MCP212XDM Microchip Technology, MCP212XDM Datasheet - Page 20
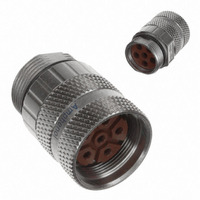
MCP212XDM
Manufacturer Part Number
MCP212XDM
Description
BOARD DEVELOPMENT IRDA
Manufacturer
Microchip Technology
Datasheet
1.MCP2122T-ESN.pdf
(58 pages)
Specifications of MCP212XDM
Main Purpose
Interface, IrDA
Utilized Ic / Part
MCP2120, MCP2122
Silicon Manufacturer
Microchip
Silicon Core Number
MCP2120, MCP2122
Core Architecture
PIC
Core Sub-architecture
PIC18
Kit Contents
MCP2120/22 Developers Board, Important Information Read First
Lead Free Status / RoHS Status
Lead free / RoHS Compliant
Secondary Attributes
-
Embedded
-
Primary Attributes
-
Lead Free Status / RoHS Status
Lead free / RoHS Compliant
Available stocks
Company
Part Number
Manufacturer
Quantity
Price
Company:
Part Number:
MCP212XDM
Manufacturer:
MICROCHIP
Quantity:
12 000
MCP2120/22 Developer’s Board User’s Guide
2.2
DS51842A-page 16
THE DEMO SYSTEM
The demo system setup requires two encoder/decoders. This can be two MCP2120/22
Developer’s Boards or one MCP2120/22 Developer’s Board and another
encoder/decoder device (such as an USB to IR port dongle with appropriate drivers).
The MCP2120/22 Developer’s Board can be powered by one of two sources:
• The USB sourced power
• The Power supply test points
For the demo descriptions, the board will be powered via USB. So a PC with an UART
and USB port is required. The USB voltage is regulated to 3.3V, due to the PIC18
device’s voltage operating range. The PIC18 generates the clock for the MCP2120/22.
This developer’s board can be configured to pass data between the IR interface and
the UART interface or to act as a stand alone embedded system.
There are four step by step descriptions for the MCP2120/22 Developer’s Board
demos. These are:
• Demo #1 Operation - Direct IR / UART (DB-9) Mode
• Demo #2 Operation - Echo Character Received (Change Case)
• Demo #3 Operation - Data Stream Mode
• Demo #4 Operation - Pass Through Mode 1
2.2.1
The PIC18F65J50 firmware program operation is determined by the state of the JMP6
header. See Figure 1-5 and Figure 1-6 for selecting the different programs. Also the
signal routing jumper headers need to be properly configured to ensure that the signals
to/from the sources/destinations are proper for the selected firmware operation.
The firmware may also generate a clock source which will be used by the MCP2122
and can be used by the MCP2120.
Table 2-2 shows the state of the MODE7, MODE3 and MODE2:0 signals which are
used to create the clock source for the MCP2120/22 device.
Table 2-3 shows the state of the MODE7, MODE3 and MODE6:4 signals which are
used to specify the program that will be executed.
If the device is the MCP2120, then three output signals will control the state of the
MCP2120’s BAUD2:0 pins to control the MCP2120’s baud rate.
All the other I/O pins will either be left as an input so not to conflict with other signals,
or will be configured as an output and driven high or low.
Note:
The PIC18F65J50 Firmware
The connectivity of these PIC18F65J50 signals to the MCP2120/22 is
dependant on the configuration of the Jumpers JP1 and JMP1 through
JMP5.
© 2009 Microchip Technology Inc.