MAX2003 Maxim Integrated Products, MAX2003 Datasheet - Page 15
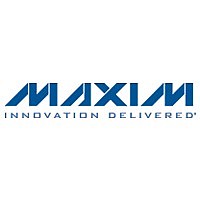
MAX2003
Manufacturer Part Number
MAX2003
Description
Nicd/nimh Battery Fast-charge Controllers
Manufacturer
Maxim Integrated Products
Datasheet
1.MAX2003.pdf
(20 pages)
Available stocks
Company
Part Number
Manufacturer
Quantity
Price
Company:
Part Number:
MAX2003
Manufacturer:
MAX
Quantity:
5 510
Part Number:
MAX2003A
Manufacturer:
MAXIM/美信
Quantity:
20 000
Company:
Part Number:
MAX2003ACSE
Manufacturer:
MAXIM
Quantity:
20
Company:
Part Number:
MAX2003ACSE
Manufacturer:
MAXIM
Quantity:
5 510
Company:
Part Number:
MAX2003ACSE
Manufacturer:
Frontier
Quantity:
5 510
Part Number:
MAX2003ACSE
Manufacturer:
MAXIM/美信
Quantity:
20 000
Part Number:
MAX2003ACWE
Manufacturer:
MAXIM/美信
Quantity:
20 000
Part Number:
MAX2003APA
Manufacturer:
MAXIM/美信
Quantity:
20 000
Part Number:
MAX2003CSE
Manufacturer:
MAXIM/美信
Quantity:
20 000
In order to provide high currents with minimum ripple,
the device must function in the continuous-conduction
mode. Figure 10 shows a current waveform of an
inductor in the continuous-conduction mode (where the
coil current never falls to zero).
The average load current (I
must be 1.7A, so a peak current (I
give a fairly low ripple while keeping the inductor size
minimal. This means that the total current change (Figure
10) across the inductor is i = 2 (1.9 - 1.7) = 0.4A.
The maximum voltage across the inductor is present
when the battery voltage is at its minimum. The mini-
mum cell voltage at the start of fast-charge will be 1V
per cell, giving a battery voltage of 6V for 6 cells. The
maximum voltage (V
The input voltage for this application is 13V, so the
maximum voltage is:
The minimum on-time t of the switch is given by:
where V
maximum input voltage, and PERIOD is the period of
the switching signal.
The maximum input voltage for this application will be
14V, and the maximum allowed switching frequency of
100kHz gives a period of 10µs. The minimum on-time
will therefore be:
The inductor value can be calculated from:
Table 6. External Component Sources
Power
Supply
Thermistor
Power
MOSFET &
Darlington
Transistor
Battery
t = (V
Device
V
L
OUT
L = V t / i = (7V x 4.62µs) / 0.4A = 81µH.
= (input voltage - minimum battery voltage)
OUT
/ V
Manufacturer
Advanced
Power
Solutions
Alpha
Thermistor
Motorola
Duracell
Energizer
Power
Systems
IN
is the minimum battery voltage, V
t = (V
) x PERIOD = (6V / 13V) x 10µs = 4.62µs
V
L
______________________________________________________________________________________
= (13V - 6V) = 7V
OUT
L
) across the inductor is therefore:
/ V
Phone Number
IN
(510) 734-3060
(800) 235-5445
(602) 303-5454
(800) 431-2658
(904) 462-3911
LOAD
) x PERIOD
) through the inductor
MAX
) of 1.9A should
(510) 460-5498
(619) 549-4791
(602) 994-6430
(203) 791-3273
(904) 462-4726
Fax Number
IN
is the
Fast-Charge Controllers
If this inductor value is used, the actual switching fre-
quency will be lower than the 100kHz expected, due to
comparator delays and variations in the duty cycle. The
inductor value selected for our application will be
100µH—a preferred value just above the calculated
value. It is important to choose the saturation current
rating of the inductor to be a little higher than the peak
currents, to prevent the inductor from saturating during
operation. The inductor must be selected to ensure that
the switching frequency of the MOD pin will not exceed
the 100kHz maximum.
_________________________Information
The MAX2003/MAX2003A can use several other cir-
cuits to charge batteries. Figure 9 shows a circuit that
uses a Darlington transistor to regulate the current a
six-cell NiCd battery pack receives. Figure 10 shows a
gated current-limited supply being used to charge a
Duracell NiMH battery pack. Table 6 lists the external
components used in these two application configura-
tions.
The circuit in Figure 11 uses an inexpensive transistor
to provide the charge current. Since the input for the
MAX667 can tolerate up to 16V, this circuit can charge
up to 7 cells. The MAX667 can be replaced with a dif-
ferent regulator if more cells need to be charged. The
DC source must supply a voltage equal to 2x the num-
ber of cells, plus 2V overhead to accommodate the
drop across external components.
When fast-charge is initiated, the voltage at the SNS pin
is sampled and compared to the trip levels (220mV low
and 250mV high). If the voltage at SNS is below
220mV, the MOD pin will switch high, and the 10k/1µF
RC lowpass filter will pull high, turning on the NPN tran-
sistor. This will pull the base of the Darlington TIP115
low, turning it on and allowing current to flow into the
battery. When the current through the battery and SNS
resistor are high enough, the voltage at SNS will
exceed 250mV and the MOD pin will turn off.
The amount of current the battery receives depends on
the resistor between SNS and V
cuit, the average current through the SNS resistor will
be:
The maximum current the resistor will receive is:
The Darlington transistor must be biased to ensure that
a minimum of 0.90A will be supplied. This minimum
I
SNS(AVG)
I
SNS(MAX)
Linear Regulation of Charge Current
NiCd/NiMH Battery
= V
= V
SNS(AVG)
SNS(MAX)
Additional Applications
/ R
/ R
SNS
SNS
= 0.235 / 0.28 = 0.84A
SS
= 0.25 / 0.28 = 0.90A
. In our example cir-
15