NCP1002P ON Semiconductor, NCP1002P Datasheet - Page 9
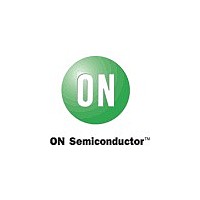
NCP1002P
Manufacturer Part Number
NCP1002P
Description
IC OFFLINE SWIT PWM UVLO HV 8DIP
Manufacturer
ON Semiconductor
Type
Integrated Off-Line Switching Regulatorr
Datasheet
1.NCP1001P.pdf
(14 pages)
Specifications of NCP1002P
Output Isolation
Isolated
Frequency Range
90 ~ 115kHz
Voltage - Input
7.5 ~ 10 V
Voltage - Output
700V
Operating Temperature
-40°C ~ 125°C
Package / Case
8-DIP (0.300", 7.62mm)
Operating Temperature Range
- 40 C to + 125 C
Mounting Style
Through Hole
Lead Free Status / RoHS Status
Contains lead / RoHS non-compliant
Other names
NCP1002POS
Available stocks
Company
Part Number
Manufacturer
Quantity
Price
Part Number:
NCP1002PG
Manufacturer:
ON/安森美
Quantity:
20 000
Current Limit Comparator and Power Switch Circuit
as a means of protecting the output switch transistor from
overstress. Current limiting is implemented by monitoring
the instantaneous output switch current during conduction,
and upon sensing an overcurrent condition, immediately
turning off the switch for the duration of the Oscillator
ramp- -down period.
SENSEFETt allowing a virtually lossless method of
monitoring the drain current. A small number of the power
MOSFET cells are used for current sensing by connecting
their individual sources to a single ground referenced sense
resistor, R
voltage across R
at the noninverting input. If exceeded, the comparator
quickly resets the PWM Latch, thus protecting the Power
Switch Circuit. Figure 9 shows that this detection method
yields a relatively constant current limit threshold over
temperature. The high voltage Power Switch Circuit is
integrated with the control logic circuitry and is designed to
directly drive the converter transformer. The Power Switch
Circuit is capable of switching 700 V with an associated
drain current that ranges from 0.5 A to 1.5 A. Proper drain
voltage snubbing during converter startup and overload is
mandatory for reliable device operation.
sensing signal path to prevent a premature reset of the PWM
Latch. A potential premature reset signal is generated each
time the Power Switch Circuit is driven into conduction and
appears as a narrow voltage spike across current sense
resistor R
capacitance, transformer interwinding capacitance, and
output rectifier recovery time. The Leading Edge Blanking
circuit has a dynamic behavior that masks the current signal
until the Power Switch Circuit turn- -on transition is
completed.
220 ns. This time is measured from when an overcurrent
appears at the Power Switch Circuit drain, to the beginning
of turn- -off. Care must be taken during transformer
saturation so that the maximum device current limit rating
is not exceeded. To determine the peak Power Switch Circuit
current at turn off, the effect of the propagation delay must
be taken into account. To do this, use the appropriate Current
Limit Threshold value from the electrical tables, and then
add the ΔIpk based on the di/dt from Figure 16. The di/dt of
the circuit can be calculated by the following formula:
where:
The NCP1000 series uses cycle- -by- -cycle current limiting
The Power Switch Circuit is constructed using a
A Leading Edge Blanking circuit was placed in the current
The current limit propagation delay time is typically
V is the rectified, filtered input voltage (volts)
L is the primary inductance of the flyback transformer
(Henries)
pk
pk
. The spike is due to the MOSFET gate to source
. The current limit comparator detects if the
pk
exceeds the reference level that is present
di∕dt (A∕ms) = V∕L
http://onsemi.com
9
High Voltage Startup
that eliminates the need for external startup components. In
addition, this circuit increases the efficiency of the supply as
it uses no power when in the normal mode of operation, but
instead uses the power supplied by the auxiliary winding.
internal JFET allows current to flow from the startup pin, to
the V
shows the startup current out of pin 1 which charges the
capacitor(s) connected to this pin.
voltage at Pin 1 (V
enhanced until the V
the Power Switch Circuit will be disabled, and the unit will
generate voltage via the auxiliary winding to maintain
proper operation of the device. Figure 4 shows the charge
time for turn- -on vs. V
initially energized.
mode), the start circuit will again begin conducting, and will
charge up the V
V
guarantee that the integrated circuit has sufficient voltage to
be fully functional before the output stage is enabled. It
inhibits operation of the major functions of the device by
disabling the Internal Bias circuitry, and assures that the
Power Switch Circuit remains in its “off’’ state as the bias
voltage is initially brought up from zero volts. When the
NCP100x is in the “off’’ state, the High Voltage Startup
circuit is operational. The UVLO is a hysteretic switch and
will hold the device in its “off’’ state any time that the V
voltage is less than 7.5 V. As the V
the NCP100x will remain off until the upper threshold of 8.6
V is reached. At this time the power converter is enabled and
will commence operation. The UVLO will allow the unit to
continue to operate as long as the V
The temperature characteristics of the UVLO circuit are
shown in Figure 8.
will enter the auto restart mode. This happens when the
auxiliary winding of the power transformer does not have
sufficient voltage to support the V
chip. Once the chip is operational, if the V
below 7.5 V the unit will shut down, and the High Voltage
Startup circuit will be enabled. This will charge the V
up to 8.5 V, which will clock the divide by eight counter. The
divide by eight counter holds the Power Switch Circuit off.
This causes the V
discharge and recharge for eight consecutive cycles. After
the eighth cycle, the unit will turn on again. If the fault
remains, the unit will again cycle through the auto restart
mode; if the fault has cleared the unit will begin normal
operation. The auto restart mode greatly reduces the power
dissipation of the power devices in the circuit and improves
CC
The NCP1000- -1002 contain an internal startup circuit
Rectified, filtered ac line voltage is connected to pin 4. An
The start circuit will be enhanced (conducting) when the
If the V
The undervoltage lockout (UVLO) is designed to
If the converter output is overloaded or shorted, the device
Limiter and Undervoltage Lockout
CC
pin at a current of approximately 3.0 mA. Figure 5
CC
voltage drops below 7.5 V (e.g. current limit
CC
CC
cap until the 8.5 V limit is reached.
CC
CC
cap to discharge. It will continue to
) is less than 7.5 V. It will remain
voltage reaches 8.5 V. At this point
CC
capacitance when the unit is
CC
CC
CC
voltage exceeds 7.5 V.
increases past 7.5 V,
requirements of the
CC
voltage falls
CC
cap
CC