lv8130v Sanyo Semiconductor Corporation, lv8130v Datasheet - Page 15
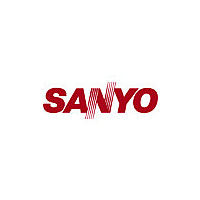
lv8130v
Manufacturer Part Number
lv8130v
Description
For Brushless Motor Drive Direct Pwm Drive, Quiet Predriver Ic
Manufacturer
Sanyo Semiconductor Corporation
Datasheet
1.LV8130V.pdf
(19 pages)
Available stocks
Company
Part Number
Manufacturer
Quantity
Price
Part Number:
lv8130v-MPB-H
Manufacturer:
SANYO/三洋
Quantity:
20 000
Part Number:
lv8130v-TLM-H
Manufacturer:
SANYO/三洋
Quantity:
20 000
4. Current Limiter Circuit
5. Power Saving Circuit
6. Notes on the PWM Frequency
7. Hall Input Signal
8. Undervoltage Protection Circuit
The current limiter circuit limits the output current peak value to a level determined by the equation I = V RF /Rf (V RF
= 0.26V (typical), Rf: current detection resistor). This circuit suppresses the output current by reducing the output on
duty.
High-precision detection can be implemented by connecting lines from
the RF and RFGND pin close to the both ends of the current detection
resisto
The current limiter circuit has an internal filter circuit that works to
prevent incorrect current limiting operation by detecting the reverse recovery current of the output diode due to PWM
operation. In normal applications there should be no problems with the internal filter circuit, but if incorrect operation
occurs (when the diode reverse recovery current flows for 1μs or more), add an external filter circuit (R, C low-pass
filter, etc.).
This IC goes to a low-power mode (power saving state) when set to the stop state. In the power save state, the bias
current in most of the circuits is cut. However, the 5V regulator output (VREG) is
still provided in the power saving state. If it is also necessary to cut the Hall device
bias current, this function can be provided by an application that, for example,
connects the Hall devices to 5V through PNP transistors.
The PWM frequency is determined by the capacitor C (F) connected to the PWM pin.
If a 1000pF capacitor is used, the circuit will oscillate at approx. 25kHz. If the PWM frequency is too low, switching
noise will be audible from the motor, and if it too high, the output power loss will increase. Thus a frequency in the
range of 15kHz and 50kHz must be used. The capacitor’s ground terminal must be placed as close as possible to the
IC’s ground pin to minimize the influence of output noise and other noise sources.
A pulse input with the amplitude in excess of the hysteresis (80mV maximum) is required for the Hall inputs.
Considering the possibility of noise and phase displacement, an even larger amplitude is desirable.
If noise disrupts the output waveform (during phase switching) or the HP output (Hall signal output), this must be
prevented by inserting capacitors or other devices across these inputs. The constraint protection circuit uses the Hall
inputs to discriminate the motor constraint state. Although the circuit is designed to tolerate a certain amount of noise,
care is required when using the constraint protection circuit.
If all three phases of the Hall input signal go to the same input state, the outputs are all set to the off state (the UL, VL,
WL, UH, VH and WH outputs all go to the low level).
If the outputs from a Hall IC are used, fixing one side of the inputs (either the + or – side) at a voltage within the
common-mode input voltage range allows the other input side to be used as an input over the 0V to V CC range.
The undervoltage protection circuit turns one side of the outputs (UH, VH, WH) off when the LVS pin voltage falls
below the minimum operating voltage. (see the Electrical Characteristics.) To prevent
this circuit from repeatedly turning the outputs on and off in the vicinity of the
protection operating voltage, this circuit is designed with hysteresis. Thus the output
will not recover until the operating voltage rises 0.5V (typical) higher than the
operating voltage.
The protection operation voltage detection level is set up for 5V systems. The detected
voltage level can be increased by shifting the voltage by inserting a zener diode in series with the LVS pin to shift the
detection level.
The LVS pin influx current during detection is approx. 80μA. To increase the diode current to stabilize the zener diode
voltage rise, insert a resistor between the LVS pin and ground.
If the LVS pin is left open, it is set to ground level input by the internal pull-down resistor, and the output will be turned
off. Therefore, when not using the undervoltage protection circuit, a voltage in excess of the LVS circuit reset voltage
(4.4V) or more must be applied to the LVS pin. (The LVS pin can also be shorted with 5VREG pin.) The maximum
rating for the voltage applied to the LVS pin is 18V.
r (Rf).
fPWM ≈ 1/(41000 × C)
• Operation voltage ≈ 3.7 + ZD voltage
• Reset voltage ≈ 4.2 + ZD voltage
LV8130V
To RF pin
To the VREG pin
To the S/S pin
To the power supply
Current detection resistor
detected
To the LVS pin
No.A1708-15/19
Hall device