DS1864T+ Maxim Integrated Products, DS1864T+ Datasheet - Page 20
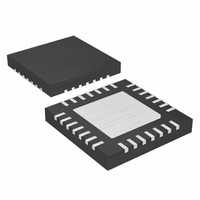
DS1864T+
Manufacturer Part Number
DS1864T+
Description
IC LASER CTRLR 1CHAN 5.5V 28TQFN
Manufacturer
Maxim Integrated Products
Type
Laser Diode Controller (Fiber Optic)r
Datasheet
1.DS1864TTR.pdf
(72 pages)
Specifications of DS1864T+
Number Of Channels
1
Voltage - Supply
2.97 V ~ 5.5 V
Current - Supply
3mA
Operating Temperature
-40°C ~ 95°C
Package / Case
28-WFQFN Exposed Pad
Mounting Type
Surface Mount
Lead Free Status / RoHS Status
Lead free / RoHS Compliant
SFP Laser Controller and
Diagnostic IC
The gain register is now set and the resolution of the
conversion will match the expected LSB. Customers
requiring nonzero null values (e.g., 0.5V as the example
shows) must next calibrate the input’s offset. If the
desired null value is 0V, leave the offset register pro-
grammed to 0000h and skip this step.
To calibrate the offset register, program the gain regis-
ter with the gain_result value determined above. Next,
force the null input voltage (0.5V for the example) and
read the digital result from the part (Meas1). The offset
value can be calculated using the following formula:
This value is then programmed into the corresponding
offset register.
The DS1864 offers a brand new feature to improve the
accuracy and range of MON3, which is most commonly
used for monitoring RSSI. Predecessors of the DS1864,
namely the DS1859 and the DS1856, feature program-
mable gain, offset, and right shifting (Scalable Dynamic
Ranging) on each of the MON channels. These three
elements are extremely beneficial when monitoring low-
amplitude signals such as RSSI. The accuracy of the
RSSI measurements is increased at the small cost of
reduced range (of input signal swing). The DS1864
eliminates this tradeoff by offering “dual-range” calibra-
tion on the MON3 channel. This feature enables right
shifting (along with its gain and offset settings) when
the input signal is below a set threshold (within the
range that benefits using right shifting) and then auto-
matically disables right shifting (recalling different gain
and offset settings) when the input signal exceeds the
threshold. Also, to prevent “chattering,” hysteresis pre-
vents excessive switching between modes in addition
to ensuring that continuity is maintained. Dual-range
operation is enabled by default (factory programmed in
EEPROM). However, it can easily be disabled by the
RSSIF and RSSIC bits, which are described later in this
section. When dual-range operation is disabled, MON3
operates identically to the other MON channels,
although featuring a differential input.
Dual-range functionality consists of two modes of oper-
ation: fine mode and course mode. Each mode is cali-
brated for a unique transfer function, hence the term
“dual range.” Table 7 highlights the registers related to
MON3. Fine mode is equivalent to the other MON chan-
nels and is similar to the DS1859 and DS1856. Fine
mode is calibrated using the gain, offset, and right
20
____________________________________________________________________
OFFSET
= − ×
Enhanced RSSI Monitoring
(Dual-Range Functionality)
1
⎛
⎜
⎝
Meas
4
1
⎞
⎟
⎠
shifting registers at locations shown in Table 7 and is
ideal for relatively small analog input voltages. Course
mode is automatically switched to when the input
exceeds the threshold (to be discussed in a subse-
quent paragraph). Course mode is calibrated using dif-
ferent gain and offset registers, but lacks right shifting
(since course mode is only used on large input sig-
nals). The gain and offset registers for course mode are
also shown in Table 7. Additional information for each
of the registers can be found in the memory map.
Dual-range operation is transparent to the end user.
The results of MON3 analog-to-digital conversions are
still stored/reported in the same memory locations (68
to 69h, Lower Memory) regardless of whether the con-
version was performed in fine mode or course mode.
The only way to tell which mode generated the digital
result is by reading the RSSIS bit.
When the DS1864 is powered up, analog-to-digital con-
versions begin in a round-robin fashion. Every MON3
timeslice begins with a fine mode analog to digital con-
version (using fine mode’s gain, offset, and right-shift-
ing settings). See the flowchart in Figure 15. Then,
depending on whether the last MON3 timeslice resulted
in a course mode conversion and also depending on
the value of the current fine conversion, decisions are
made whether to use the current fine mode conversion
result or to make an additional conversion (within the
same MON3 timeslice), using course mode (using
course mode’s gain and offset settings⎯and remem-
ber, no right shifting) and reporting the course mode
result. The flowchart also illustrates how hysteresis is
implemented. The fine mode conversion is compared
to one of two thresholds. The actual threshold values
are a function of the number of right shifts being used.
Table 6 shows the threshold values for each possible
number of right shifts.
The RSSIF and RSSIC bits are used to force fine mode
or course mode conversions, or to disable the dual-
range functionality. Dual-range functionality is enabled
by default (both RSSIC and RSSIF are factory pro-
grammed to “0” in EEPROM). It can be disabled by set-
ting RSSIC to 0 and RSSIF to 1. These bits are also
useful when calibrating MON3. For additional informa-
tion, see the Memory Map.
The DS1864 provides a variety of system alerts to help
automate laser control. These alerts are in the form of
fast-trip comparators, fast-trip alarm and warning
thresholds, diagnostic alarm and warning thresholds,
and configurable laser eye safety and shutdown logic.
Fast-trip comparator values are measured against fast-
trip thresholds to set alarms and to enable fault and
Fault Management