ISL78100 Intersil Corporation, ISL78100 Datasheet - Page 13
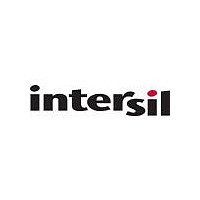
ISL78100
Manufacturer Part Number
ISL78100
Description
Manufacturer
Intersil Corporation
Datasheet
1.ISL78100.pdf
(19 pages)
Over-Temperature Shutdown
An internal sense circuit disables PWM switching if the die
temperature exceeds +135°C. Switching is re-enabled when
the temperature falls below +100°C.
Internal 5V LDO
An internal LDO between V
to power control and gate drive circuits when V
5.1V. In normal operation decouple VDC with at least 3.3µF.
In applications where the input supply is less than 5.5V, VDC
should be tied directly to V
LED Temperature Control
LED lifetime reduces dramatically with elevated
temperature. An over-temperature control circuit utilizing the
thermistor voltage at TEMP reduces the LED bias current
when VTEMP exceeds the threshold voltage on TMAX. To
minimize noise injection, use a potential divider between
VDC and GND to set the voltage on TMAX, as shown in
Figure 34. The value of TMAX for a specific threshold
temperature is determined by the choice of thermistor
temperature coefficient. Disable the function by connecting
the TMAX pin to VDC and TEMP pin to GND.
FB LEVEL
CURRENT
VBAT
FIGURE 34. OVER-TEMPERATURE CIRCUIT
ISL78100
ISL78100
VIN
VBAT FAULT
SWS1 SWS2
FIGURE 33. EXTERNAL OVP CIRCUIT
+
-
LDO
SWD1
SWD2
COMPENSATION
VDC
TEMPERATURE
VIN
FB
IN
IN
.
13
and VDC regulates VDC to 5V,
CREG
0.47µF
10µH
ZOVP
L1
TMAX
GND
TEMP
100
R1
THERMISTOR
CLOSE
TO LEDs
RM2
RM1
80k
20k
RT
0.5
RSENSE
IN
10k
VOUT
exceeds
COUT
20µF
ISL78100
Component Selection
Input Capacitor
Switching regulators require input capacitors to deliver peak
charging current and to reduce the impedance of the input
supply. This reduces interaction between the regulator and
input supply, improving system stability. The high switching
frequency of the loop causes almost all ripple current to flow
in the input capacitor, which must be rated accordingly.
Considerably more input current ripple is generated in buck
mode than boost mode. In buck mode input current is
alternately switched between I
current flow in the input capacitor is given by Equation 3:
Where: D = Duty Cycle
The input current is maximum for D = 0.5 and when I
approaches current limit (2.4A) giving a value of around
1.2A.
A capacitor with low internal series resistance should be
chosen to minimize heating effects and improve system
efficiency, such as X5R or X7R ceramic capacitors, which
offer small size and a lower value of temperature and voltage
coefficient compared to other ceramic capacitors.
In boost mode input current flows continuously into the
inductor, with an AC ripple component proportional to the
rate of inductor charging only and smaller value input
capacitors may be used. It is recommended that an input
capacitor of at least 10µF be used. Ensure the voltage rating
of the input capacitor is suitable to handle the full supply
range.
In automotive applications, the input capacitor can be
protected from exposure to high voltages present during
fault conditions (load dump) by connecting it downstream of
the fault protection switch, as shown in Figures 39 and 40.
Inductor
Careful selection of inductor value will optimize circuit
operation. Inductor type and value influence many key
parameters, including ripple current, current limit, efficiency,
transient performance and stability. Internal slope
compensation has been optimized for inductor values
between 4.7µH and 10µH. Ensure the inductor current rating
is capable of handling the current limit value in the
configuration used (2.4A for buck, 3.5A for boost). If an
inductor core is chosen with too low a current rating,
saturation in the core will cause the effective inductor value
to fall, leading to an increase in peak to average current
level, poor efficiency and overheating in the core.
I
CAPRMS
=
I
OUT
•
(
D D
–
2
)
OUT
and zero. The RMS
December 17, 2007
OUT
(EQ. 3)
FN6626.0