pip250m NXP Semiconductors, pip250m Datasheet - Page 15
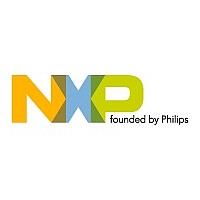
pip250m
Manufacturer Part Number
pip250m
Description
Pip250m Integrated Buck Converter
Manufacturer
NXP Semiconductors
Datasheet
1.PIP250M.pdf
(19 pages)
Philips Semiconductors
15. Mounting
9397 750 10904
Product data
14.2 Rework guidelines
15.1 PCB design guidelines
Since the solder joints are largely inaccessible, only the side fillets can be touched
up. If there are defects underneath the package, then the whole package has to be
removed.
The first step in component removal is to reflow the solder joints. It is recommended
that the board is heated from the underside using a convective heater whilst hot air or
gas is directed at the upper surface of the component. Nozzles should be used to
direct the hot air or gas to minimize heating of adjacent components. Excessive
airflow should be avoided since this may cause the package to skew. An airflow of 15
to 20 liters per minute is usually adequate.
Once the solder joints have reflowed, the component should be lifted off the board
using a vacuum pen.
The next step is to clean the solder pads using solder braid and a blade shaped
soldering tool. Finally, the pads should be cleaned with a solvent. The solvent is
usually specific to the type of solder paste used in the original assembly and the
paste manufacturers recommendations should be followed.
The terminals on the underside of the package are rectangular in shape with a
rounded edge on the inside. Electrical connection between the package and the
printed-circuit board is made by printing solder paste onto the PCB footprint followed
by component placement and reflow soldering. The PCB footprint shown in
is designed to form reliable solder joints.
The use of solder resist between each solder land is recommended. PCB tracks
should not be routed through the corner areas shown in
there is a small, exposed remnant of the lead frame in each corner of the package,
left over from the cropping process.
Good surface flatness of the PCB lands is desirable to ensure accuracy of placement
after soldering. Printed-circuit boards that are finished with a roller tin process tend to
leave small lumps of tin in the corners of each land. Levelling with a hot air knife
improves flatness. Alternatively, an electro-less silver or silver immersion process
produces completely flat PCB lands.
Rev. 02 — 21 February 2003
© Koninklijke Philips Electronics N.V. 2003. All rights reserved.
Figure
Integrated buck converter
15. This is because
PIP250M
Figure 15
15 of 19