-
stood as follows. The nominal bias current, Ib_nom, is
multiplied by a temperature compensation factor, produc-
ing a 10-bit digital set point value, Ib_set. Ib_set is the
target value for the laser bias current. The ADC digitizes the
SRC pin current and the average modulation current,
producing 10-bit values Is_adc and Im_adc. The laser bias
current is the difference between the SRC pin current and
the average modulation current (Equation 1). The system
generates a digital representation of the laser bias current
by calculating:
where Ib_adc is the result of a calculation. (The ADC never
digitizes the laser bias current directly.)
The difference between the target value and the actual
value is the servo loop error signal, Ib_error. Ib_error is
multiplied by a constant, Ib_gain, to set the loop gain. The
result is integrated in a digital accumulator and applied to
a 10-bit DAC, increasing or decreasing the SRC pin current
as required to drive the loop error to zero. The servo loop
adjusts the SRC pin current every four milliseconds,
producing 250 servo iterations per second.
The simplified difference equation for the bias current
servo loop is, assuming Im_nom = 0:
Ib_gain is a 5-bit digital value, so the scaling factor,
Ib_gain/32, takes on the discrete values 0, 1/32, 2/32, …,
31/32. If Ib_gain • (Is_rng + 1) = 16, then Ib_gain • (Is_rng
+ 1)/32 = 0.5 and the error in the control loop is cut in half
26
Ib_adc = Is_rng • Is_adc – Im_rng • Im_adc
Ib adc
Ib adc
Ib adc
_
_
•
Ib set Ib adc
_
_
n
n
n
1
–
1
Ib gain
U
Ib gain
_
_
32
_
32
n
• ( _
1
Is rng
• ( _
Is rng
1
)• _
1
Ib error
)
(26)
( )
27
with each servo iteration. In this case the step response of
the loop is given by, assuming Im_nom = 0 :
The step response has the familiar exponential settling
characteristic of a first order system. The step response
is shown in Figure 26 for Ib_gain • (Is_rng + 1) = 16. The
remaining error is reduced by one-half with each servo
iteration. In seven iterations, or about 28ms, the laser bias
current settles to under 1% in this example. The mea-
sured step response is shown in the Typical Performance
Characteristics.
Reducing Ib_gain slows the settling time and increasing
Ib_gain speeds the settling time. For example, with Ib_gain
• (Is_rng + 1) = 1, the residual loop error is cut by 1/32 with
each servo iteration. In this case it would take 145 servo
iterations (about 580ms) to settle to 1%. With Ib_gain •
(Is_rng + 1) = 31, the residual servo loop error is cut by 31/
32 with each servo iteration. In this case it would take only
two servo iterations (about 8ms) to settle to 1%.
Setting Im_nom
bias current somewhat. This effect can easily be compen-
sated by increasing Ib_gain.
Temperature Compensation
The set point value for the laser bias current, Ib_set in
Figure 4, can change with temperature to compensate the
temperature dependence of the laser diode’s threshold
current. Temperature measurements are supplied either
Ib adc
Ib set
Ib_adc
_
_
0
Figure 26. Step Response of the Laser Bias
Current for (Ib_gain) • (Is_rngtl ) = 16
• –
n
4
1
1
2
8
1
–
0 slows the settling time of the laser
12
3
Ib gain Is rng
_
16
4
20
5
• ( _
32
24
6
28
7
Ib_set
32
8
1
)
SERVO
ITERATIONS
TIME (ms)
n
5100 F26
sn5100 5100fs
(28)