IXDP610PI IXYS, IXDP610PI Datasheet - Page 8
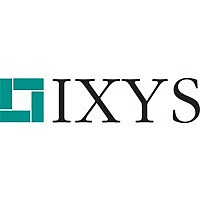
IXDP610PI
Manufacturer Part Number
IXDP610PI
Description
IC PWM CTRL BUS DIGITAL 18-PDIP
Manufacturer
IXYS
Datasheet
1.IXDP610PI.pdf
(8 pages)
Specifications of IXDP610PI
Applications
PWM Motor Controller
Interface
Microprocessor
Voltage - Supply
4.5 V ~ 5.5 V
Package / Case
18-DIP (0.300", 7.62mm)
Mounting Type
Through Hole
Operating Supply Voltage
- 0.3 V to + 5.5 V
Maximum Operating Temperature
85 C
Minimum Operating Temperature
-40 C
Mounting Style
Through Hole
Lead Free Status / RoHS Status
Lead free / RoHS Compliant
Available stocks
Company
Part Number
Manufacturer
Quantity
Price
Company:
Part Number:
IXDP610PI
Manufacturer:
CEO
Quantity:
6 225
© 2001 IXYS/DEI All rights reserved
a)
b)
c)
d)
e)
Fig. 6 Effect of Nonzero Dead-time on
PWM Waveform
on-time of an output is less than one
dead-time period, the output will not
turn on. This is shown in Fig. 6b and
6d. Therefore, the commanded duty
cycle and the actual duty cycle may
differ slightly, especially at extreme
duty cycle values.
Additionally, the dead-time can have
an effect on the voltage applied to
the load by the switching power
bridge; the exact effect is a function
of the direction of the current in the
bridge and the architecture of the
bridge. One should try and choose
the smallest dead-time that will work
with the given switch configuration.
Fig. 6.a and 6.e illustrate the two
duty cycle extremes, 0 % and 100 %.
In these two instances there will
never by a dead-time period, regard-
less of the value programmed in the
dead-time bits, because neither
output ever turns off. Fig. 6b and 6d
a)
b)
Fig. 7 Effect of Changing the Duty
Cycle during a PWM Cycle
t
t
t
t
t
t
PW
PW
PW
PW
PW
PW
= 0
≤ t
> t
< (t
≥ (t
= t
DT
DT
CYCL
CYCL
CYCL
- t
- t
DT
DT
)
)
have only one dead-time period in-
serted in each PWM cycle. In Fig. 6b
the desired ontime of OUT1 is less
than the one dead-time period, there-
fore OUT1 can never turn on. The
same is true for OUT2 in Fig. 6d. Fig.
6c is the normal situation, where both
outputs turn on and off during one
PWM cycle and, as a result, two
dead-time periods are inserted.
Response to a Change in the Pulse
Width Number
One can change the Pulse Width
number at any time. It is not
necessary to synchronize writes to
the Pulse Width latch with the CLK or
the PWM cycle period. The IXDP610
responds to the new Pulse Width
number three clock cycles after the
Pulse Width latch is loaded (1 CLK
cycle after WR goes high). Thus,
OUT1 and OUT2 will immediately
reflect the new Pulse Width number.
The IXDP610 does not wait until the
next PWM cycle to implement a
change in the Pulse Width number.
(See Fig. 7).
The resulting duty cycle is some-
where between the old and the new
duty cycle. The exact value of the
resulting duty cycle depends on when
the Width Latch is loaded (1 CLK
cycle after WR goes high). Thus,
OUT1 and OUT2 will immediately
reflect the new Pulse Width number.
The IXDP610 does not wait until the
next PWM cycle to implement a
change in the Pulse Width number.
Fig. 7a shows what happens when the
Pulse Width number is changed from
20 % to 80 % near the middle of the
PWM cycle. Fig. 7b shows the reverse
situation.
The resulting duty cycle is somewhere
between the old and the new duty
cycle. The exact value of the resulting
duty cycle depends when the Width
latch is loaded (1 CLK cycle after WR
goes high). Thus, OUT1 and OUT2 will
immediately reflect the new Pulse
Width number. The IXDP610 does not
wait until the next PWM cycle to
implement a change in the Pulse Width
number.
IXDP 610
8