NCV8851B ON Semiconductor, NCV8851B Datasheet - Page 13
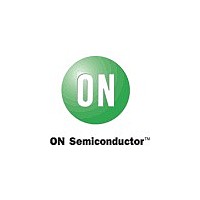
NCV8851B
Manufacturer Part Number
NCV8851B
Description
Automotive Grade Synchronous Buck Controller
Manufacturer
ON Semiconductor
Datasheet
1.NCV8851B.pdf
(18 pages)
The soft−start time can be estimated as follows:
Where: T
(3) Current Sensor Selection
the inductor current signal. This is translated into a voltage
via a current sensor, which is then measured differentially by
the current sense amplifier, generating a single−ended
output to use as a control signal. The easiest means of
implementing this transresistance is through the use of a
sense resistor in series with the output inductor and
capacitors. A sense resistor should be selected as follows:
Where: R
Alternative methods, such as lossless inductor current
sensing, are feasible but beyond the scope of this document.
(4) Output Inductor Selection
the selection of an output inductor. From a mechanical
perspective, smaller inductor values generally correspond to
Table 1. Frequency vs. R
Current sensing for average current mode control relies on
Both mechanical and electrical considerations influence
600
500
400
300
200
100
0
10
F
F
T
V
I
SW
CL
SS
0
SS0
S
CL
170
250
300
360
500
: specified frequency [Hz]
: sense resistor [W]
: desired current limit [A]
(kHz)
: soft−start time [s]
: current limit threshold voltage [V]
20
: soft−start time at specified frequency [s]
Figure 25. Frequency vs. R
30
T
SS
R
[
R
40
OSC
S
OSC
F
+
F
SW
0
(kW)
V
I
50
CL
@ T
CL
SS0
R
60
OSC
51.1
34.8
28.7
23.2
16.2
OSC
(kW)
70
80
http://onsemi.com
NCV8851B
90
13
www.DataSheet.co.kr
smaller physical size. Since the inductor is often one of the
largest components in the power supply, a minimum
inductor value is particularly important in space−
constrained applications. From an electrical perspective, an
inductor is chosen for a set amount of current ripple and to
assure adequate transient response.
current through the output inductor in response to output load
transients, impacting the dynamic response. While the
inductor is slewing current during this time, output capacitors
must supply the load current. Therefore, decreasing the
inductance allows for less output capacitance to hold the
output voltage up during a load step. Load transient
simulation is a powerful tool in anticipating this response.
protection (OCP) and average current limiting (ACL), the
OCP and ACL references are compared to the sensed current
via sense resistance, R
to prevent the OCP from tripping during the onset of ACL
during typical operation as follows:
Where: L
control purposes, the voltage ripple over the sense resistance
must be sufficient in magnitude to counteract the
contribution due to inherent comparator offsets and other
errors, as follows:
Where: L
expressed as follows:
has been empirically sufficient.
maximum achievable slew rate and decrease the necessary
capacitance, at the expense of higher ripple current, which
causes higher output voltage ripple. The peak−to−peak
ripple current is given by the following equation:
Where: i
Larger inductor values limit the switcher’s ability to slew
For switchers with both cycle−by−cycle overcurrent
For switchers that use the current signal of the inductor for
The inductor current ripple to current limit ratio is
As a rule of thumb, ensuring that κ
Smaller values of inductance increase the regulator’s
DV
κ
V
L
MIN
L
L
MAX
CL
: peak−to−peak output current ripple [App]
do not both trip [H]
voltage ripple over the sense resistance [H]
: inductor current ripple to current limit ratio [%]
voltages [V]
MAX
CL
: threshold voltage for the current limit [V]
: minimum inductance to assure OCP and ACL
: difference between OCP and ACL threshold
: maximum inductance to assure adequate
L
+
MIN
V
i
L
+
OUT
+
S
V
. A minimum inductance is required
V
OUT
@ (1 * D
Ë
2 @ F
OUT
F
L
SW
+
L @ F
(1 * D)
@ (1 * D)
SW
I
i
CL
L
SW
MAX
@
L
)
DV
@
is at least 5% to 10%
R
Ë
S
CL
L
R
@ V
S
CL
Datasheet pdf - http://www.DataSheet4U.net/