MAX2003 Maxim Integrated Products, MAX2003 Datasheet - Page 12
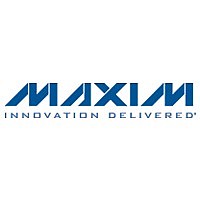
MAX2003
Manufacturer Part Number
MAX2003
Description
Nicd/nimh Battery Fast-charge Controllers
Manufacturer
Maxim Integrated Products
Datasheet
1.MAX2003.pdf
(20 pages)
Available stocks
Company
Part Number
Manufacturer
Quantity
Price
Company:
Part Number:
MAX2003
Manufacturer:
MAX
Quantity:
5 510
Part Number:
MAX2003A
Manufacturer:
MAXIM/美信
Quantity:
20 000
Company:
Part Number:
MAX2003ACSE
Manufacturer:
MAXIM
Quantity:
20
Company:
Part Number:
MAX2003ACSE
Manufacturer:
MAXIM
Quantity:
5 510
Company:
Part Number:
MAX2003ACSE
Manufacturer:
Frontier
Quantity:
5 510
Part Number:
MAX2003ACSE
Manufacturer:
MAXIM/美信
Quantity:
20 000
Part Number:
MAX2003ACWE
Manufacturer:
MAXIM/美信
Quantity:
20 000
Part Number:
MAX2003APA
Manufacturer:
MAXIM/美信
Quantity:
20 000
Part Number:
MAX2003CSE
Manufacturer:
MAXIM/美信
Quantity:
20 000
The top-off charge is done at 1/8 the fast-charge rate.
For the MAX2003, the MOD pin is activated in every 34
second period to supply current to the battery for 4
seconds (MOD oscillates for 4 seconds and stays low
for 30 seconds) (Figure 7). If external regulation is used
(SNS tied to ground), MOD stays high for 4 seconds
and low for 30 seconds (Figure 8). This top-off process
continues until the fast-charge timeout (Table 4) is
exceeded, or if a maximum temperature or maximum
voltage condition is detected. The MAX2003A is slightly
modified to turn the MOD pin on for 0.5sec in every 4
second period. This shorter on-time reduces battery
heat and increases charge acceptance. During the top-
off charge, the CHG pin will cycle low (LED on) for
0.125sec and high (LED off) for 0.125sec.
A trickle-charge is applied to the battery after fast-
charge and top-off charge have terminated to compen-
sate for self discharge. There are two methods of trickle
charge: constant and pulsed.
The MAX2003A provides a pulsed trickle-charge to the
battery by turning on the MOD pin briefly during a fixed
period of time. The duty cycle of the pulse is a function of
the programmable inputs TM1 and TM2 (Table 4 ). The
MAX2003A does not use the trickle resistor to provide the
trickle charge. However, the trickle resistor cannot be
entirely omitted because it is also used for the battery-
detect circuitry.
The MAX2003 provides a steady trickle-charge to the
battery by connecting a resistor from the DC supply to
the positive battery terminal. This resistor has a dual
purpose, in that it provides a trickle-charge and pulls
the BAT pin above the MCV when the battery is absent.
The trickle-charge rate depends on the type of battery
used. For NiCd batteries, a nominal trickle-charge rate
NiCd/NiMH Battery
Fast-Charge Controllers
Table 5. Charge Status
12
Battery Absent
Charge Pending
Discharge-Before-Charge
Fast-Charge
Charge Complete and Top-
Off
______________________________________________________________________________________
Charge State
Constant Trickle-Charge (MAX2003)
Pulsed Trickle-Charge (MAX2003A)
LED off
LED on for 0.125sec, off for
1.375sec
LED on for 1.375sec, off for
0.125sec
LED on
LED on for 0.125sec, off for
0.125sec
CHG LED Status
Trickle-Charge
would be C/16, and NiMH batteries could use a rate of
C/40. The resistor value used depends on the maxi-
mum DC voltage and the typical battery voltage. For
example, a six-cell 800mAh NiCd pack with a nominal
voltage of 1.2V per cell would have a total voltage of
1.2V x 6V = 7.2V. If the DC supply voltage used is 14V,
the voltage across the trickle resistor would be 14.0V -
7.2V = 6.8V. The trickle current needed would be C/16
= 800 / 16 = 50mA. The trickle resistor would therefore
be R
should be made for NiMH batteries using C/40 as the
trickle-charge rate.
If a trickle-charge is not needed, a higher value of trick-
le resistor (like 100kΩ) can be selected to sense the
battery insertion.
The CHG pin is connected to a LED that indicates the
operating mode. Table 5 summarizes the different
charge conditions.
Using the circuit of Figure 1 as an example, the follow-
ing nine steps show how to design a 1.7A switch-mode
fast-charger that can charge a Duracell DR17 (NiMH
six-cell battery pack with a 1700mAh capacity).
1) Select DC Power Supply. The first step is to select
the DC power supply (such as a wall cube). The mini-
mum supply voltage should have a supply equal to
about 2V per cell, plus 1V headroom for external cir-
cuitry ((2V/cell) + 1V). The minimum supply voltage
must be greater than 6V. If, as in our example, there
are six cells, a minimum supply of about 13V is needed
((6 cells x 2V) + 1V).
2) Determine Charge Rate. The charge rate, or fast-
charge current (I
the capacity of the battery, and the time in which the
user wants the battery to be charged. The battery man-
ufacturer recommends a maximum fast-charge rate,
which must not be exceeded.
For example, if a 1700mAh battery needs to be charged
in two hours (C/2), a fast-charge current of at least
850mA is needed. A charge rate of C/2 will ideally charge
a battery in two hours but, because of inefficiencies in a
battery’s chemical processes, the time could be 30% to
40% more. Our example circuit (Figure 1) charges the
Duracell battery pack at a C rate of 1.7A, which should fully
charge a discharged battery in approximately 80 minutes.
_______________________Design Guide
TR
I
FAST
= 6.8V / 50mA ≈ 150Ω. Similar calculations
(mA) = ————————————
FAST
Capacity of Battery (mAh)
), is determined by two factors:
Charge Time (h)
Charge Status