LTM4601EV#PBF Linear Technology, LTM4601EV#PBF Datasheet - Page 12
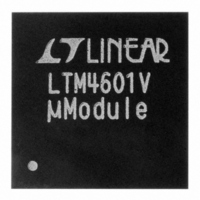
LTM4601EV#PBF
Manufacturer Part Number
LTM4601EV#PBF
Description
IC DC/DC UMODULE 12A 118-LGA
Manufacturer
Linear Technology
Series
µModuler
Type
Point of Load (POL) Non-Isolatedr
Datasheet
1.LTM4601EV-1PBF.pdf
(30 pages)
Specifications of LTM4601EV#PBF
Design Resources
LTM4601 Spice Model
Output
0.6 ~ 5 V
Number Of Outputs
1
Power (watts)
60W
Mounting Type
Surface Mount
Voltage - Input
4.5 ~ 20V
Package / Case
118-LGA
1st Output
0.6 ~ 5 VDC @ 12A
Size / Dimension
0.59" L x 0.59" W x 0.11" H (15mm x 15mm x 2.8mm)
Power (watts) - Rated
60W
Operating Temperature
-40°C ~ 85°C
Efficiency
95%
Lead Free Status / RoHS Status
Lead free / RoHS Compliant
3rd Output
-
2nd Output
-
Available stocks
Company
Part Number
Manufacturer
Quantity
Price
LTM4601/LTM4601-1
For a buck converter, the switching duty-cycle can be
estimated as:
Without considering the inductor current ripple, the RMS
current of the input capacitor can be estimated as:
In the above equation, η% is the estimated effi ciency of
the power module. C
aluminum capacitor, OS-CON capacitor or high volume
ceramic capacitor. Note the capacitor ripple current ratings
are often based on temperature and hours of life. This
makes it advisable to properly derate the input capacitor,
or choose a capacitor rated at a higher temperature than
required. Always contact the capacitor manufacturer for
derating requirements.
In Figure 18, the 10μF ceramic capacitors are together
used as a high frequency input decoupling capacitor. In a
typical 12A output application, three very low ESR, X5R or
X7R, 10μF ceramic capacitors are recommended. These
decoupling capacitors should be placed directly adjacent
to the module input pins in the PCB layout to minimize
the trace inductance and high frequency AC noise. Each
10μF ceramic is typically good for 2A to 3A of RMS ripple
current. Refer to your ceramics capacitor catalog for the
RMS current ratings.
Multiphase operation with multiple LTM4601 devices in
parallel will lower the effective input RMS ripple current due
to the interleaving operation of the regulators. Application
Note 77 provides a detailed explanation. Refer to Figure 2
for the input capacitor ripple current requirement as a
function of the number of phases. The fi gure provides a
ratio of RMS ripple current to DC load current as function
of duty cycle and the number of paralleled phases. Pick
APPLICATIONS INFORMATION
12
D
I
CIN RMS
=
(
V
V
OUT
IN
)
=
I
OUT MAX
η
(
%
IN
can be a switcher-rated electrolytic
)
•
D
• –
(
1
D
)
the corresponding duty cycle and the number of phases
to arrive at the correct ripple current value. For example,
the 2-phase parallel LTM4601 design provides 24A at 2.5V
output from a 12V input. The duty cycle is DC = 2.5V/12V
= 0.21. The 2-phase curve has a ratio of ~0.25 for a duty
cycle of 0.21. This 0.25 ratio of RMS ripple current to a
DC load current of 24A equals ~6A of input RMS ripple
current for the external input capacitors.
Output Capacitors
The LTM4601 is designed for low output voltage ripple.
The bulk output capacitors defi ned as C
with low enough effective series resistance (ESR) to meet
the output voltage ripple and transient requirements. C
can be a low ESR tantalum capacitor, a low ESR polymer
capacitor or a ceramic capacitor. The typical capacitance is
200μF if all ceramic output capacitors are used. Additional
output fi ltering may be required by the system designer,
if further reduction of output ripple or dynamic transient
spike is required. Table 2 shows a matrix of different output
voltages and output capacitors to minimize the voltage
droop and overshoot during a 5A/μs transient. The table
optimizes total equivalent ESR and total bulk capacitance
to maximize transient performance.
Figure 2. Normalized Input RMS Ripple Current
vs Duty Factor for One to Six Modules (Phases)
0.6
0.5
0.4
0.3
0.2
0.1
0
0.1
0.2
0.3
DUTY FACTOR (V
0.4
1-PHASE
2-PHASE
3-PHASE
4-PHASE
6-PHASE
12-PHASE
0.5
OUT
0.6
/V
IN
0.7
)
0.8
4601 F02
OUT
0.9
are chosen
4601fb
OUT