CDB150X-01-Z Cirrus Logic Inc, CDB150X-01-Z Datasheet - Page 2
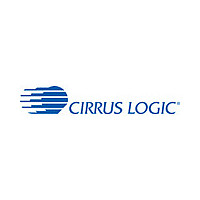
CDB150X-01-Z
Manufacturer Part Number
CDB150X-01-Z
Description
High-efficiency PFC Demo. Board
Manufacturer
Cirrus Logic Inc
Series
-r
Datasheets
1.CDB150X-01-Z.pdf
(16 pages)
2.CDB150X-01-Z.pdf
(16 pages)
3.CDB150X-01-Z.pdf
(16 pages)
4.CDB150X-01-Z.pdf
(2 pages)
Specifications of CDB150X-01-Z
Silicon Manufacturer
Cirrus Logic
Kit Application Type
Power Management
Application Sub Type
Power Factor Correction (PFC)
Kit Contents
Board, Datasheet
Design Resources
CS150x/160x PCB Layout Guidelines Boost Inductance vs. Inductor Size
Featured Product
CS1501/CS1601 Power Factor Correction IC Controllers
Main Purpose
Power Management, Power Factor Correction
Embedded
No
Utilized Ic / Part
CS1501
Primary Attributes
400V, 90W output
Secondary Attributes
90 ~ 265 VAC universal input
Lead Free Status / Rohs Status
Lead free / RoHS Compliant
1. INTRODUCTION
The CS1501 digital power factor correction (PFC) control IC is
designed to deliver the lowest system cost by reducing the
total number of system components and optimizing the EMI
noise signature, which reduces the conducted EMI filter
requirements. The CS1501 digital algorithm determines the
behavior of the boost converter during startup, normal
operation,
overcurrent, and overtemperature).
Figure 1 illustrates a high-level block diagram of the CS1501.
The PFC processor logic regulates the power transfer by
using an adaptive digital algorithm to optimize the PFC
active-switch (MOSFET) drive signal duty cycle and switching
frequency. The adaptive controller uses independent
analog-to-digital converter (ADC) channels when sensing the
feedback and feedforward analog signals required to
implement the digital PFC control algorithm.
The AC mains rectified voltage (on pin IAC) and PFC output
link voltage (on pin IFB) are transformed by the PFC
processor logic and used to generate the optimum PFC
active-switch drive signal (GD) by calculating the optimal
switching frequency and t
An auxiliary winding is typically added to the PFC boost
inductor to provide zero-current detection (ZCD) information.
The ZCD acts as a demagnetization sensor used to monitor
2
and
STBY
IAC
IFB
CS
under
2
ON
1
3
4
fault
600
time on a cycle-by-cycle basis.
V
V
V
DD
DD
DD
15k
15k
600k
V
CS(clamp )
conditions
V
24k
24k
CS(th)
+
+
-
-
ADC
ADC
Figure 1. CS1501 Block Diagram
(overvoltage,
I
I
t
ref
ref
LEB
Threshold
CS Clamp
CS
Regulator
the PFC active-switching behavior and efficiency. The
auxiliary voltage is normalized using an external attenuator
and is connected to the ZCD pin, providing the CS1501 a
mechanism to detect the valley/zero crossings. The ZCD
comparator looks for the zero crossing on the auxiliary winding
and switches when the auxiliary voltage is below zero.
Switching in the valley of the oscillation minimizes the
switching losses and reduces EMI noise.
The PFC controller uses a current sensor for overcurrent
protection. The boost inductor peak current is measured
across an external resistor in the switching circuit on a
cycle-by-cycle basis. An overcurrent fault is generated when
the sense voltage applied to the CS pin exceeds a predefined
reference voltage.
The CS1501 includes a supervisor & protection circuit to
manage startup, shutdown, and fault conditions. The
protection circuit is designed to prevent output overvoltage as
a result of load and AC mains transients. The PFC power
converter main rectified voltage (V
(V
shutdown of the PFC controller. The PFC overvoltage
protection is designed for auto-recovery, i.e. operation resumes
once the fault clears.
Voltage
link
) are monitored for overvoltage faults which would lead to
POR
Zero Crossing
Detect
+
-
V
V
DD (on )
DD (off)
t
ZCB
V
Z
V
+
-
DD
rect
V
ZCD(th)
) and output link voltage
7
6
5
8
DS927PP6
VDD
GD
GND
ZCD