CY7C1367A-150AC Cypress Semiconductor Corp, CY7C1367A-150AC Datasheet - Page 10
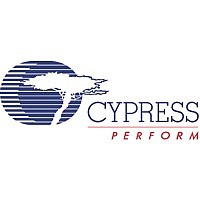
CY7C1367A-150AC
Manufacturer Part Number
CY7C1367A-150AC
Description
Manufacturer
Cypress Semiconductor Corp
Datasheet
1.CY7C1367A-150AC.pdf
(27 pages)
Specifications of CY7C1367A-150AC
Density
9Mb
Access Time (max)
3.5ns
Operating Supply Voltage (typ)
3.3V
Package Type
TQFP
Operating Temp Range
0C to 70C
Supply Current
380mA
Operating Supply Voltage (min)
3.14V
Operating Supply Voltage (max)
3.63V
Operating Temperature Classification
Commercial
Mounting
Surface Mount
Pin Count
100
Word Size
18b
Lead Free Status / Rohs Status
Not Compliant
Boundary Scan Register
The Boundary Scan register is connected to all the input and
bidirectional I/O pins (not counting the TAP pins) on the device.
This also includes a number of NC pins that are reserved for
future needs. There are a total of 70 bits for x36 device and 51
bits for x18 device. The boundary scan register, under the con-
trol of the TAP controller, is loaded with the contents of the
device I/O ring when the controller is in Capture-DR state and
then is placed between the TDI and TDO pins when the con-
troller is moved to Shift-DR state. The EXTEST, SAM-
PLE/PRELOAD and SAMPLE-Z instructions can be used to
capture the contents of the I/O ring.
The Boundary Scan Order table describes the order in which
the bits are connected. The first column defines the bit’s posi-
tion in the boundary scan register. The MSB of the register is
connected to TDI, and LSB is connected to TDO. The second
column is the signal name, the third column is the TQFP pin
number, and the fourth column is the BGA bump number.
Identification (ID) Register
The ID Register is a 32-bit register that is loaded with a device
and vendor specific 32-bit code when the controller is put in
Capture-DR state with the IDCODE command loaded in the
instruction register. The register is then placed between the
TDI and TDO pins when the controller is moved into Shift-DR
state. Bit 0 in the register is the LSB and the first to reach TDO
when shifting begins. The code is loaded from a 32-bit on-chip
ROM. It describes various attributes of the device as described
in the Identification Register Definitions table.
TAP Controller Instruction Set
Overview
There are two classes of instructions defined in the IEEE Stan-
dard 1149.1-1990; the standard (public) instructions and de-
vice specific (private) instructions. Some public instructions
are mandatory for IEEE 1149.1 compliance. Optional public
instructions must be implemented in prescribed ways.
Although the TAP controller in this device follows the IEEE
1149.1 conventions, it is not IEEE 1149.1 compliant because
some of the mandatory instructions are not fully implemented.
The TAP on this device may be used to monitor all input and
I/O pads, but can not be used to load address, data, or control
signals into the device or to preload the I/O buffers. In other
words, the device will not perform IEEE 1149.1 EXTEST, IN-
TEST, or the preload portion of the SAMPLE/PRELOAD com-
mand.
When the TAP controller is placed in Capture-IR state, the two
least significant bits of the instruction register are loaded with
01. When the controller is moved to the Shift-IR state the in-
struction is serially loaded through the TDI input (while the
previous contents are shifted out at TDO). For all instructions,
the TAP executes newly loaded instructions only when the con-
troller is moved to Update-IR state. The TAP instruction sets
for this device are listed in the following tables.
EXTEST
EXTEST is an IEEE 1149.1 mandatory public instruction. It is
to be executed whenever the instruction register is loaded with
all 0s. EXTEST is not implemented in this device.
10
The TAP controller does recognize an all-0 instruction. When
an EXTEST instruction is loaded into the instruction register,
the device responds as if a SAMPLE/PRELOAD instruction
has been loaded. There is one difference between two instruc-
tions. Unlike SAMPLE/PRELOAD instruction, EXTEST places
the device outputs in a High-Z state.
IDCODE
The IDCODE instruction causes a vendor-specific, 32-bit code
to be loaded into the ID register when the controller is in Cap-
ture-DR mode and places the ID register between the TDI and
TDO pins in Shift-DR mode. The IDCODE instruction is the
default instruction loaded in the instruction upon power-up and
at any time the TAP controller is placed in the test-logic reset
state.
SAMPLE-Z
If the High-Z instruction is loaded in the instruction register, all
output pins are forced to a High-Z state and the boundary scan
register is connected between TDI and TDO pins when the
TAP controller is in a Shift-DR state.
SAMPLE/PRELOAD
SAMPLE/PRELOAD is an IEEE 1149.1 mandatory instruction.
The PRELOAD portion of the command is not implemented in
this device, so the device TAP controller is not fully IEEE
1149.1-compliant.
When the SAMPLE/PRELOAD instruction is loaded in the in-
struction register and the TAP controller is in the Capture-DR
state, a snap shot of the data in the device’s input and I/O
buffers is loaded into the boundary scan register. Because the
device system clock(s) are independent from the TAP clock
(TCK), it is possible for the TAP to attempt to capture the input
and I/O ring contents while the buffers are in transition (i.e., in
a metastable state). Although allowing the TAP to sample
metastable inputs will not harm the device, repeatable results
can not be expected. To guarantee that the boundary scan
register will capture the correct value of a signal, the device
input signals must be stabilized long enough to meet the TAP
controller’s capture set up plus hold time (t
device clock input(s) need not be paused for any other TAP
operation except capturing the input and I/O ring contents into
the boundary scan register.
Moving the controller to Shift-DR state then places the bound-
ary scan register between the TDI and TDO pins. Because the
PRELOAD portion of the command is not implemented in this
device, moving the controller to the Update-DR state with the
SAMPLE/PRELOAD instruction loaded in the instruction reg-
ister has the same effect as the Pause-DR command.
BYPASS
When the BYPASS instruction is loaded in the instruction reg-
ister and the TAP controller is in the Shift-DR state, the bypass
register is placed between TDI and TDO. This allows the board
level scan path to be shortened to facilitate testing of other
devices in the scan path.
Reserved
Do not use these instructions. They are reserved for future
use.
CY7C1366A/GVT71256C36
CY7C1367A/GVT71512C18
CS
plus t
CH
). The