MAX147EVKIT-DIP Maxim Integrated Products, MAX147EVKIT-DIP Datasheet - Page 3
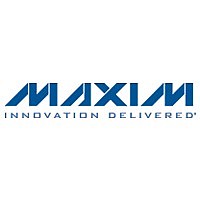
MAX147EVKIT-DIP
Manufacturer Part Number
MAX147EVKIT-DIP
Description
EVAL KIT FOR MAX147
Manufacturer
Maxim Integrated Products
Specifications of MAX147EVKIT-DIP
Number Of Adc's
1
Number Of Bits
12
Sampling Rate (per Second)
133k
Data Interface
Serial
Inputs Per Adc
8 Single Ended
Input Range
±VREF/2
Power (typ) @ Conditions
2.7mW @ 133kSPS
Voltage Supply Source
Single Supply
Operating Temperature
0°C ~ 70°C
Utilized Ic / Part
MAX147
Lead Free Status / RoHS Status
Lead free / RoHS Compliant
internal 1.2V bandgap reference remains active. The
MAX146 is always fully powered during conversions.
The RS-232 serial link limits the data-logging sample
rate to no more than 10sps (samples per second). The
data-logging command is used to write data to a user-
specified file in plain comma-spaced-value text format.
From the control panel screen, press L. If a log file is
not already open, the software asks for a file name.
Only one log file is allowed per session. Once a log file
is open, press L to toggle data logging on or off.
With data logging enabled, “Logging” flashes on the
screen. One complete line of data is written after all
enabled channels are sampled.
The first line of the log file contains the column head-
ings. Each subsequent line of the log file contains all
eight channels, separated by commas. The values are
written as raw decimal output codes or as scaled volt-
ages, depending on which setting the control panel is
currently displaying. Use the C and V commands to
select the display format (Table 3). F3, the log data
marker command, can be used to sequentially tag dif-
ferent sections of the log file to indicate a change in
setup or input conditions. Pressing F3 writes an extra
entry at the end of the current line of the data log, to
indicate a change in setup or input conditions.
The S command samples rates over 10 samples per
second (sps). Data is collected from only one of the
eight channels at a rate from 100sps to 91ksps. First,
select the channel by pressing one of the number keys
0–7. Next, press F to specify the name of the file into
which the samples should be written. If the file already
exists, the screen displays “*** file already exists ***”.
To begin collecting data, press B. After the samples are
collected, the data is automatically uploaded to the
host and stored in the sample file.
The rate for high-speed sampling, data logging, and
the oscilloscope demo mode (Table 3, key O) is con-
trolled by the D (delay between samples) command.
When used with the sample or oscilloscope demo com-
mands, specify the approximate delay in microseconds
or milliseconds by typing D, then the number, then “µsec”
or “msec”. Always verify timing by using an oscilloscope,
since this delay is not linear due to code overhead. The
fast sampling screen and oscilloscope demo mode use
delays from 100µs to 1000µs. The 68HC16 software sup-
ports delays between 68µs and 1000ms. The 80C32 soft-
ware supports delays between 450µs and 70ms.
MAX147 Evaluation System/Evaluation Kit
Controlling the Sampling Rate
_______________________________________________________________________________________
High-Speed Data Sampling
Low-Speed Data Logging
When used with the slower data-logging command,
specify the delay in seconds. The delay is between
enabled channels, and one line of data is logged after
all enabled channels have been polled.
COM is connected to ground (default) or to a user-
supplied analog common voltage applied to the
EXTCOM input pad. Press F6 to select the desired
COM connection.
The EV kit software can measure a user-applied COM
voltage. When F4 is pressed from the control panel
screen (Table 3), the software connects the EXTCOM
input pad to input channel 0. Next, the software con-
nects COM to ground. The channel 0 voltage is mea-
sured in single-ended unipolar mode. The measure-
ment is performed several times and averaged. After
measuring the external COM pad voltage, the switches
are restored to their previous configuration.
The EV kit software program KIT147.S19 loaded into
the 68HC16 module uses a 24-bits-per-transfer mode,
which operates at 59ksps throughput. Refer to the tim-
ing diagrams in the Clock Modes section of the
MAX147 data sheet.
Table 1. Recommended QSPI Setup
Parameters for 24 Bits per Transfer
(used in KIT147.S19)
PARAMETER
CPHA
CPOL
SPBR
BITS
CR0
CR1
RR1
DTL
TR0
TR1
5 (1.68MHz)
0 (clock is idle low)
0 (data is stable on clock rising edge)
16 (when enabled)
4 (7.6µs delay used in internal clock mode)
0000 0000 1xxx xxyy (configure and start
conversion)
0000 0000 0000 0000 (read data)
External clock: 1000 xxx0 (hold CS low).
Internal clock: 1010 xxx0 (hold CS low; DT
delay after transfer).
0100 xxx0 (16-bit enable)
Received data, left justified, with one lead-
ing zero bit
Operating with QSPI,
24 Bits per Transfer
VALUE
COM Voltage
3